Understanding Foundry Sand Testing A Key to Quality Casting
Foundry sand testing plays a crucial role in the manufacturing process of metal castings, serving as the backbone of quality assurance in foundries. A meticulous evaluation of sand properties is essential for achieving consistent, high-quality castings in various industries, including automotive, aerospace, and machinery. This article delves into the significance of foundry sand testing, key parameters to be evaluated, and the methodologies employed in the testing process.
Importance of Foundry Sand Testing
The quality of sand directly affects the performance of the casting process. Variations in sand properties can lead to defects such as inclusions, poor surface finish, or dimensional inaccuracies. Thus, rigorous sand testing helps identify potential issues before the casting process begins, minimizing waste and preventing costly revisions.
Foundry sand testing serves several critical purposes
1. Quality Control Consistent sand quality ensures that the casting process runs smoothly and the final products meet specifications. 2. Cost Efficiency By identifying and addressing issues early, foundries can save on raw materials and labor costs associated with rework and scrap.
3. Process Optimization Understanding sand characteristics allows for fine-tuning of the casting process, resulting in improved efficiency and reduced cycle times.
Key Parameters in Sand Testing
When testing foundry sand, several key parameters must be evaluated to ensure optimal performance. Some of the most critical aspects include
1. Grain Size Distribution The size and distribution of sand grains affect permeability, strength, and the overall finish of the castings. A well-graded sand mix balances fine and coarse particles.
2. Moisture Content The amount of moisture in the sand affects its bonding ability and can impact the final casting quality. Control of moisture content is vital for preventing defects.
foundry sand testing
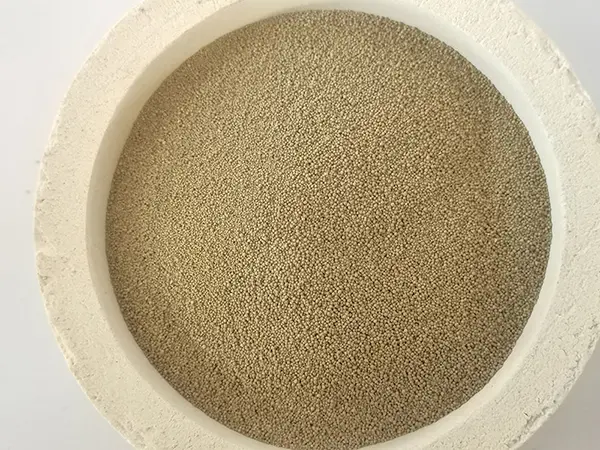
3. Clay Content Clay particles enhance the binding properties of the sand but excessive amounts can lead to sticking, leading to defects in the casting.
4. Permeability This measures how easily gases can escape from the mold during pouring. Proper permeability is critical to prevent blowholes and other gas-related defects.
5. Compressive Strength The strength of the sand mixture is vital for maintaining the mold's integrity during the casting process. Insufficient strength can result in mold collapse.
Methodologies for Sand Testing
Several standardized methodologies are employed in foundry sand testing, including
1. Sieve Analysis A mechanical process that determines the grain size distribution of the sand mixture. This ensures that the right proportions of fine and coarse sands are used.
2. Moisture Tests Various methods, such as infrared drying or the use of moisture meters, gauge moisture levels to ensure the mix adheres to specifications.
3. Permeability Tests Often measured using a permeability meter, this test assesses how well air can flow through the sand, ensuring it is suitable for the casting process.
4. Strength Tests Techniques such as the use of a universal testing machine help to determine the compressive strength of the sand mixture.
5. Plasticity Tests Evaluating the plasticity of the sand ensures proper moldability and adhesion during the casting process.
In conclusion, foundry sand testing is an essential step in the casting process that ensures product quality and consistency. By rigorously analyzing key parameters and employing standardized methodologies, foundries can enhance their production processes, reduce waste, and ultimately deliver superior castings. As industries continue to demand high standards, the importance of effective foundry sand testing will only continue to grow.
Post time:Dec . 13, 2024 11:05
Next:what is resin coated sand