Lost Foam Castings A Revolutionary Manufacturing Process
Lost foam casting is a unique and innovative process in the field of metalworking that offers a number of advantages over traditional casting methods. This technique, which was developed in the mid-20th century, allows for the production of complex shapes with high precision while significantly reducing the amount of material waste. As industries continuously seek ways to enhance their manufacturing processes, lost foam casting stands out as a viable option that merges efficiency with flexibility.
At the heart of lost foam casting is the use of foam patterns made from polystyrene. These patterns are created using a process called foam fabrication, in which blocks of polystyrene are cut or molded into the desired shape. Once the foam pattern is prepared, it is coated with a special refractory material to provide strength and ensure that it can withstand the molten metal. This coating protects the foam during the pouring process, allowing the foam to remain intact until the metal is introduced.
Lost Foam Castings A Revolutionary Manufacturing Process
One of the main advantages of lost foam casting is its ability to produce intricate designs that would be difficult, if not impossible, to achieve with traditional casting methods. This capability is particularly valuable in industries that demand high precision, such as automotive, aerospace, and machinery manufacturing. The process also allows for the integration of complex features and geometries, such as internal passages and cooling channels, without the need for additional machining.
lost foam castings
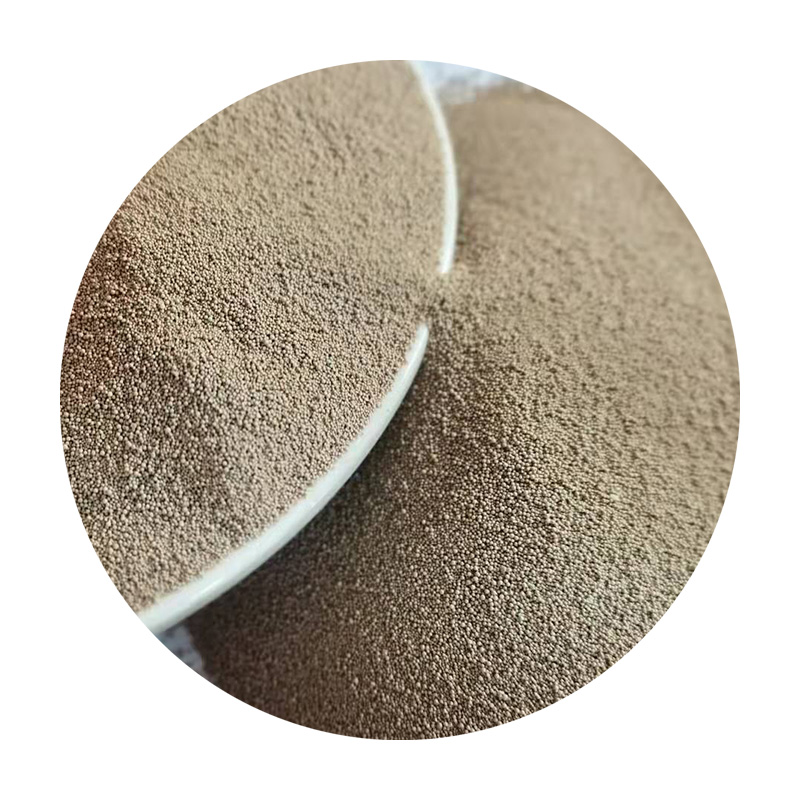
Furthermore, lost foam casting is an environmentally friendly option compared to other casting methods. The production of foam patterns generates significantly less waste material, which helps to reduce the overall environmental impact of the manufacturing process. In addition, the process generally uses less energy, as the heat required to melt metals can be more efficiently applied due to the rapid vaporization of the foam.
In terms of economic advantages, lost foam casting often translates into reduced production costs. The ability to create near-net-shape components minimizes the need for additional machining and finishing processes, leading to lower labor and material expenses. This efficiency can give companies a competitive edge in fast-paced industries where cost and time-saving measures are paramount.
However, despite its numerous advantages, lost foam casting is not without its challenges. One of the most significant hurdles is the need for precise control over various parameters during the casting process, including temperature, timing, and the properties of the foam patterns. Any deviations can lead to defects in the final product, such as uneven surfaces or dimensional inaccuracies. As a result, companies may need to invest in thorough training for their workforce and possibly sophisticated equipment to ensure consistent quality.
Moreover, while the materials used in lost foam casting are becoming more widely available, there may still be limitations on the types of metals that can be effectively cast using this method. Certain alloys may not respond well to the rapid vaporization and can lead to issues such as gas entrapment or incomplete filling of the mold.
In conclusion, lost foam casting is a revolutionary manufacturing process that combines precision, efficiency, and environmental sustainability. Its ability to produce complex shapes with minimal waste positions it as an attractive option for many industries facing the challenges of modern manufacturing. As advancements continue to be made in materials and technology, the potential for lost foam casting only looks to expand, paving the way for innovative applications and even greater efficiencies in the years to come. By embracing this method, manufacturers can not only enhance their capabilities but also contribute to a more sustainable future in production.
Post time:11月 . 08, 2024 14:21
Next:A Guide to Sanding Your 3D Printed Models for a Smooth Finish