Advantages and Disadvantages of Sand Casting
Sand casting is one of the oldest and most versatile metal casting techniques used in manufacturing. This method involves pouring molten metal into a mold formed from sand, which can be an excellent choice for producing complex shapes and large components. However, like any manufacturing process, sand casting has its advantages and disadvantages. Understanding these can help engineers and manufacturers make informed decisions when choosing the appropriate casting method for their projects.
Advantages of Sand Casting
1. Cost-Effective One of the most significant advantages of sand casting is its cost-effectiveness, especially for low to medium production runs. The materials used, predominantly sand and metal, are relatively inexpensive. Additionally, the process does not require costly equipment or tooling compared to other casting methods, making it accessible for smaller operations and startups.
2. Versatility in Shapes and Sizes Sand casting can produce a wide range of shapes and sizes, from small intricate items to large components weighing several tons. The flexibility of the molding process allows for complex designs that may be challenging to achieve with other casting methods. This versatility makes sand casting suitable for various industries, including automotive, aerospace, and construction.
3. Material Variety This method can accommodate various metals and alloys, including aluminum, iron, bronze, and magnesium. The ability to cast different materials expands the applications of sand casting across multiple sectors.
4. Ease of Modifications The sand mold can be easily modified to accommodate design changes. If revisions are needed, only the sand mold needs adjustment, making it less time-consuming and expensive than other methods that may require new tooling.
5. Good Surface Finish and Dimensional Accuracy Although sand casting may not offer the same precision as other casting methods, it can still achieve satisfactory surface finishes and dimensional tolerances with proper techniques. For many applications, the quality meets the required standards.
6. Efficiency for Low-Volume Production Sand casting is particularly efficient for low-volume production runs. The quick turnaround time for creating molds and the simplicity of the casting process make it an ideal choice for prototype development or custom parts.
advantages and disadvantages of sand casting
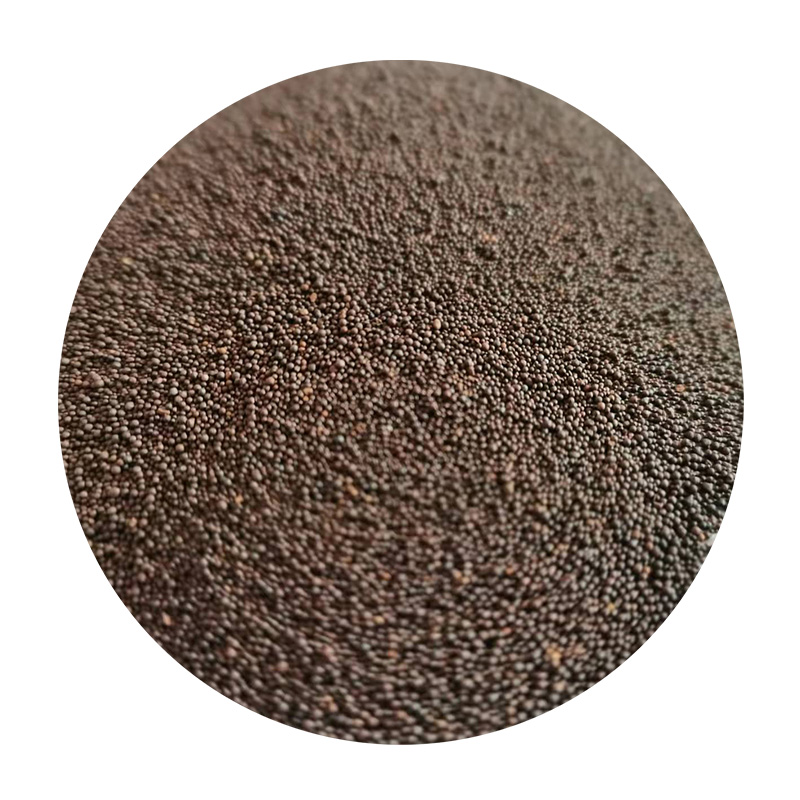
Disadvantages of Sand Casting
1. Surface Finish Quality While sand casting can produce acceptable surface finishes, it generally does not match the smoothness of other casting methods such as investment casting or die casting. This limitation may necessitate additional machining or finishing processes, which can increase overall production costs.
2. Labor-Intensive Sand casting can be labor-intensive, requiring skilled workers to prepare molds, handle molten metal, and carry out finishing operations. The reliance on manual labor can slow down the production process and potentially lead to inconsistencies in the final product.
3. Porosity Issues One of the common challenges in sand casting is the potential for porosity in the finished product. Gas may become trapped within the mold, leading to voids or weak spots in the casting. This issue can compromise the integrity of the final component, especially in critical applications.
4. Limitations on Wall Thickness The thickness of the walls in sand-cast components is often limited. Thick sections can lead to uneven cooling, resulting in warping or cracking. As a result, engineers must carefully consider wall thickness during the design phase.
5. Longer Lead Times Although sand casting is suitable for low-volume production, the lead time for setup may be longer than for other methods, especially when creating complex molds. This factor can impact time-sensitive projects or those requiring rapid prototyping.
6. Environmental Concerns The use of sand as a mold material raises environmental concerns, particularly in terms of sand depletion and the potential for dust pollution. Additionally, the disposal of used sand and binders can pose environmental challenges that manufacturers must address.
Conclusion
In summary, sand casting is a widely used manufacturing process with its unique set of advantages and disadvantages. Its cost-effectiveness, versatility, and ability to accommodate various materials make it an attractive option for many applications. However, challenges related to surface finish quality, labor intensity, and porosity must be considered when deciding on the best casting method. By weighing these factors, manufacturers can make informed choices that align with their production needs and quality requirements, ultimately driving efficiency in their operations.
Post time:ნოე . 05, 2024 21:45
Next:golden sands for sale