Types of Sand Used in Foundry
In the world of foundry casting, sand plays a pivotal role, as it serves as a primary material for mold-making. The type of sand used can greatly affect the quality and characteristics of the cast product. Here’s an overview of the main types of sand utilized in the foundry industry.
1. Green Sand
Green sand is the most common type of sand used in foundries. It is a mixture of silica sand, clay, and water. The term green refers to the moisture content present in the sand prior to molding. Green sand’s properties allow for excellent casting and molding characteristics. The clay gives the sand cohesiveness, while the moisture helps in binding the particles together. This type of sand is favored for its ability to produce intricate designs and its cost-effectiveness, making it the choice for many foundries.
2. Dry Sand
Unlike green sand, dry sand is free from moisture. This makes it suitable for applications where a quick setting time is essential. Dry sand is typically mixed with a binding agent to enhance its strength and durability. It is commonly used for producing large molds and cores that require high dimensional accuracy. Its lack of moisture also reduces the risk of defects caused by steam or gas during the casting process, resulting in smoother finishes on the final product.
types of sand used in foundry
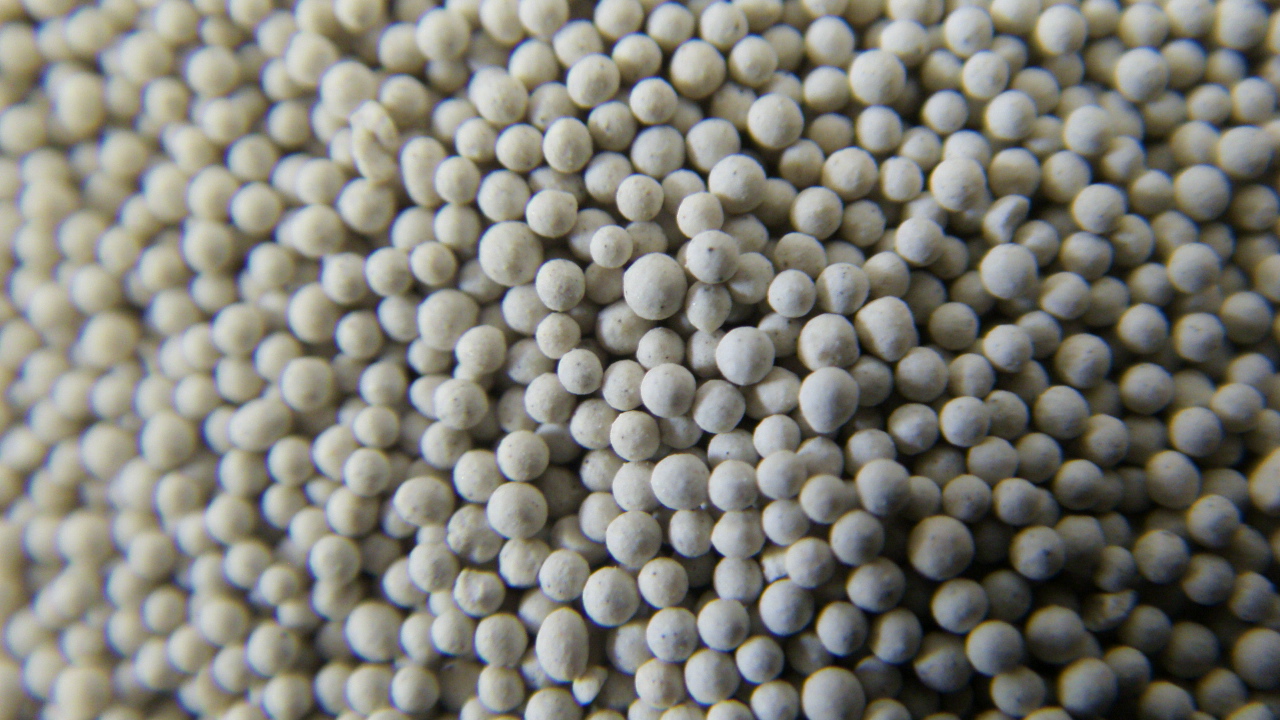
3. Nobake Sand
Nobake sand is another widely used material in foundries. It is a mixture of silica sand and a chemical binder, which is activated by heat rather than moisture. This sand is typically used for larger casting applications requiring superior strength and stability. Nobake molds are created by packing the sand around a pattern, with the heat from the molten metal setting the binder. This process allows for intricate designs and reduces the risk of mold deterioration during the casting process.
4. Resin Sand
Resin sand is processed with a phenolic resin binder that provides exceptional heat resistance and strength. This type of sand is favored for its ability to produce high-quality surface finishes and is often used in the casting of high-performance components. The resin binding system enhances the sand's stability during the casting process, producing molds that can withstand extreme temperatures and varying metal alloys.
Conclusion
The choice of sand in foundry applications is critical in determining the quality and effectiveness of the final cast product. Each type of sand has distinct properties and advantages, making it suitable for different casting processes. Understanding these differences is essential for foundry professionals to optimize production, meet specifications, and ultimately ensure the success of their foundry operations. In an industry where precision is key, the right type of sand can make all the difference.
Post time:9月 . 03, 2024 09:58
Next:sand casting mass production