Sand Printing Casting An Innovative Approach in Manufacturing
In the ever-evolving realm of manufacturing, new technologies often emerge to improve efficiency, reduce costs, and enhance product quality. One of the most fascinating advancements in recent years is sand printing casting, a method that seamlessly combines traditional sand casting with modern additive manufacturing techniques. This innovative approach not only streamlines the casting process but also opens up a realm of possibilities for designers and engineers.
Understanding Sand Casting
Sand casting has long been a staple method in metalworking, famous for its ability to create complex shapes economically. The process involves creating a mold from sand, into which molten metal is poured to form desired components. Traditionally, the creation of these molds can be labor-intensive, requiring significant manual labor to sculpt the design into the sand, followed by curing or hardening the mold. However, the introduction of 3D printing technology to this age-old process has revolutionized how manufacturers approach sand casting.
The Evolution of Sand Printing Casting
Sand printing casting, often referred to as 3D sand printing, utilizes advanced printing technology to create molds from sand with a binding agent, layer by layer. This process begins with a computer-aided design (CAD) model of the desired part. The 3D printer then translates this design into a series of fine layers of sand, binding them together with a sophisticated adhesive. Once the mold is completed, it can be used for pouring molten metal, producing intricate parts with precision and speed.
This technology eliminates many of the constraints associated with traditional sand casting. For example, complex geometries that would have required elaborate tooling and extended lead times can now be printed quickly and efficiently. Moreover, the flexibility in design allows engineers to experiment with shapes that are lighter and more robust, ultimately leading to performance enhancements in the final product.
Benefits of Sand Printing Casting
One of the most significant advantages of sand printing casting is the reduction of material waste. Traditional casting methods often involve excess material that must be machined away after the component is cast. In contrast, sand printing allows for precise layer control, thereby minimizing waste and reducing costs. Additionally, the production of molds is faster, which translates into shorter lead times and quicker turnaround for prototypes and production runs.
sand printing casting
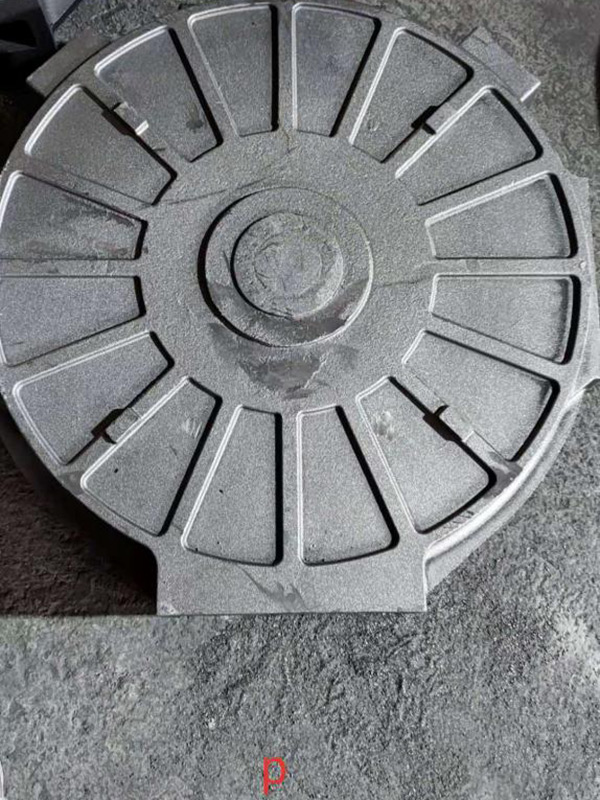
Another critical benefit is the ability to produce molds without the need for complex tooling. This feature significantly lowers the barrier for customization, enabling rapid iterations based on design feedback. Manufacturers can quickly adjust the CAD model to create new molds without the need for extensive machining or setup changes, fostering a more agile and responsive production environment.
Applications Across Industries
The versatility of sand printing casting makes it applicable in various industries, including automotive, aerospace, and art. In the automotive sector, for example, manufacturers can create lightweight yet durable components that contribute to fuel efficiency and performance. Similarly, in aerospace, complex parts that require high precision and strength can be produced faster and at a lower cost compared to traditional methods.
Moreover, artists and designers have embraced sand printing casting to create intricate sculptures and functional art pieces that push the boundaries of creativity. By leveraging this technology, they can realize visions that were once constrained by traditional manufacturing limitations.
Challenges and Future Prospects
Despite its numerous advantages, sand printing casting is not without challenges. Material properties of printed molds must be meticulously controlled to ensure they can withstand the rigors of molten metal. Additionally, the technology, while growing, is still relatively new, and widespread adoption may require further advancements in printer technology and materials.
Looking ahead, the future of sand printing casting appears promising. As technology continues to evolve, enhancements in speed, precision, and material formulations will likely expand its capabilities. Furthermore, as industries increasingly prioritize sustainability, the eco-friendly nature of sand printing casting—by reducing waste and allowing for the reuse of materials—positions it as a key player in the future of manufacturing.
In summary, sand printing casting represents a significant step forward in the engineering and manufacturing landscape. By merging traditional casting techniques with modern technology, it not only boosts efficiency and reduces costs but also empowers innovation across industries. As this technology matures, it will undoubtedly change how we conceive, design, and produce objects in the future.
Post time:12月 . 20, 2024 14:34
Next:what is sand casting process