Sand Casting of Cast Iron A Timeless Manufacturing Technique
Sand casting, one of the oldest and most versatile manufacturing processes, continues to play a significant role in the production of cast iron products. With its simplicity and cost-effectiveness, this method has remained a cornerstone of metalworking for centuries. Whether it’s for creating intricate designs or large structural components, sand casting provides a reliable means of transforming molten metal into solid forms.
The Sand Casting Process
The sand casting process begins with the creation of a pattern, which is essentially a replica of the final product. Patterns can be made from various materials, including wood, metal, or plastic, and are designed to be slightly larger than the final piece to account for shrinkage during cooling. Once the pattern is ready, a mold is created by packing sand around it. The sand is typically mixed with a binder to enhance its cohesiveness.
After the mold is formed, it is split into two halves for the removal of the pattern, creating a hollow cavity that mirrors the desired shape. The two halves of the mold are then reassembled and held together, after which molten cast iron is poured into the cavity. As the molten metal fills the mold, it takes on the shape of the pattern. This process is repeated for larger production runs, and the efficiency can be further enhanced with automated systems.
Advantages of Sand Casting for Cast Iron
One of the primary advantages of sand casting is its adaptability. It can be used to produce both small-scale components and massive industrial parts, such as engine blocks or machinery frames. The process is also suitable for a wide range of iron alloys, which allows manufacturers to tailor the composition of the cast iron to achieve specific mechanical properties.
sand casting cast iron
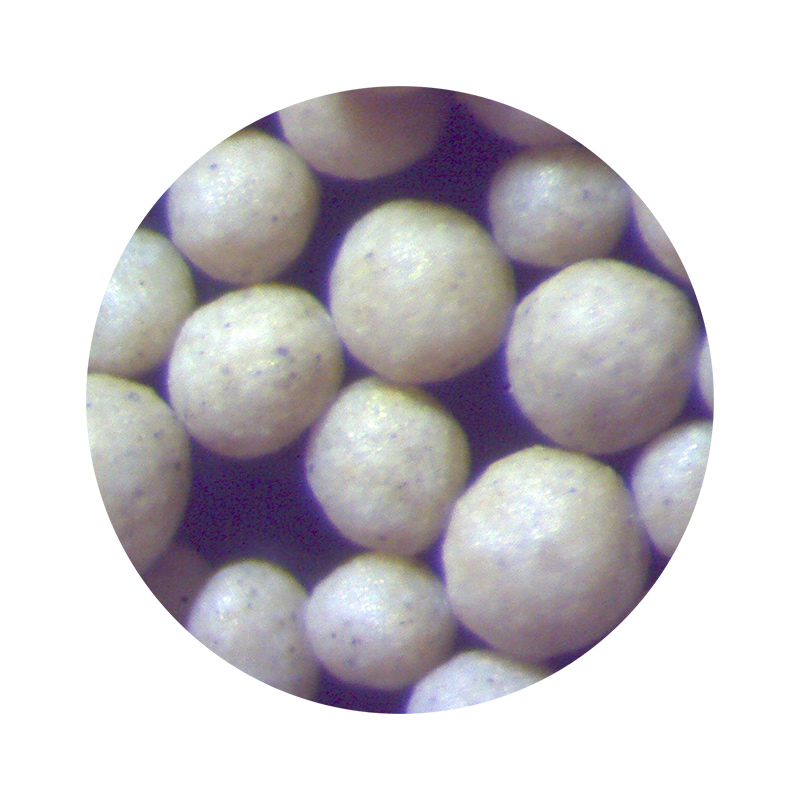
Additionally, sand casting is less expensive compared to other casting methods. The materials used for molds are relatively inexpensive, and the process can be conducted with minimal setup costs. This makes it a preferred choice for low to medium production volumes and applications where precision is not the highest priority.
Another significant benefit is the ability to create complex geometries. The porous nature of sand molds allows for excellent detail replication, and because the molds can be easily modified, design changes can be implemented without substantial costs. This is particularly advantageous for prototype development or custom parts.
Challenges and Considerations
Despite its advantages, sand casting is not without challenges. Surface finish and dimensional accuracy may not match that of other casting techniques, such as investment casting. As a result, additional machining or finishing operations may be required, which can add to the overall production time and cost.
Moreover, the brittleness of cast iron can also result in issues during the casting process or with the final product, particularly if the iron is highly alloyed or not properly handled. Therefore, careful control of the melting and pouring process is necessary to mitigate defects such as cold shuts or porosity.
Conclusion
In summary, sand casting remains a vital method for producing cast iron components across various industries. Its combination of low cost, flexibility, and the ability to create complex shapes makes it an enduring choice for both traditional and modern applications. As technology evolves, the sand casting process continues to be refined, ensuring its relevance in the ever-changing landscape of manufacturing. Whether for automotive parts, industrial machinery, or artistic applications, the impact of sand casting on the cast iron market is undeniable, cementing its place as a foundational technique within the metalworking field.
Post time:8月 . 29, 2024 16:58
Next:3D Printing Sanding