Understanding Materials Used in Sand Casting
Sand casting is one of the oldest and most widely used metal casting processes, renowned for its versatility and effectiveness in producing complex shapes and large components. The process relies on a mixture of materials that create a mold capable of withstanding molten metal. The choice of materials is crucial as it influences the quality, efficiency, and properties of the final product. This article explores the main materials used in sand casting.
1. Sand
The primary material used in sand casting is sand, specifically shaped grains of silica (SiO₂). Silica sand is preferred due to its high melting point and ability to withstand high temperatures. The sand used in the casting process is often mixed with a binding agent, typically clay, which helps maintain the mold structure and prevents it from collapsing when molten metal is poured into it. The most common type of clay used is bentonite, known for its excellent binding properties.
2. Binder
Binders play a critical role in ensuring the cohesion of sand grains. In addition to clay, other binders may be used, such as resin-based systems, which enhance the mold strength and reduce the tendency for defects in castings. These binders can provide better surface finishes and greater dimensional accuracy, making them ideal for producing intricate designs.
3. Additives
what materials are used in sand casting
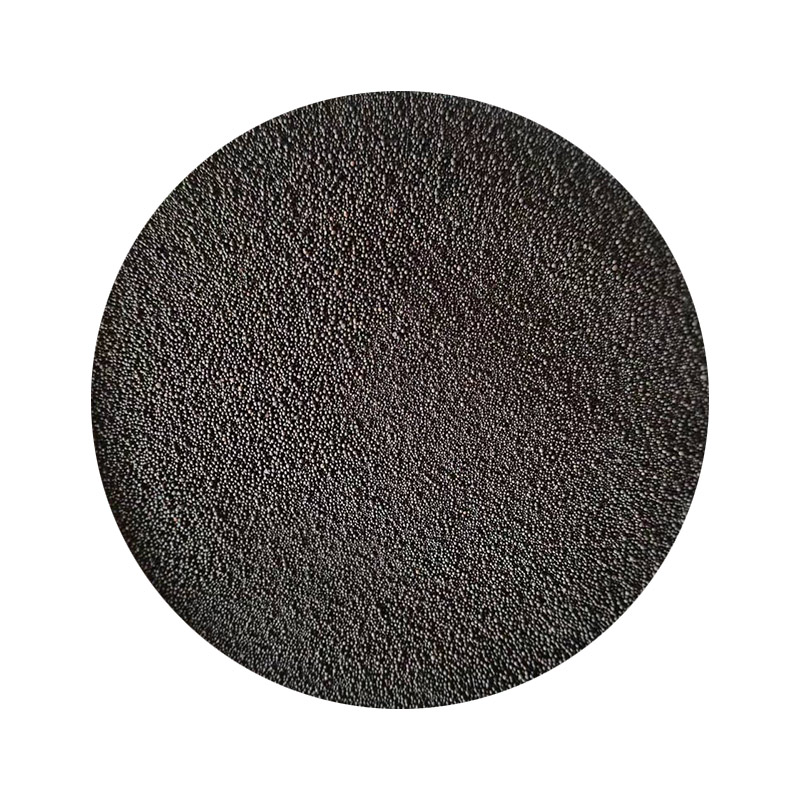
To improve the performance of the sand mixture, various additives may be introduced. These include materials that enhance the thermal properties, reduce expansion during heating, and improve the mold's ability to release the casting once cooling is complete. For instance, additives like sea coal or carbon may be mixed with sand to enhance mold strength while also providing a smoother surface finish.
4. Metals
The molten metal that is poured into the sand mold can vary widely, with common choices including aluminum, iron, and bronze. The type of metal used is often determined by the application and the desired properties of the final product. For example, aluminum alloys are prized for their lightweight properties and corrosion resistance, while cast iron is favored for its durability and high wear resistance.
5. Core Materials
In projects requiring hollow sections, cores made from sand or metal are employed. Sand cores are often made from the same sand mixture as the mold, whereas metal cores provide greater strength and stability, especially for complex inner geometries.
In conclusion, the materials utilized in sand casting—ranging from silica sand and binders to various metals and cores—are fundamental to the process's success. The careful selection and combination of these materials enable manufacturers to produce high-quality castings tailored to specific applications, reinforcing sand casting's enduring relevance in modern manufacturing.
Post time:9月 . 14, 2024 10:14
Next:3d sand printer price