Sand 3D Printing Revolutionizing Manufacturing and Design
In recent years, 3D printing technology has transformed various industries, offering new methods for design and manufacturing. Among the various materials and techniques available, sand 3D printing has emerged as a particularly innovative and versatile approach. This process not only broadens the horizons of production capabilities but also introduces sustainable practices in manufacturing.
The Process of Sand 3D Printing
Sand 3D printing primarily involves the use of silica sand as the main material. The technology utilizes a method known as binder jetting, where a computer-controlled printer deposits a liquid binding agent onto layers of sand. Each layer is precisely printed to form a three-dimensional object. Once the desired structure is completed, the unbound sand is removed, leaving behind a sturdy, detailed mold or casting.
This method opens up possibilities for creating complex designs that are often too intricate or costly to achieve through traditional manufacturing techniques. For instance, intricate geometries such as lattice structures and organic shapes that were once relegated to digital renderings can now be produced efficiently.
Advantages of Sand 3D Printing
One of the most significant advantages of sand 3D printing is its efficiency in producing custom molds for casting. Traditional mold-making processes can be time-consuming and expensive, often requiring significant labor and materials. In contrast, sand 3D printing reduces lead times significantly, allowing manufacturers to produce customized molds with minimal effort. This feature is particularly beneficial for industries such as aerospace and automotive, where customized components are often needed for prototypes or limited-run products.
Additionally, sand-based materials are environmentally friendly. The process reduces waste typically associated with traditional manufacturing methods. Since the sand used in printing is reusable, manufacturers can recycle leftover sand from previous projects, minimizing the environmental footprint. Furthermore, the binders utilized in the printing process are often non-toxic, promoting safer working conditions.
sand 3d printing
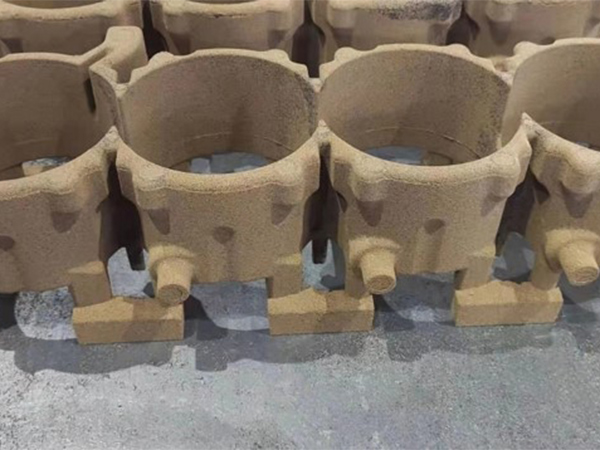
Applications in Various Industries
The applications of sand 3D printing are vast and varied. In the construction industry, it's being explored for its potential to create intricate architectural elements and even entire structures. The ability to produce complex molds and components onsite can significantly reduce costs and time associated with transporting materials.
In the field of art and design, artists and designers are increasingly leveraging sand 3D printing to create unique and customized pieces that challenge the boundaries of traditional artwork. The intricate details that can be achieved with this technology allow for a new level of creativity and innovation.
Moreover, sand 3D printing is revolutionizing the manufacturing of metal parts. By creating sand molds for metal casting, manufacturers can achieve high-quality, intricate components that were previously difficult or impossible to produce. This combination of 3D printing with metallurgy holds immense potential for industries where precision and complexity are crucial.
Challenges and Future Prospects
Despite its advantages, sand 3D printing is not without challenges. Ensuring the quality and consistency of printed products can be difficult, especially when scaling production. Additionally, the initial setup costs for sand 3D printing systems can be high, which may deter some manufacturers from investing in this technology.
However, as advancements continue and the technology becomes more accessible, it is likely that sand 3D printing will play an increasingly integral role in modern manufacturing. The potential for innovation is vast, and the ongoing research into new materials and methods promises to broaden its applications further.
In conclusion, sand 3D printing stands at the forefront of manufacturing technology, offering efficient, sustainable, and creative solutions across various industries. As we move forward, this process will not only change how products are designed and manufactured but will also pave the way for a more sustainable and innovative future in the world of production design. The exploration of this technology is just beginning, and its impact will resonate for years to come.
Post time:12月 . 03, 2024 18:18
Next:foundry sand reuse