Understanding Sand Casting A Comprehensive Overview
Sand casting is one of the oldest and most widely used metal casting processes in the manufacturing industry. This versatile method involves the creation of metal parts by pouring molten metal into a mold made of sand. Its simplicity, cost-effectiveness, and adaptability to various metals make sand casting a preferred choice for many industrial applications. In this article, we will explore the fundamentals of sand casting, its process, benefits, and applications.
What is Sand Casting?
Sand casting, sometimes referred to as sand mold casting, utilizes a mold made from sand to shape liquid metal. The process typically involves several steps, including pattern making, mold preparation, pouring, and final finishing. Sand casting can accommodate a wide range of metals, including aluminum, iron, steel, and bronze, making it suitable for producing complex shapes.
The Sand Casting Process
The sand casting process can be broken down into several key stages
1. Pattern Making The first step involves creating a pattern of the final product. A pattern is a replica of the object to be cast, typically made from materials such as wood or metal. Patterns can be single-piece or multi-piece, depending on the complexity of the design.
2. Mold Preparation The mold is created by compacting sand around the pattern. The sand used in the process is typically a mixture of silica sand, clay, and water, which helps bind the sand particles together. Once the mold is formed, the pattern is removed, leaving a cavity that reflects the shape of the desired object.
3. Pouring After mold preparation, the molten metal is poured into the mold cavity. Care must be taken to control the pouring temperature and speed to avoid defects such as air pockets or oxidation.
4. Cooling Once the metal has cooled and solidified, the mold is broken away, revealing the cast object. This stage may require additional processes to remove any sand or imperfections on the surface.
5. Finishing The final step involves finishing operations such as machining, grinding, or polishing to achieve the desired dimensions and surface quality of the cast product.
Advantages of Sand Casting
what is sand casting
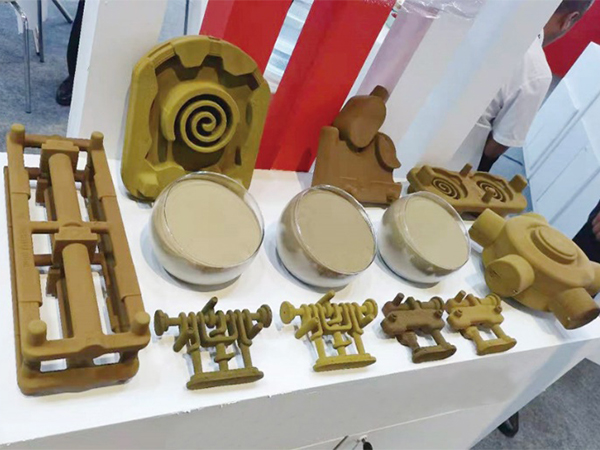
Sand casting offers several advantages over other casting methods, making it a popular choice among manufacturers
- Cost-Effective The materials used in sand casting, particularly sand, are inexpensive and readily available. This low setup cost makes it an economically viable option, especially for small production runs.
- Versatility Sand casting can accommodate a variety of metals and alloys, as well as complex geometries. This flexibility allows for the production of diverse components, from small parts to large machinery.
- Scalability The sand casting process can be scaled up or down, making it suitable for both prototype development and mass production.
- Good Dimensional Accuracy While sand casting may not achieve the same precision as methods like investment casting, advancements in technology and techniques have improved its accuracy, making it suitable for many applications.
Applications of Sand Casting
Sand casting is employed in various industries, including automotive, aerospace, construction, and art. Common applications include
- Automotive Parts Many components, such as engine blocks, transmission cases, and housings, are produced using sand casting due to the process's ability to handle complex shapes and large production volumes.
- Aerospace Components High-performance components, including turbine casings and structural supports, often utilize sand casting for its ability to produce lightweight yet strong parts.
- Artistic Casting Artists frequently use sand casting to create sculptures and decorative items, allowing for unique designs and intricate details.
Conclusion
Sand casting is a time-honored manufacturing process that continues to play a crucial role in various industries. With its cost-effectiveness, versatility, and ability to produce complex shapes, it remains a popular choice for producing high-quality metal components. As technology advances, sand casting will likely evolve further, paving the way for even greater innovations in manufacturing. Whether for practical functions or artistic creations, sand casting's rich history and enduring applications highlight its importance in the world of metalworking.
Post time:11月 . 05, 2024 23:19
Next:Understanding the Process and Benefits of Sand Casting for Iron Products