The Advantages of Cast Iron Sand Casting
Cast iron sand casting is a widely utilized manufacturing process that combines the advantages of cast iron's durability with the versatility of sand molds. This technique is prevalent in various industries, including automotive, construction, and machinery, due to its ability to produce complex shapes and large components efficiently.
Process Overview
The sand casting process begins with the creation of a sand mold. Fine sand is mixed with a binding agent, such as clay, and water to form a pliable mixture. This sand is then compacted around a pattern, which is a replica of the part to be cast. Once the sand is shaped and hardened, the pattern is removed, leaving a cavity in the mold. The next step involves pouring molten cast iron into this cavity. The iron, heated to its melting point, fills the mold, taking the shape of the desired component. After the casting cools and solidifies, the sand mold is broken away to reveal the finished product.
Material Benefits
Cast iron, known for its excellent casting properties, is composed primarily of iron, carbon, and silicon. Its high fluidity allows it to fill intricate mold designs, making it ideal for complex shapes. Once cooled, cast iron demonstrates exceptional wear resistance, mechanical strength, and thermal stability. These properties make it an excellent choice for heavy-duty applications, such as engine blocks, pipes, and machine components.
cast iron sand casting
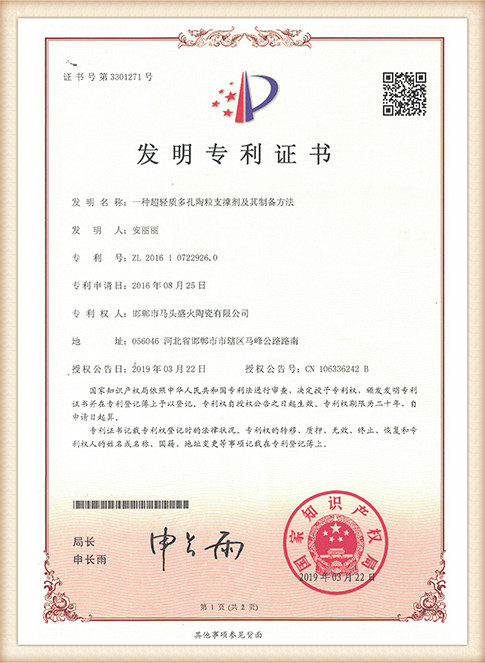
Environmental Aspects
The sand casting process is also environmentally friendly. One significant benefit is the recyclability of sand. After completing a casting, the sand can be cleaned and reused for future molds, significantly reducing waste. Furthermore, advances in technology have led to the development of more sustainable practices in the foundry industry, such as using low-emission furnaces and minimizing energy consumption.
Applications and Innovations
The versatility of cast iron sand casting has led to its widespread application across various sectors. Industries use this method to manufacture engine components, heavy machinery parts, and decorative architectural elements. Innovations are continuing to enhance the efficiency and quality of cast iron products, including the use of computer-aided design (CAD) for improved mold accuracy and the implementation of 3D printing to create complex patterns.
Conclusion
In conclusion, cast iron sand casting remains a formidable technique in modern manufacturing, combining the durability of cast iron with the adaptability of sand molds. Its environmental benefits and ability to produce intricate designs make it an essential process across many industries. As technology continues to advance, cast iron sand casting is poised for continued growth and innovation, shaping the future of manufacturing.
Post time:9月 . 10, 2024 16:36
Next:How to Sand Resin for a Smooth Finish