Foundry Sand Density An Essential Parameter in Metal Casting
Foundry sand plays a pivotal role in the metal casting process, particularly in the production of intricate shapes and components. This sand, primarily composed of silica, is a fundamental ingredient in creating molds that hold molten metal during various metalworking applications. One critical characteristic of foundry sand that significantly affects its performance is density. This article delves into the importance of foundry sand density, its measurement, and its implications for casting quality.
Understanding Foundry Sand Density
Density, defined as mass per unit volume, is a vital metric when evaluating foundry sand. The density of foundry sand can influence several physical properties, including permeability, strength, and thermal conductivity. A higher density typically indicates that the sand is less porous, which can enhance mold strength but may reduce airflow, potentially leading to defects during the casting process.
The density of foundry sand is affected by various factors, including grain size, shape, and distribution, as well as the moisture content and additives used in the mixture. This interplay of factors means that achieving the optimal density is critical for ensuring the effectiveness of the casting process.
Importance of Measuring Density
Regular measurement of foundry sand density is crucial for foundries aiming to maintain consistency and quality in their products. Variations in density can lead to significant defects in the final castings, such as misruns or insufficient fill. Moreover, inconsistent sand density can affect how molten metal interacts with the mold, leading to issues such as sand contamination or poor surface finishes.
foundry sand density
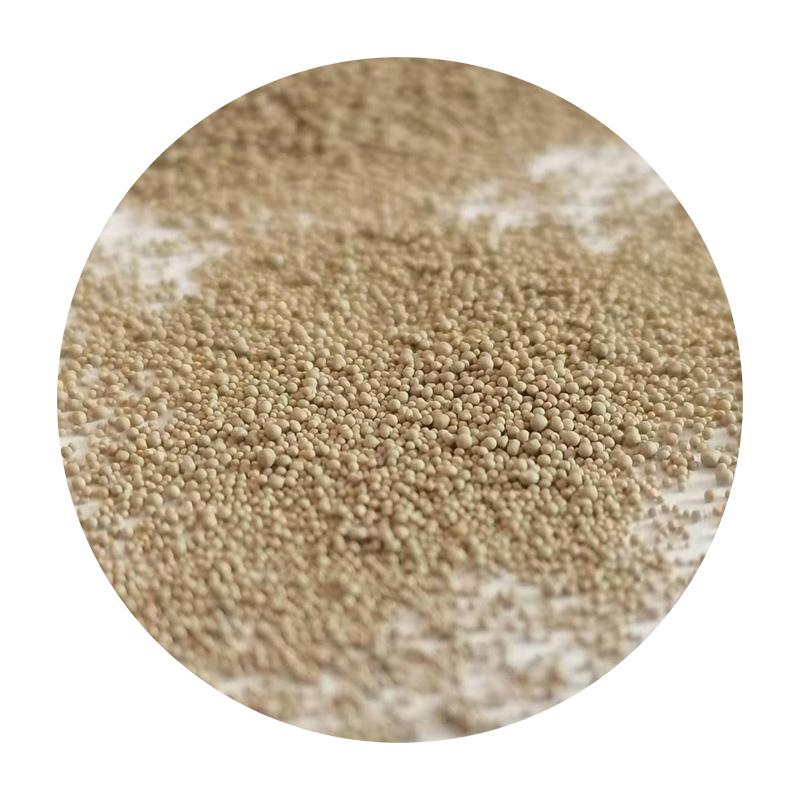
Foundries often utilize specialized equipment to measure sand density accurately. Techniques such as using a density cup or performing water displacement methods help determine the precise density of the sand mix. By employing these techniques, foundry operators can make informed decisions regarding sand selection and adjustments necessary for achieving the desired mold properties.
Implications for Casting Quality
The impact of foundry sand density on casting quality cannot be overstated. A mold with optimal sand density provides better thermal insulation, which is crucial for controlling the cooling rate of the molten metal. This control impacts the final microstructure of the casting, ultimately enhancing the mechanical properties of the finished product.
Additionally, the right sand density aids in preventing common casting defects, such as gas porosity and shrinkage cavities. For example, if the sand is too dense, it may hinder the escape of gases generated during casting, leading to defects. Conversely, if the sand is too light, it might not be able to withstand the pressure of the molten metal, compromising the integrity of the mold.
Conclusion
In summary, the density of foundry sand is a critical parameter that profoundly influences the metal casting process. Understanding and controlling this property can lead to enhanced casting quality, reduced defects, and improved overall performance in foundries. As the industry continues to evolve, embracing advanced methods for measuring and optimizing foundry sand density will be crucial for manufacturers aiming to produce high-quality metal components efficiently and consistently. By prioritizing sand density in their processes, foundries can better meet the demanding standards of modern manufacturing.
Post time:11月 . 07, 2024 08:46
Next:Tailored Sand Casting Solutions for Unique Metal Component Manufacturing