Sand Cast Foundry An Essential Backbone of Modern Manufacturing
The sand casting process is one of the oldest and most widely used manufacturing methods in the foundry industry. It involves pouring molten metal into a sand mold to create complex parts and components. This method is not only versatile and cost-effective but also allows for the production of intricate designs, making it a cornerstone of modern manufacturing.
The Basics of Sand Casting
Sand casting begins with the creation of a mold. The mold is typically made from a mixture of sand, clay, and water, which is compacted to hold its shape. The sand used in this process is usually silica sand, known for its high melting point and ability to withstand the heat of molten metal. A pattern, which represents the object to be cast, is placed in the sand to form the cavity in which the metal will be poured.
Once the mold is prepared, it is important to ensure that it can withstand the pressure of the molten metal. The sand mold is often treated with various chemicals to enhance its properties, such as increasing its strength and reducing any defects that might arise during the casting process.
The Pouring Process
After the mold is ready, the next step is the pouring of the molten metal. This metal can be a variety of alloys, including aluminum, iron, or magnesium, depending on the desired properties of the final product. The molten metal is heated to a specific temperature, making it less viscous for easier pouring.
Once poured, the metal fills the mold cavity, taking the shape of the pattern. This process requires precision and timing; the temperature of the molten metal must be closely monitored to avoid defects such as gas porosity or cold shuts - where the metal fails to fuse properly during pouring.
Cooling and Finishing
sand cast foundry
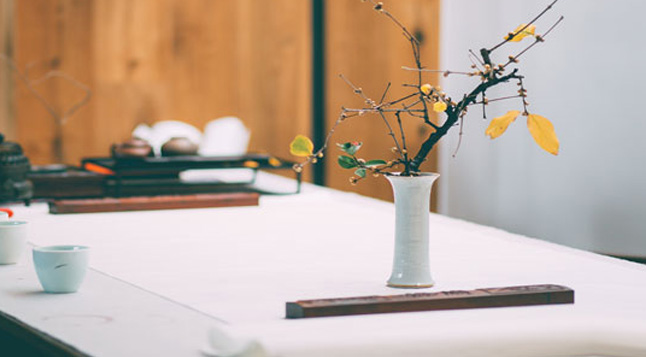
After the molten metal has cooled and solidified, the next step is removing it from the mold. This is typically done by carefully breaking away the sand to reveal the cast metal component. In some cases, the sand can be reused for future molds, making sand casting an environmentally friendly option.
Once the part is removed, it may require finishing processes such as machining, grinding, or polishing to achieve the desired surface finish and dimensional accuracy. Depending on the complexity of the component, additional processes such as heat treatment may be applied to enhance mechanical properties.
Applications and Advantages
The versatility of sand casting makes it widely used across various industries. It is particularly favored in sectors like automotive, aerospace, and construction, where complex shapes and large components are frequently required. Because it can accommodate a wide range of metal alloys, sand casting is an ideal choice for producing everything from small parts to large heavy machinery.
One of the main advantages of sand casting is its cost-effectiveness. The production of sand molds is less expensive compared to other types of molds, making it a viable option for both small-scale and mass production. Additionally, the process is relatively quick, which helps to reduce lead times for product delivery.
Challenges and Innovations
Despite its many benefits, sand casting also faces challenges, such as dimensional tolerances and surface finish quality. Advances in technology, such as computer-aided design (CAD) and 3D printing, are being integrated into the sand casting process to overcome these issues. These innovations allow for the creation of more precise molds and patterns, leading to improved cast quality and reduced waste.
Conclusion
In conclusion, the sand cast foundry plays a vital role in the manufacturing landscape. Its ability to produce complex, high-quality components at a relatively low cost makes it indispensable. As technology continues to evolve, the sand casting process will inevitably adapt, ensuring its relevance and efficiency in future manufacturing endeavors. The enduring appeal of sand casting highlights its importance not only as a method of production but as a testament to the ingenuity of conventional manufacturing practices.
Post time:12月 . 25, 2024 19:05
Next:Innovative Approaches to Sand Casting Techniques for Enhanced Metal Casting Projects