Dry Sand Casting Process An Overview
Dry sand casting is a widely utilized manufacturing process that offers a range of advantages in the production of metal components. This method, a subset of sand casting, involves creating a mold out of dry sand and can efficiently meet the demands of both small and large-scale production runs. The process is particularly valued for its versatility, cost-effectiveness, and ability to produce complex shapes with high dimensional accuracy.
The dry sand casting process begins with the preparation of the sand, which plays a crucial role in the quality of the final product. Unlike traditional sand casting, where sand is typically mixed with a binder and water to create a mold, dry sand casting employs sand that is processed to be devoid of moisture. The dry sand is often mixed with a binder agent, such as resin or a clay-based material, which enhances its strength and refractoriness. This type of sand can be reused multiple times, making it a sustainable choice for manufacturers.
Once the sand is ready, the next step involves forming the mold. The dry sand is packed into a mold box around a pattern, which represents the shape of the desired casting. Since the sand is dry, it can be compacted more densely than wet sand, leading to improved surface finishes and fine details. The compacting process is critical; it often involves the use of vibrating tables or mechanical rammers to ensure that the sand fully encapsulates the pattern and achieves the desired strength.
After the mold has been formed and allowed to harden, the pattern is removed carefully, creating a cavity within the sand that precisely mirrors the intended final product. At this point, the mold is inspected for defects and is assembled into two or more halves if necessary, ensuring a proper fit for the casting process.
dry sand casting process
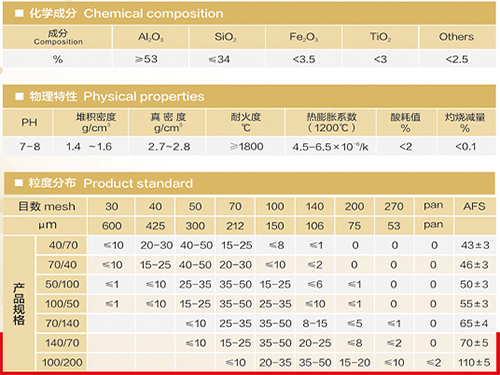
The next phase is melting the metal, which is typically done in a furnace. The choice of metal depends on the intended application; common materials used in dry sand casting include aluminum, brass, bronze, and iron. Once the metal reaches its molten state, it is poured into the prepared sand mold. The dry nature of the sand minimizes the possibility of moisture reaction, which can lead to pouring defects such as porosity or gas entrapment, thus ensuring a cleaner cast.
After the molten metal fills the cavity, it is allowed to cool and solidify, resulting in a solid piece of metal that takes the shape of the mold. Cooling times can vary depending on the thickness of the casting and the type of metal used. Once solidified, the mold is broken away to reveal the casting, which may require further finishing operations such as grinding, machining, or surface treatment, depending on the specifications of the final product.
One of the significant advantages of dry sand casting is its ability to produce intricate shapes with excellent dimensional accuracy. This process allows for tight tolerances and reduces the need for extensive machining, thereby lowering production costs. Additionally, the durability and thermal properties of the dry sand make it suitable for casting a variety of metals, contributing to its widespread use across different industries, including automotive, aerospace, and general manufacturing.
In conclusion, the dry sand casting process is a vital method in modern metal casting practices, combining efficiency, versatility, and cost-effectiveness. As technology advances, innovations such as automated sand preparation and computer-aided design (CAD) are further enhancing the capabilities of dry sand casting. This process not only supports the creation of complex geometries but also aligns with the growing demand for sustainable manufacturing practices. With its myriad benefits, dry sand casting will continue to play a crucial role in the production of high-quality metal components for years to come.
Post time:ნოე . 07, 2024 23:21
Next:Pros and Cons of Sand Casting Method in Manufacturing Production