Sand for Metal Casting An Essential Component in Foundry Processes
Metal casting is a crucial manufacturing process that transforms molten metal into desired shapes and components, and one cannot overlook the pivotal role played by sand in this procedure. Sand has been utilized in metal casting for centuries, serving as a mold material that provides the necessary shape and support to the molten metals. This article aims to explore the types of sand, its properties, and its significance in the metal casting industry.
Types of Sand Used in Metal Casting
There are various types of sand suited for metal casting purposes, with the most common being silica sand. Silica sand is composed primarily of silicon dioxide (SiO2) and is favored for its high melting point, good thermal conductivity, and availability. However, there are other types of sand used depending on the specific needs of the casting process
1. Green Sand This is a mixture of silica sand, clay, and water. The term green refers to its moisture content rather than its color. Green sand has excellent mold-making properties and is cost-effective, making it popular in foundries for ferrous and non-ferrous casting.
2. Dry Sand Unlike green sand, dry sand is used after it has been thoroughly dried. Dry sand molds are more rigid and better suited for intricate designs. The lack of moisture in these molds makes them ideal for casting metals that require high precision.
3. Resin Sand This type of sand is coated with resin, which hardens when heated. Resin sand molds offer superior dimensional accuracy, surface finish, and strength, making them ideal for high-performance casting applications, although at a higher cost.
4. Shell Molding Sand Shell molding uses a mixture of fine sand and thermosetting resin. The sand is applied to a heated metal pattern, creating a thin shell that hardens. Shell molds are known for their excellent surface finish and dimensional accuracy.
5. Investment Casting Sand Used primarily in investment casting, this sand is made from fine particles and is typically coated with a ceramic material to improve its refractory properties.
Properties of Sand for Metal Casting
The effectiveness of sand in metal casting is determined by its physical and chemical properties. Key characteristics of casting sand include
- Grain Size The size of the sand grains affects the mold's permeability and strength
. Finer sands can produce smoother surfaces but may also lead to increased resistance to gas escape.sand for metal casting
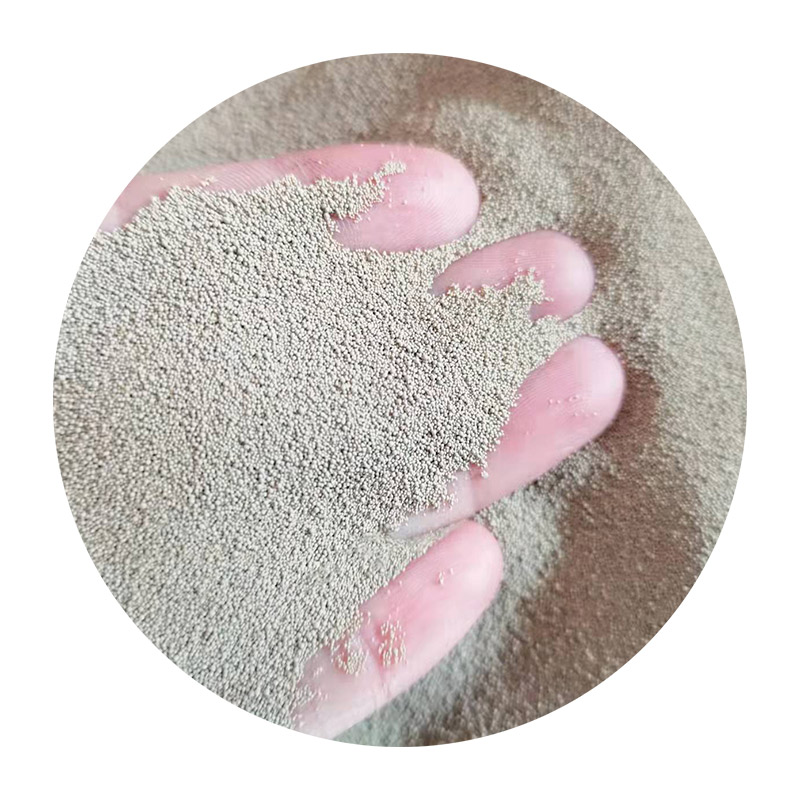
- Shape The shape of the sand grains influences the packing density. Angular grains can provide better strength, while spherical grains may offer improved flowability.
- Thermal Stability The ability of sand to withstand high temperatures is crucial in preventing mold deformation during the casting process. High thermal stability ensures that the mold can endure the molten metal pouring without degrading.
- Binding Properties The type and amount of binder used (such as clay or resin) significantly affect the sand's cohesiveness, strength, and ability to hold its shape.
Significance of Sand in Metal Casting
Sand plays an indispensable role in the metal casting process for several reasons
1. Mold Formation The primary function of sand in metal casting is to form molds that define the shape of castings. The ability to produce complex geometries makes sand molds incredibly versatile.
2. Heat Resistance The high melting point of silica sand means it can withstand the temperatures of molten metals, maintaining the integrity of the mold.
3. Cost-Effectiveness Sand, particularly green sand, is inexpensive and abundant, making it a favorite choice in foundries worldwide.
4. Reusability Many types of casting sand can be reused multiple times, reducing waste and economic costs.
5. Improved Surface Finish The right type of sand can significantly enhance the surface quality of castings, reducing the need for further finishing processes.
Conclusion
In summary, sand is a fundamental element in the metal casting industry, providing the necessary properties and functionality required to produce high-quality castings. Its versatility and efficacy have made it a long-standing choice within foundries, from the production of simple components to complex assemblies. As technology advances, the formulation and processing of casting sands continue to evolve, ensuring that they meet the demands of modern manufacturing practices while maintaining their essential role in the metal casting process. Understanding the various types of sand and their properties is crucial for any foundry looking to optimize its casting process and achieve the best possible results.
Post time:11月 . 09, 2024 09:56
Next:Understanding the Benefits and Applications of Resin Coated Sand in Modern Industries