Understanding Sand Casting A Comprehensive Overview
Sand casting, often referred to as sand mold casting, is one of the oldest and most widely used metal casting processes in manufacturing. Its simplicity, versatility, and cost-effectiveness have made it popular across various industries, including automotive, aerospace, and art. In this article, we will delve into the intricacies of sand casting, its processes, materials, applications, and advantages, providing a comprehensive view of this fundamental manufacturing method.
The Sand Casting Process
The sand casting process involves several key steps. The first stage is pattern making, where a replica of the final product, known as a pattern, is created from materials such as wood, metal, or plastic. The pattern is essential as it forms the cavity in the sand where the molten metal will be poured.
Next, the pattern is placed in a mixture of sand and binder, which is then compacted into a mold. The most common type of sand used is silica sand due to its temperature resistance and availability. The mold typically consists of two halves the cope (the top half) and the drag (the bottom half). Once the mold is assembled and compacted, the pattern is removed, leaving behind a cavity that mirrors the shape of the desired casting.
After the mold is prepared, it's time for the pouring phase. Molten metal, heated to a temperature that exceeds its melting point, is poured into the mold cavity. The metal fills every part of the mold, conforming to its shape. After the metal has cooled and solidified, the mold is broken apart to reveal the casting inside. Finally, the casting undergoes various finishing processes to remove excess material, improve surface quality, and achieve desired specifications.
Materials Used in Sand Casting
The two primary materials involved in sand casting are the sand used for mold-making and the metal to be cast. Silica sand is the most common choice due to its durable and heat-resistant properties. Additives may be included in the sand mix to enhance its binding capabilities, with clay being a prevalent binder.
As for the metal, a broad range of alloys can be used in sand casting, including iron, aluminum, bronze, magnesium, and zinc. The choice of metal largely depends on the desired properties of the final casting, such as strength, weight, and corrosion resistance.
describe sand casting
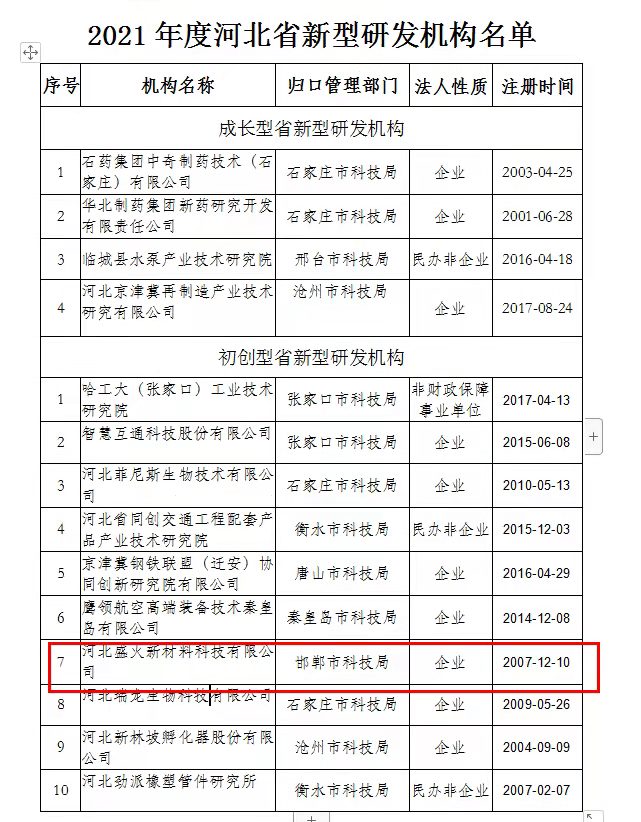
Applications of Sand Casting
Sand casting is utilized in various industries, proving its adaptability and effectiveness. In the automotive industry, sand casting is often used to produce engine blocks, transmission cases, and other complex components. The aerospace sector benefits from sand casting to create parts like turbine housings and brackets, where lightweight and high-strength materials are imperative.
Moreover, sand casting is also employed in artistic creations, allowing artists to replicate detailed sculptures and designs. The method's flexibility to produce both large and small components makes it a favored choice for custom parts and prototypes.
Advantages of Sand Casting
Several advantages contribute to the ongoing popularity of sand casting. Firstly, it is capable of producing intricate and complex shapes that would be challenging with other manufacturing methods. The sand mold can be easily modified to accommodate different designs without incurring significant costs.
Secondly, sand casting can handle a variety of metals and alloys, making it suitable for diverse applications. The process also allows for the production of large components, which is often more difficult with other casting methods.
Additionally, the setup for sand casting can be relatively low-cost compared to more advanced techniques like die casting or investment casting. This socioeconomic benefit makes it an appealing option for small businesses and artisans.
Conclusion
Sand casting remains a foundational process in manufacturing and engineering, transcending time due to its effectiveness and versatility. By understanding its processes, materials, applications, and advantages, manufacturers can leverage sand casting to meet their production needs, bringing innovative designs and solutions to life. Whether producing intricate art pieces or essential automotive components, sand casting continues to be an invaluable part of the manufacturing landscape.
Post time:11月 . 30, 2024 05:08
Next:Leading Manufacturer of High-Quality Sand Castings for Various Industries and Applications