3D Printing for Sand Casting Revolutionizing Foundry Processes
3D printing technology has made significant strides across various industries, and its integration into the sand casting process marks a pivotal moment in the evolution of foundry practices. Sand casting, a traditional method of metal casting, involves creating a mold from sand in which molten metal is poured to form a desired shape. However, this method, while effective, has certain limitations such as long lead times, high material waste, and restrictions on design complexity. The advent of 3D printing offers solutions to these challenges, enhancing efficiency, precision, and innovation within the foundry sector.
3D Printing for Sand Casting Revolutionizing Foundry Processes
Furthermore, 3D printing allows for greater design flexibility. Complex geometries and intricate details that would be nearly impossible or prohibitively expensive to achieve with traditional casting methods can be produced effortlessly with 3D printing. This capability opens the door to innovative designs that not only enhance functionality but also reduce the overall weight of cast parts, contributing to more efficient end products. Additionally, the ability to produce lightweight, optimized structures can lead to significant material savings and lower production costs.
3d printing for sand casting
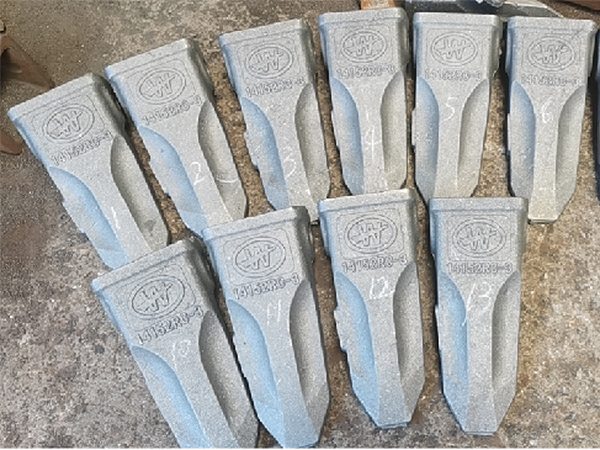
Another critical benefit of adopting 3D printing in sand casting is the reduction of material waste. Traditional sand molds often result in excess material that is discarded, whereas 3D printed molds can be produced with high precision, minimizing waste. Moreover, advancements in sustainable 3D printing materials and processes allow for more environmentally conscious options, aligning with the growing trend toward sustainability in manufacturing.
The integration of 3D printing technology into sand casting is not just about improving existing processes; it also fosters collaboration between engineers, designers, and manufacturers. By using digital design tools and simulation software, teams can better visualize and test their designs before committing to physical production. This collaborative approach enhances communication and ensures that end products meet the required specifications and performance standards.
In conclusion, the incorporation of 3D printing in sand casting presents numerous benefits that can significantly transform the foundry industry. With faster production times, increased design flexibility, reduced material waste, and improved collaboration, 3D printing is set to redefine traditional manufacturing practices. As this technology continues to evolve, it promises to unlock even more potential for innovation and efficiency, paving the way for a new era in metal casting. Embracing these changes will not only improve operational effectiveness but also place manufacturers ahead in a competitive landscape.
Post time:11月 . 02, 2024 09:38
Next:metal casting sand