Understanding the Benefits of Sand Casting in Manufacturing
Sand casting is one of the oldest and most versatile manufacturing processes still in use today. This technique has been a staple in various industries for producing metal parts due to its simplicity and cost-effectiveness. In this article, we will explore the advantages of sand casting and discuss why it remains a popular choice for many manufacturers around the world.
Sand casting involves creating a mold from a mixture of sand, clay, and water. The pattern, or model of the part to be produced, is pressed into the sand to create a cavity, into which molten metal is poured. After the metal cools and solidifies, the sand mold is broken away to reveal the finished product. The cycle is then repeated for mass production.
Understanding the Benefits of Sand Casting in Manufacturing
Additionally, sand casting offers exceptional versatility. It can be employed to create parts of various sizes, from small components to large industrial pieces weighing several tons. This flexibility allows manufacturers to explore a wide range of applications, including automotive, aerospace, and construction industries. Furthermore, sand casting can accommodate nearly any metal, including iron, aluminum, bronze, and various alloys, making it suitable for diverse projects.
buy sand casting
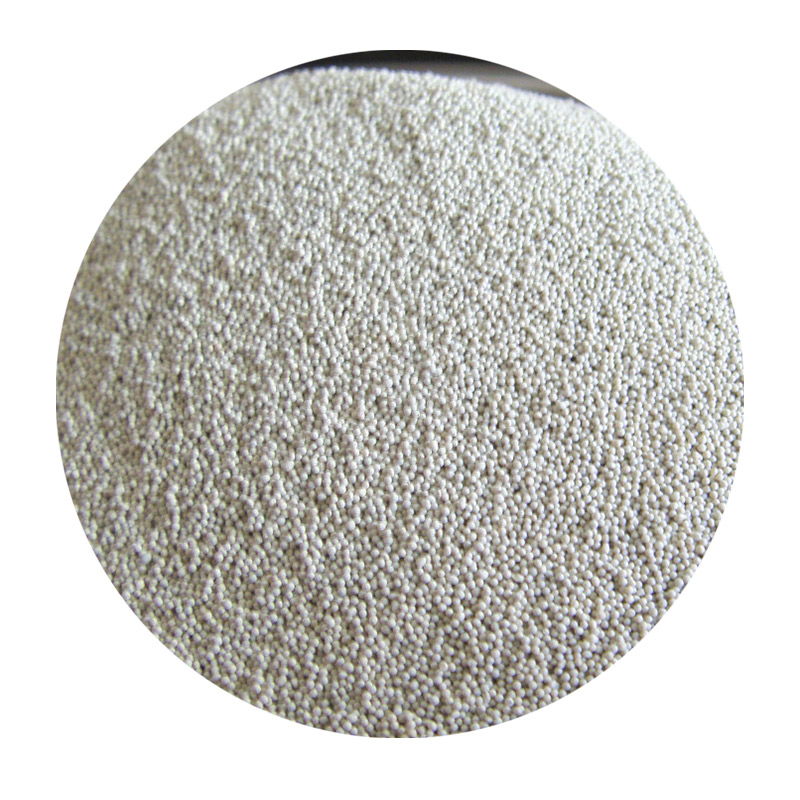
Another significant advantage of sand casting is its capability to produce complex geometries. The sand mold can be easily manipulated to create intricate designs that would be difficult or impossible to achieve with other casting methods. This ability to produce detailed prototypes quickly makes sand casting an ideal choice for many engineers and designers during the development phase of a project.
Moreover, the sand casting process allows for excellent surface finishes. While sand-cast parts may require additional finishing operations, the initial surface quality can be quite good, leading to reduced machining time and costs. Various techniques can be employed to improve finishing, ensuring that the final product meets the necessary specifications.
Environmental considerations also play a part in the attraction of sand casting. The primary material, sand, is abundant and can be recycled. After the casting process, the sand can be reused for new molds, reducing waste significantly. As manufacturers increasingly seek sustainable practices, this characteristic of sand casting aligns well with their goals.
Furthermore, the sand casting process is relatively straightforward. With a traditional setup, minimal training is required for operators, which reduces labor costs and speeds up production times. This accessibility allows smaller businesses to enter the market and compete with larger industries effectively.
In conclusion, the decision to buy or invest in sand casting services is backed by numerous benefits, including cost-effectiveness, versatility, capability for complex designs, good surface finishes, environmental sustainability, and ease of operation. As industries continue to evolve, embracing traditional techniques like sand casting proves vital for a wide range of manufacturing applications. Whether you are part of a large corporation or a small business, the advantages of sand casting can be harnessed to create high-quality, precise metal parts that meet the demands of today’s market. As the manufacturing landscape continues to change, sand casting remains a reliable and efficient choice for producing robust metal components.
Post time:11月 . 15, 2024 08:52
Next:sanding 3d prints