Understanding Sand Casting A Comprehensive Overview
Sand casting, also known as sand mold casting, is a versatile and widely used manufacturing process that involves the formation of metal parts through the creation of molds made from sand. This traditional technique has stood the test of time due to its simplicity, cost-effectiveness, and ability to produce intricate shapes and sizes. In this article, we will delve into the essence of sand casting, its processes, advantages, and applications, providing a well-rounded perspective on this important manufacturing method.
What is Sand Casting?
At its core, sand casting is a casting process that uses sand as the primary mold material. The process begins with the creation of a mold that is made from a mixture of sand, a binding agent, and water. This mixture is shaped around a pattern (which is a replica of the final product) and then hardened to form a cavity. Once the mold is prepared, molten metal is poured into the cavity, where it cools and solidifies, taking the shape of the mold. After the metal has cooled sufficiently, the sand mold is broken away, revealing the finished cast part.
The Sand Casting Process
The sand casting process can be broken down into several key steps
1. Pattern Making The first step involves creating a pattern of the desired part. Patterns can be made from various materials like metal, plastic, or wood. They closely represent the shape and dimensions of the final product.
2. Mold Preparation The pattern is used to form the sand mold. The sand mixture is compacted around the pattern to create the necessary cavity. In some cases, two halves of the mold (cope and drag) are made, which are then assembled.
3. Melting and Pouring After the mold is prepared, the selected metal alloy is melted in a furnace. Once at the required temperature, the molten metal is carefully poured into the mold cavity.
4. Cooling The molten metal is left to cool and solidify, a process that can take from minutes to hours, depending on the size and type of metal.
5. Mold Removal Once cooled, the sand mold is removed, often by simple mechanical means or by breaking it apart, revealing the metal casting.
6. Finishing Finally, the cast part may require additional finishing processes, such as sanding, machining, or painting, to achieve the desired surface quality and tolerances.
Advantages of Sand Casting
what is a sand casting
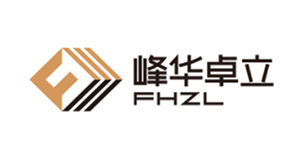
The popularity of sand casting can be attributed to several advantages
- Cost-Effectiveness Compared to other casting methods, sand casting is typically less expensive due to the low cost of sand and the relatively simple equipment required.
- Versatility Sand casting can be used to produce a wide variety of metal alloys and allows for casting of complex shapes that would be challenging in other processes.
- Size Range This technique can accommodate parts of various sizes, from small components to massive industrial pieces, making it suitable for diverse applications.
- Ease of Pattern Creation Patterns can be easily produced, and even modifications can be made without significant expense, allowing for rapid prototyping and experimentation.
Applications of Sand Casting
Sand casting finds applications across a wide range of industries due to its adaptability. Some common applications include
- Automotive Parts Many automotive components, such as engine blocks, transmission cases, and other critical parts, are produced using sand casting techniques.
- Aerospace The aerospace sector utilizes sand casting to manufacture lightweight yet strong components that meet precise specifications.
- Industrial Equipment A variety of machinery parts, tool components, and industrial equipment are often made through sand casting to ensure durability and reliability.
- Art and Sculpture Artists and sculptors frequently use sand casting to bring their designs to life, showcasing the artistic potential of this technique.
Conclusion
In conclusion, sand casting is a time-honored method of metal casting that combines efficiency, versatility, and cost-effectiveness. By understanding the various stages of the sand casting process, along with its numerous advantages and applications, one can appreciate why it remains a key player in the manufacturing landscape. Whether for industrial purposes or creative endeavors, sand casting continues to shape the future of metal fabrication.
Post time:Ott . 01, 2024 08:56
Next:Этапы песчано-литейного процесса для успешного литья изделий