Understanding Sand Casting An Overview
Sand casting, also known as sand mold casting, is one of the most widely used manufacturing processes in the world, valued for its simplicity and versatility. The technique involves creating a sand mold into which molten metal is poured to produce a solid object. This method has been utilized for centuries, from ancient civilizations to modern industrial applications, making it a cornerstone in metalworking and production.
The Process of Sand Casting
The sand casting process begins with creating a mold. This involves two primary components the pattern and the mold itself. The pattern, typically made of metal, plastic, or wood, is a replica of the final product, designed slightly larger to account for the contraction of the metal as it cools. The mold is formed by compacting sand around the pattern, typically using a mixture of silica sand, clay, and water. This mixture provides the necessary cohesiveness and stability during the pouring process.
Once the mold is prepared, it is separated, and the pattern is carefully removed, leaving an impression in the sand. The two halves of the mold are then reassembled, and a pouring cup is attached to facilitate the flow of molten metal into the cavity. At this stage, the metal is heated until it reaches a liquid state, often using a furnace. Common metals used in sand casting include aluminum, iron, and zinc, chosen for their favorable casting properties.
After the metal is poured into the mold, it undergoes a cooling phase. The cooling rate depends on various factors, including the type of metal and the thickness of the cast. Once the metal solidifies, the mold is broken apart, and the newly formed casting is removed. The process does not end here, as several finishing operations may be necessary to achieve the desired surface condition and dimensional accuracy. These operations can include grinding, sanding, machining, and applying protective coatings.
Advantages of Sand Casting
describe sand casting
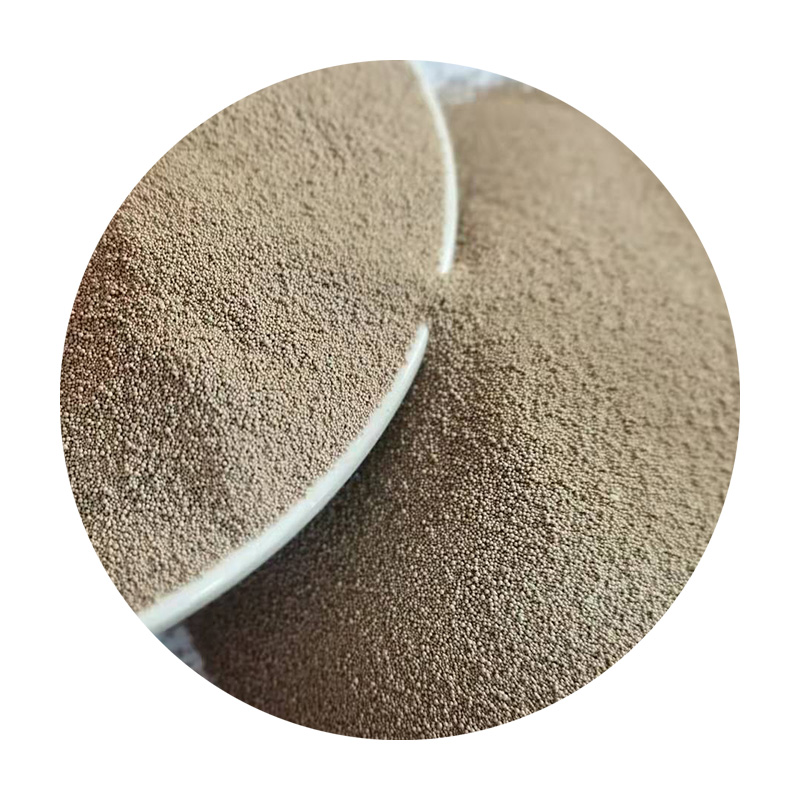
One of the primary advantages of sand casting is its cost-effectiveness, especially for producing large components. The materials used for the mold are relatively inexpensive, and the process allows for the production of both small and large quantities of parts. Additionally, complex shapes and designs can be achieved, which might be challenging with other casting methods.
Another significant benefit is the capability to cast a variety of metals, making sand casting suitable for a wide range of industries, including automotive, aerospace, and sculpture. Its adaptability allows manufacturers to utilize different types of sand and binder mixtures to meet specific requirements for strength, thermal stability, and finish quality.
Applications of Sand Casting
Sand casting is employed in various industries for diverse applications. In the automotive sector, it is used to produce engine blocks, cylinder heads, and transmission cases. The aerospace industry also benefits from sand casting in creating lightweight yet strong components for aircraft. Moreover, sand casting is pivotal in artistic endeavors, allowing sculptors to create intricate metal sculptures and decorative items.
Conclusion
Sand casting remains an essential technique in the manufacturing landscape, combining tradition and modernity. Its flexibility, economic advantages, and ability to produce complex shapes make it a preferred choice for many industries. Whether creating everyday items or high-precision components, sand casting provides a reliable and efficient solution that continues to evolve with technological advancements. As industries demand more innovative and sustainable methods of production, sand casting will likely adapt and remain relevant in the years to come.
Post time:11月 . 14, 2024 23:43
Next:advantages and disadvantages of sand casting process