Lost Foam Casting Revolutionizing the Foundry Industry
Lost foam casting (LFC) represents a significant advancement in metal casting techniques, providing an innovative solution for the fabrication of complex and high-precision components across various industries. This method, which dates back to the late 20th century, has garnered attention for its ability to produce castings with exceptional surface finishes and intricate geometries, effectively addressing the limitations of traditional sand casting processes.
At the core of lost foam casting lies the use of expandable polystyrene (EPS) foam patterns. These patterns are intricately shaped to match the desired final product, and they are coated with a fine layer of refractory material, usually a mix of sand and bonding agents. Once the coating has dried, the foam pattern is prepared for the casting process. The innovative aspect of LFC emerges when the molten metal is introduced into the mold. As the metal fills the cavity, the foam pattern vaporizes, leaving behind a hollow space that takes on the shape of the original pattern. This eliminates the need for traditional molds, which can be time-consuming and expensive to produce.
Lost Foam Casting Revolutionizing the Foundry Industry
Another noteworthy benefit of LFC is its efficiency in material usage. Traditional casting methods often result in significant waste due to the need for excess material to accommodate the mold and gating systems. In contrast, lost foam casting reduces waste substantially, as the foam is fully consumed during the process. This not only contributes to a more sustainable production practice but also lowers the overall cost of materials.
lost foam casting foundry
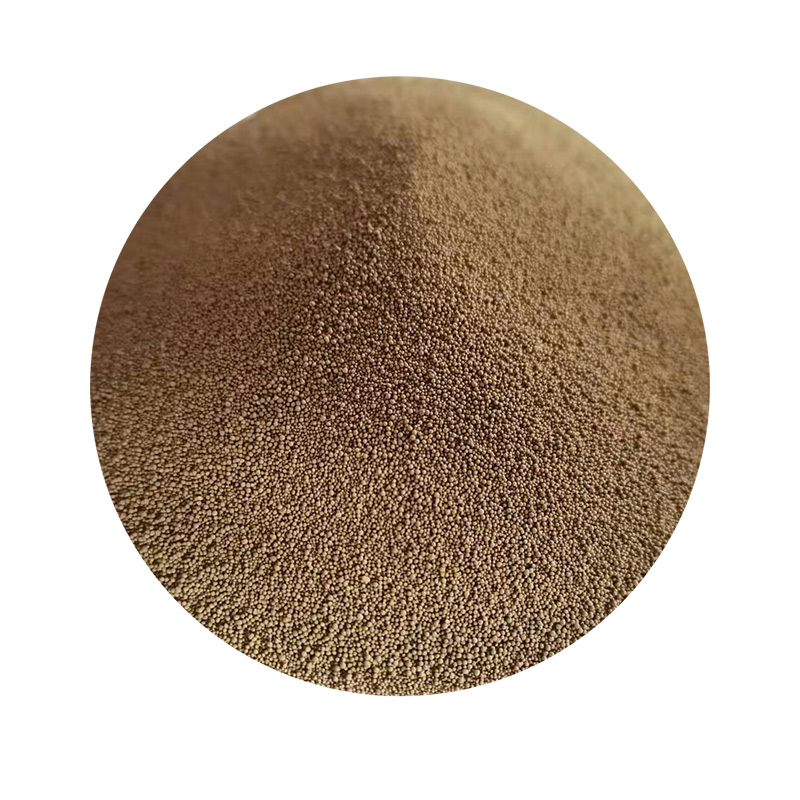
The versatility of lost foam casting makes it suitable for a wide range of applications, from automotive components to industrial machinery parts. Industries that demand high strength-to-weight ratios often find LFC particularly beneficial. Components such as engine blocks, transmission housings, and various structural elements can be manufactured with the precision and quality required for high-performance applications. Furthermore, the process can accommodate a variety of metals, including aluminum, iron, and copper alloys, making it adaptable for different manufacturing needs.
As technology continues to evolve, the integration of advanced techniques such as computer-aided design (CAD) and computer numerical control (CNC) machining with lost foam casting has further enhanced its capabilities. Modern foundries are increasingly adopting these innovations to optimize production efficiency and quality control. The use of simulation software allows for better prediction of how metals will flow and solidify within foam molds, leading to fewer defects and higher-quality outputs.
Despite its numerous advantages, lost foam casting does come with certain challenges. The initial setup costs can be higher than traditional methods due to the need for specialized equipment and materials. Additionally, the process requires careful control of temperature and pouring rates to ensure that the foam pattern burns off correctly, and any miscalculation could lead to defects in the final casting.
In conclusion, lost foam casting stands out as a transformative technique within the foundry industry, combining innovation with efficiency. Its ability to produce complex shapes with high precision and a superior surface finish makes it an attractive alternative to traditional casting methods. As industries continue to seek more effective manufacturing solutions, lost foam casting is poised to play a crucial role in shaping the future of metal casting, driving advancements that meet the increasing demands for quality and efficiency in manufacturing. As technology progresses, we can expect further refinements in this technique, likely expanding its applications and enhancing its capabilities even further.
Post time:11月 . 28, 2024 00:01
Next:Is Sand Casting an Expensive Manufacturing Process Compared to Alternatives?