The Density of Foundry Sand A Critical Parameter in Metal Casting
Foundry sand, an essential material in the metal casting industry, plays a crucial role in the manufacturing of metal components. Understanding the properties of foundry sand, particularly its density, is vital for ensuring the quality and precision of castings. This article delves into the significance of foundry sand density, its influencing factors, and its implications in the casting process.
What is Foundry Sand?
Foundry sand is a high-quality silica sand that is specifically used in metal casting processes to create molds and cores. It is characterized by its ability to withstand high temperatures and forms a durable mold when mixed with a binding agent. The primary function of foundry sand is to provide a solid shape for molten metal to be poured into, and subsequently harden to form the final metal product.
Importance of Density in Foundry Sand
Density is a critical property of foundry sand that affects various aspects of the metal casting process. It can be defined as the mass of the sand per unit volume, typically expressed in grams per cubic centimeter (g/cm³) or pounds per cubic foot (lb/ft³). The density of foundry sand influences
1. Mold Strength Higher density sands often yield stronger molds that can withstand the pressure exerted by molten metal. This strength is essential in preventing deformations or collapses during the casting process.
2. Thermal Conductivity The thermal properties of foundry sand, including its density, affect its ability to absorb and dissipate heat. A sand with appropriate density can better manage the heat generated during casting, thereby influencing the cooling rate of the molten metal.
3. Gas Permeability Foundry sand density impacts gas permeability, which is essential for allowing gases generated during casting to escape without causing defects. An ideal balance in density is required to ensure that the molds permit gas escape while maintaining structural integrity.
4. Surface Finish The density of the sand can affect the surface finish of the cast product. Finer and denser sands often result in smoother surfaces, reducing the need for additional finishing processes.
density of foundry sand
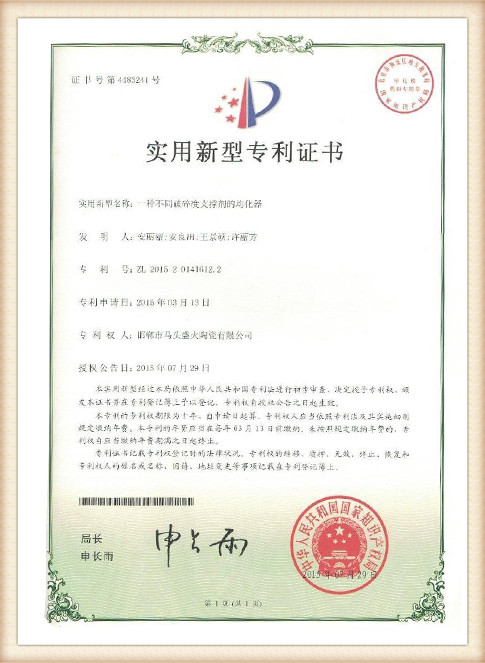
Factors Affecting Density
Several factors determine the density of foundry sand, including
1. Grain Size The size of the sand grains significantly impacts the overall density. Finer sands tend to fill spaces between larger particles, increasing overall density.
2. Moisture Content The presence of moisture can add weight to the sand, thus altering its density. Excess moisture can lead to molding issues, while insufficient moisture might fail to achieve the desired packing characteristics.
3. Additives Various additives are sometimes mixed with foundry sand, such as clay or resin, which can change both the density and the thermal properties of the material.
4. Compaction The method by which the sand is compacted during the molding process will affect its density. Higher compaction generally results in increased density, leading to stronger molds.
Measuring Density
Determining the density of foundry sand is crucial for optimizing the casting process. It is typically measured using standardized methods, such as the gravimetric and pycnometric techniques. Regular density assessments help foundries maintain consistency in their materials and ensure that the quality of their cast products meets industry standards.
Conclusion
In the world of metal casting, the density of foundry sand is far more than just a numerical value; it is a pivotal parameter that influences various aspects of the casting process. By understanding and controlling the density of foundry sand, foundries can enhance mold strength, improve thermal management, facilitate gas escape, and ultimately produce higher-quality cast products. As the industry continues to evolve, ongoing research into the properties of foundry sand will undoubtedly lead to innovations that further refine the casting process, ensuring that density remains a key focal point in metal manufacturing.
Post time:10月 . 19, 2024 06:23
Next:Innovative Techniques in Additive Manufacturing for Sand Casting Patterns in 3D Printing