Components of Sand Casting
Sand casting is a fundamental manufacturing process used for creating complex metal parts. This technique has been around for centuries and remains popular due to its adaptability and cost-effectiveness. Understanding the components that make up the sand casting process is crucial for anyone interested in metalworking, engineering, or manufacturing. This article outlines the key components involved in sand casting, providing insight into how this versatile method operates.
1. Pattern
At the heart of the sand casting process is the pattern. The pattern is a replica of the final product and is typically made from materials such as metal, wood, or plastic. Patterns can be designed in different ways, depending on the complexity of the part. There are two primary types of patterns solid patterns, which replicate the entire shape of the item, and split patterns, which consist of two halves that can be separated. The material chosen for the pattern, as well as its finish, plays a crucial role in the quality of the final casting.
2. Mold
The mold is formed around the pattern and serves as the cavity where molten metal is poured. In sand casting, the mold is made from a mixture of sand, clay, and water. The sand provides strength and permeability, while the clay acts as a binder to hold the particles together. The quality of the mold directly affects the integrity of the final product. The sand must be properly prepared and compacted to ensure that it can withstand the heat of molten metal and maintain its shape during the pouring process.
3. Core
In cases where the finished part requires internal cavities or complex geometries, a core is used. Cores are typically made from sand and are positioned within the mold to create holes or channels in the completed casting. Cores can be removable, allowing for easy extraction following the casting process, or they can be integral to the mold, depending on the design. Ensuring that the core is properly placed and securely supported in the mold is vital for the accuracy of the final part.
components of sand casting
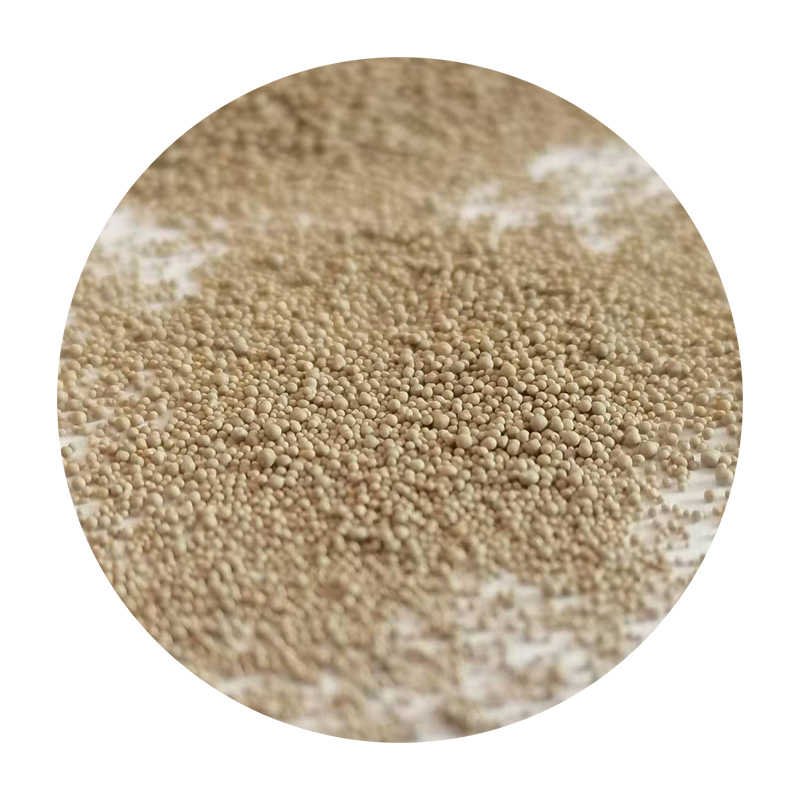
4. Molten Metal
The molten metal is the substance that fills the mold and solidifies to create the desired component. Common metals used in sand casting include aluminum, brass, bronze, and iron. The selection of the metal depends on the mechanical properties required in the final product, as well as cost considerations. Once the metal is melted, it is carefully poured into the mold, filling all cavities and taking the shape of the pattern. Temperature control is critical during this stage to prevent defects such as porosity or incomplete filling.
After the molten metal is poured into the mold, it begins to cool and solidify. This phase is essential, as the cooling rate can significantly influence the properties of the final casting. Slow cooling may lead to a finer grain structure, while rapid cooling can introduce brittleness. Monitoring cooling times and ensuring that the molten metal remains in the mold for the appropriate duration is essential for achieving the desired material properties.
6. Cleaning and Finishing
Once the metal has solidified, the mold is broken away to reveal the casting. This marks the beginning of the cleaning process, which typically involves sand removal, grinding, and polishing to achieve the desired surface finish. Additional treatment processes, such as heat treatment or surface coatings, may also be employed to enhance performance characteristics.
Conclusion
Sand casting is a well-established manufacturing process that encompasses various components, each contributing to the successful creation of metal parts. From the pattern and mold to the molten metal and finishing processes, understanding these components allows for better control over the trial and error inherent in production. As industries continue to seek efficient and effective methods of manufacturing, sand casting remains a reliable choice due to its versatility and ability to produce intricate designs. Whether for small-scale applications or large industrial components, the principles of sand casting continue to play a vital role in modern manufacturing.
Post time:11月 . 30, 2024 07:59
Next:super sand bond g2