Sand Casting A Timeless Manufacturing Process
Sand casting, also known as sand mold casting, is one of the oldest and most widely used metal casting processes in the manufacturing industry. Its unique combination of versatility, cost-effectiveness, and ease of use makes it a preferred choice for producing complex shapes and large components across various industries, including automotive, aerospace, and heavy machinery.
The Basics of Sand Casting
The fundamental principle of sand casting involves creating a mold from sand and then pouring molten metal into this mold to create a desired shape. The process begins with the design of a pattern, often made from wood, plastic, or metal, which mimics the final product's dimensions. This pattern is then pressed into a mixture of sand and a binding agent, forming two halves of a mold the cope (top half) and the drag (bottom half).
Once the mold is prepared, it is typically coated with a release agent to facilitate the removal of the final casting. After the mold halves are assembled, molten metal is poured inside, filling the cavity created by the pattern. Once the metal cools and solidifies, the mold is broken away to reveal the finished part, which may require additional machining to meet specific tolerances and surface finishes.
Advantages of Sand Casting
One of the main advantages of sand casting is its flexibility. It can accommodate a wide range of metals, including aluminum, iron, and bronze, making it suitable for diverse applications. The process can also produce intricate shapes and large components that would be difficult or impossible to achieve with other methods.
Additionally, sand casting is relatively cost-effective, especially for low to medium production runs. The materials used in sand casting, primarily sand and binding agents, are inexpensive and readily available. Moreover, the reusable nature of sand allows manufacturers to recycle the sand after the casting process, further reducing waste and costs.
Process Variations
sand casting
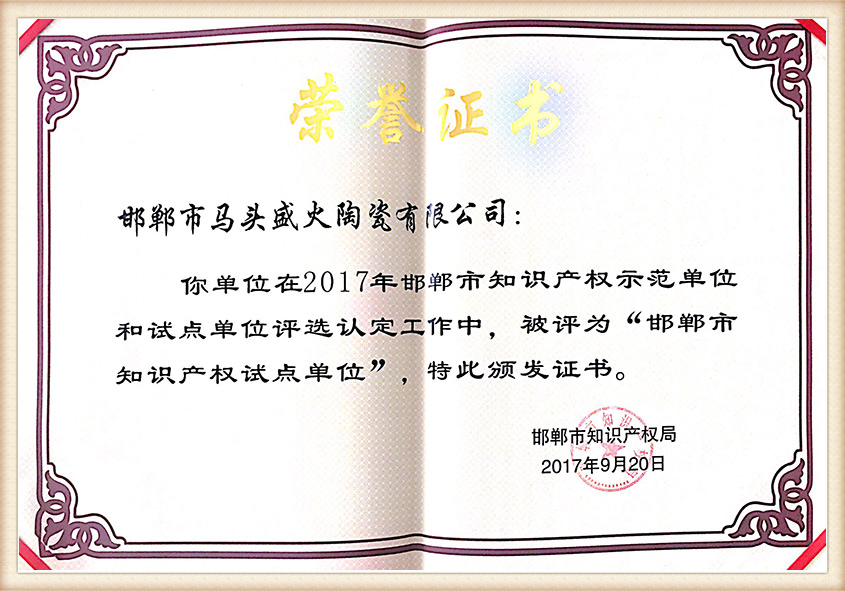
While conventional sand casting remains popular, several variations have emerged to enhance its efficiency and precision. Some notable variations include
1. Green Sand Casting This method utilizes a mixture of sand, clay, and water to create a mold that retains moisture. It's the most commonly used type of sand casting due to its simplicity and effectiveness.
2. Dry Sand Casting In this variation, the sand mold is hardened with a binder cured by heat. Dry sand molds can withstand higher temperatures and offer improved dimensional accuracy.
3. CO2 Sand Casting This process involves the use of CO2 gas to harden the sand mixture, resulting in molds that provide excellent detail and surface finish.
4. Lost Foam Casting An innovative approach that replaces traditional patterns with foam models, which evaporate upon contact with molten metal, leaving a cavity for casting.
Applications of Sand Casting
Sand casting is utilized across various industries to produce intricate and robust parts. In the automotive industry, it is commonly used for creating engine blocks, transmission cases, and various structural components. The aerospace industry relies on sand casting for manufacturing complex shapes like turbine housings and brackets. Additionally, heavy machinery and construction equipment often utilize sand casting for durable parts that can withstand significant wear and tear.
Conclusion
Sand casting remains a vital manufacturing process due to its adaptability and effectiveness in producing high-quality metal parts. As technology advances, innovations in sand casting techniques continue to improve efficiency and product quality, ensuring that this timeless method will remain relevant in the ever-evolving landscape of manufacturing. Whether for small-scale applications or large industrial components, sand casting will always hold a special place in the heart of metalworking.
Post time:12月 . 14, 2024 04:31
Next:Evaluation and Insights on Sand Casting Techniques and Their Applications in Modern Manufacturing