The Future of Manufacturing 3D Printed Sand Casting
In recent years, the manufacturing landscape has been significantly transformed by the advent of additive manufacturing technologies. Among the various applications of 3D printing, one of the most groundbreaking has been the use of 3D printed sand casting. This innovative technique has revolutionized the casting process, offering numerous benefits that enhance efficiency, precision, and sustainability.
Traditionally, sand casting involves creating a mold from sand that is then filled with molten metal to create a desired part. This process is labor-intensive and requires a high degree of skill, as well as considerable time for mold preparation. However, the introduction of 3D printing has streamlined this process dramatically. With 3D printed sand molds, manufacturers can design and produce complex geometries that would be nearly impossible or cost-prohibitive using traditional methods.
The Future of Manufacturing 3D Printed Sand Casting
Moreover, the precision offered by 3D printing technology cannot be overstated. Traditional sand casting often comes with variations due to the manual nature of mold creation, leading to inconsistencies in the final product. In contrast, 3D printing allows for highly precise and repeatable molds, resulting in parts that are more accurate and reliable. This becomes especially crucial in industries such as automotive and aerospace, where component reliability is paramount for safety and performance.
3d printed sand casting
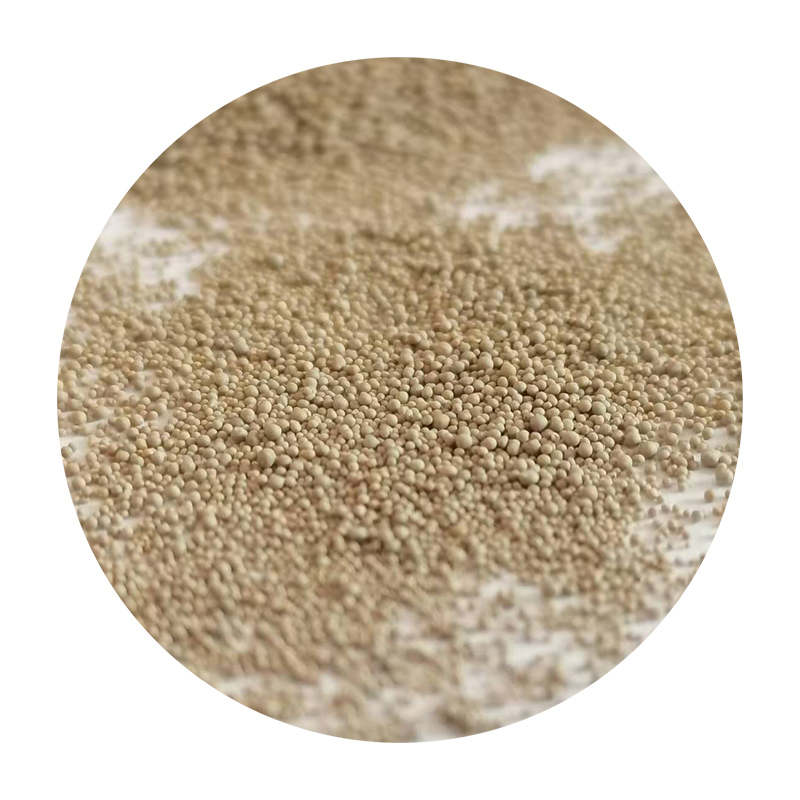
The design freedom afforded by 3D printing is another monumental advantage. Engineers and designers can create intricate designs that optimize performance without the constraints of conventional mold-making techniques. Features such as internal cooling channels, lattices, and complex geometries can be easily integrated into the mold design. This freedom not only enhances the performance of the final product but also can lead to materials and resource savings.
Sustainability is a critical consideration in modern manufacturing, and 3D printed sand casting offers promising avenues for reducing environmental impact. The traditional casting methods often result in significant material waste, as excess sand and material must be disposed of. However, 3D printing allows for the utilization of sand in a more efficient manner, minimizing waste. Additionally, it can accommodate recyclable materials and enable the creation of molds that use less energy during the curing process. The potential for reduced material waste and energy consumption positions 3D printed sand casting as a more sustainable option compared to conventional methods.
The applications of 3D printed sand casting span a wide range of industries. From prototyping to full-scale production, this technology is being leveraged to create everything from intricate automotive parts to artistic sculptures. Industries such as healthcare are also exploring 3D printed molds for creating customized prosthetics and implants, showcasing the technology's versatility.
Despite its advantages, 3D printed sand casting is still facing challenges that need addressing. The technology itself requires significant investment, and there may be a learning curve associated with integrating it into traditional manufacturing processes. Furthermore, the material properties of the printed molds must continue to be refined to ensure they can withstand the rigors of high-temperature metal casting without degradation.
In conclusion, 3D printed sand casting represents a significant leap forward in manufacturing technology. Its ability to reduce lead times, enhance precision, provide design freedom, and promote sustainability positions it as a key player in the future of manufacturing. As the technology continues to evolve and mature, it is likely to play an increasingly vital role in various industries, paving the way for innovative production methods that align with the demands of modern consumers and the ecological imperatives of our time.
Post time:12月 . 11, 2024 06:24
Next:Exploring the Applications and Benefits of Sand Casting in Modern Manufacturing