Advantages and Disadvantages of Sand Casting
Sand casting, one of the oldest and most widely used metal casting processes, offers a range of benefits and drawbacks that manufacturers must consider when selecting a method for producing metal parts. Understanding these advantages and disadvantages is key to making informed decisions in production processes.
Advantages of Sand Casting
1. Versatility in Materials Sand casting is compatible with a wide variety of metals, including iron, aluminum, bronze, and steel. This versatility allows manufacturers to select the most suitable material for their specific application, which can enhance product performance and durability.
2. Cost-Effectiveness One of the most significant advantages of sand casting is its cost-effectiveness, especially for low to medium production volumes. The materials used, such as sand and binders, are relatively inexpensive, and the molds can be reused multiple times, effectively reducing material costs over time.
3. Complex Shapes Sand casting is ideally suited for producing complex geometries and intricate designs. The pliability of sand allows for the creation of complex molds that can capture fine details, which may be difficult to achieve with other casting methods. This capability makes sand casting popular for creating one-of-a-kind prototypes and custom components.
4. Large Component Production Sand casting can accommodate large-scale components that might be challenging for other casting processes. By using larger sand molds, manufacturers can create heavy parts with intricate shapes, making it suitable for a variety of industries, including automotive, aerospace, and heavy machinery.
5. Environmental Impact Modern sand casting techniques can minimize waste and promote recycling. Used sand can often be reclaimed and reused in new molds, significantly reducing the environmental footprint of the casting process.
advantages and disadvantages of sand casting
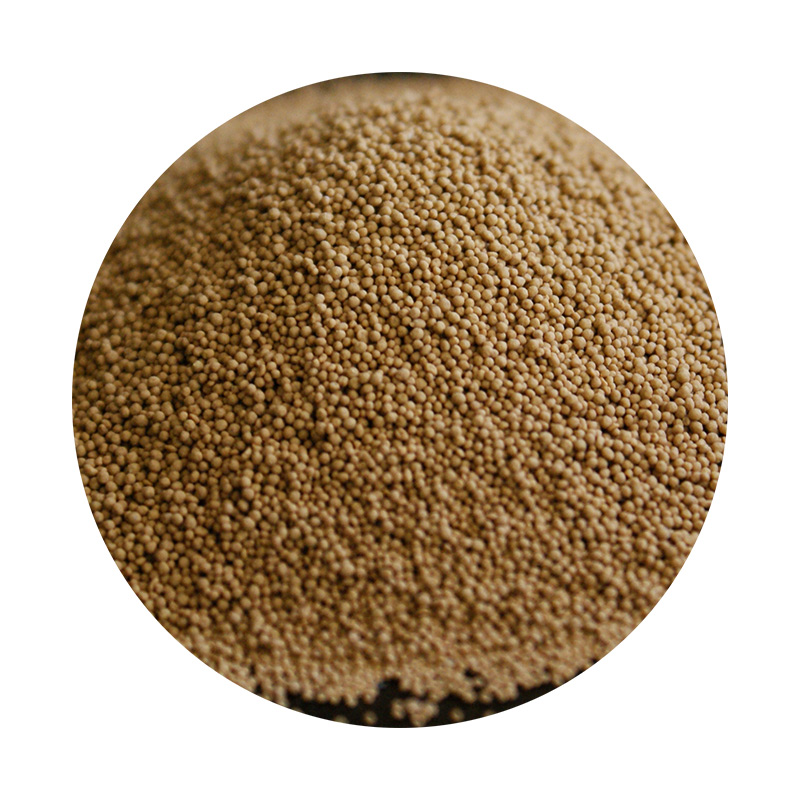
Disadvantages of Sand Casting
1. Surface Finish and Tolerance While sand casting can produce complex shapes, the surface finish often requires additional machining to achieve a smooth finish. Additionally, the tolerances achieved in sand casting are typically not as precise as those obtained through processes like investment casting or die casting, which can affect the final product's functionality.
2. Labor-Intensive The process of creating sand molds can be labor-intensive, requiring skilled workers to ensure quality and precision. This reliance on manual labor can lead to higher labor costs and longer production times compared to automated casting methods.
3. Dimensional Variability Due to the nature of sand molds, there can be variability in dimension and weight. This inconsistency arises from factors such as temperature, humidity, and the sand's compaction quality, which can impact the final product’s precision and reliability.
4. Limited Production Rates Although sand casting is cost-effective for low to medium volumes, it is not necessarily the fastest method for mass production. The process involves several stages – from mold making to pouring and cooling – which can slow down production rates. For high-volume production, other methods like die casting might be more efficient.
5. Strength Limitations The mechanical properties of sand-cast parts can vary based on the metal used and the casting process. Sand-cast components may not achieve the same tensile strength or overall mechanical performance as those produced through more controlled processes.
Conclusion
In summary, sand casting is a versatile and cost-effective manufacturing technique that offers numerous advantages, including the ability to produce complex shapes and accommodate a wide range of metals. However, it also has its share of disadvantages, such as variability in tolerances and the need for post-processing. As with any manufacturing method, companies must carefully evaluate the specific requirements of their projects to determine if sand casting is the most suitable choice for their needs.
Post time:Nov . 25, 2024 11:03
Next:Optimizing Sanding Techniques for Enhanced Ceramic Surface Finishing