Understanding Sand Casting An Essential Manufacturing Process
Sand casting, also referred to as sand mold casting, is one of the oldest and most widely used metal casting processes in manufacturing. This technique involves creating a mold from a mixture of sand and a bonding agent, then pouring molten metal into the mold to produce a desired shape. Its simplicity, versatility, and cost-effectiveness have made it a staple in various industries, from automotive to aerospace.
The Sand Casting Process
The sand casting process encompasses several key steps, starting with the creation of a mold. The first step involves preparing the pattern, which is a replica of the object to be cast. The pattern is typically made from materials like wood, metal, or plastic. Once the pattern is ready, it is pressed into a mixture of sand and a bonding agent, usually clay or resin, to create a sand mold. The mold consists of two halves — the cope (top half) and the drag (bottom half) — which are assembled to form a complete cavity.
After the mold is created, the next step involves pouring molten metal into the cavity. The temperature of the molten metal varies depending on the specific alloy being used; for example, aluminum melts at a lower temperature compared to cast iron. Once the metal is poured, it is left to cool and solidify. After sufficient cooling time, the mold is broken apart to reveal the casting, which may require additional finishing processes such as grinding, machining, or surface treatment.
Advantages of Sand Casting
One of the primary advantages of sand casting is its cost-effectiveness. The materials used for the mold — primarily sand — are inexpensive and widely available. Additionally, this method allows for the production of large parts at a relatively low cost, making it an attractive option for small and large production runs alike.
Another significant advantage is the versatility of sand casting. It can accommodate a wide range of metals, including iron, aluminum, bronze, and magnesium, enabling manufacturers to tailor the casting process to specific requirements. Furthermore, sand casting is capable of producing complex geometries and large parts that would be difficult or impossible to achieve with other manufacturing methods such as die casting or injection molding.
Applications of Sand Casting
youtube sand casting
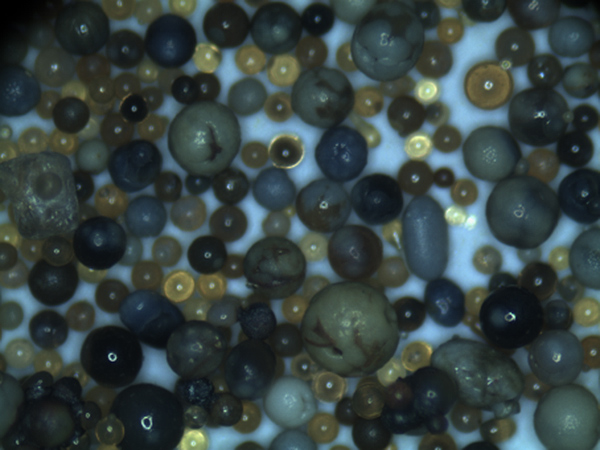
Sand casting finds applications across numerous industries. In the automotive sector, it is extensively used to manufacture engine blocks, cylinder heads, and transmission cases. The ability to create complex shapes and intricate features makes it particularly valuable in producing components that require high precision.
In the aerospace industry, sand casting is utilized to manufacture critical components that need to withstand extreme conditions. Parts such as turbine housings, structural components, and fittings often originate from sand casting processes due to the strength and durability of the materials used.
Moreover, the construction and heavy equipment industries benefit from sand casting in producing large and heavy components like machine frames, gears, and brackets. This versatility in application underscores the significance of sand casting in modern manufacturing.
Challenges and Future Outlook
Despite its numerous advantages, sand casting does face certain challenges. One of the main concerns is the potential for defects, such as holes, surface irregularities, or dimensional inaccuracies, which can arise from improper mold preparation or pouring techniques. To combat these issues, manufacturers are continually investing in new technologies such as 3D printing for mold creation, which can enhance precision and reduce lead time.
Looking ahead, the future of sand casting appears promising, driven by advancements in technology and growing demand for customized solutions. As manufacturers adopt innovative techniques and materials, sand casting is poised to maintain its position as a vital manufacturing process in various industries. Moreover, with the increasing trend toward sustainability, there is potential for sand casting to evolve by incorporating more environmentally friendly practices and materials.
Conclusion
In conclusion, sand casting is a fundamental manufacturing process known for its simplicity, cost-effectiveness, and versatility. Its wide range of applications makes it indispensable in many industries. As technology continues to evolve, the sand casting process will likely adapt to meet the changing needs of modern manufacturing, ensuring its relevance for years to come. Whether you are a seasoned engineer or a curious learner, understanding sand casting will provide valuable insights into the world of manufacturing.
Post time:Ott . 01, 2024 12:07
Next:ข้อกำหนดสำหรับทรายเคลือบเรซิน