Types of Sand Used in Foundry
Foundry work is an integral part of metal casting processes, where various materials are shaped into desired forms. Among these materials, sand plays a crucial role due to its properties that make it ideal for molding and core making. The choice of sand can significantly influence the final quality of the cast products. In this article, we will explore the different types of sand commonly used in foundries, each with its unique characteristics and advantages.
1. Green Sand
Green sand is one of the most widely used foundry sands. It is a mixture of silica sand, clay, water, and other additives. The green in green sand refers to its moisture content rather than its color. The clay acts as a binder, helping to hold the sand grains together while providing the necessary strength to the mold. One of the key advantages of green sand is its ability to retain moisture, which enhances the molding process. Additionally, it has excellent reusability, making it a cost-effective choice for many foundries. Green sand is primarily used for ferrous metal castings, especially in the production of large quantities of castings.
2. Resin Sand
Resin sand, also known as chemically bonded sand, utilizes synthetic resins as a binding agent. This type of sand is often used in the production of high-quality castings and is known for its superior strength and surface finish. The resin is typically added to the sand mixture in a specific ratio, and it hardens when exposed to heat or a chemical catalyst. The use of resin sand allows for intricate designs, as it can produce molds with precise details. However, the cost of resin sand is higher compared to green sand, which may limit its use in budget-sensitive operations.
3. Silica Sand
types of sand used in foundry
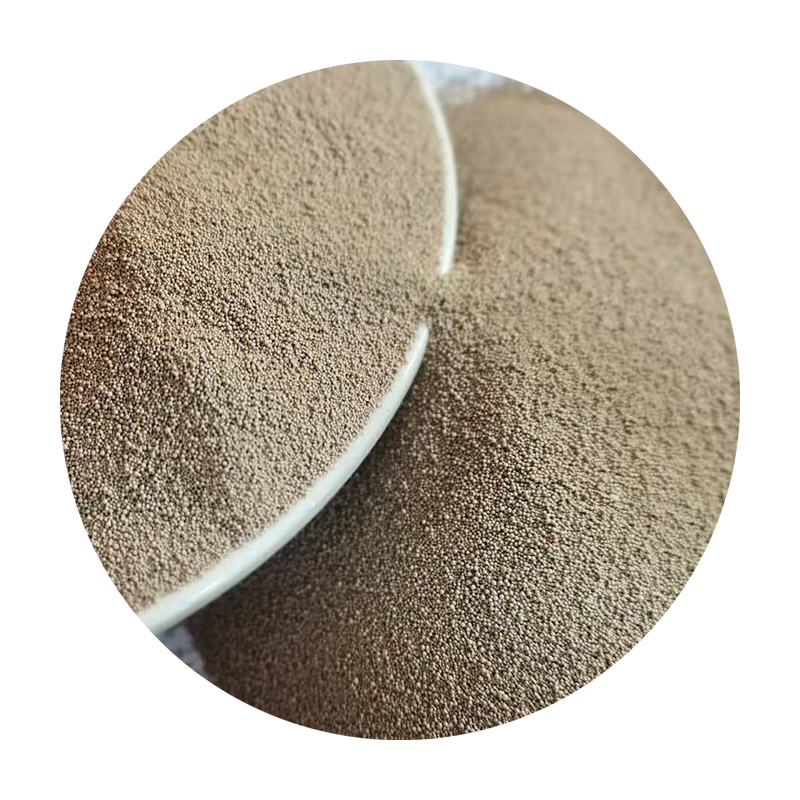
As the name suggests, silica sand comprises predominantly silica (SiO2) and is another common type of sand used in foundries. It is prized for its high melting point and excellent thermal stability, making it suitable for high-temperature applications. Silica sand is often used in conjunction with other binding agents to create molds that can withstand the demands of molten metal. Its fine and uniform grain size enhances the surface finish of castings, making it a preferred choice for high-quality products.
4. Chromite Sand
Chromite sand, composed primarily of chromium ore, is known for its excellent thermal resistance and low expansion properties. This type of sand is particularly useful for steel and iron castings because it can withstand the heat generated during the casting process without deforming. Moreover, chromite sand provides a smooth finish to the casting surface, which is vital for certain applications. However, due to its higher cost and limited availability, its use is often reserved for specialized foundry work.
5. Zircon Sand
Zircon sand is another specialty sand that is used in foundries, particularly for its high melting point and exceptional resistance to thermal shock. It is often employed in the production of molds for non-ferrous metals, including aluminum and magnesium alloys. Zircon's chemical stability reduces the likelihood of sand contamination, which can be crucial when casting reactive metals. Although zircon sand is more expensive than other types, its unique properties justify the investment for specific applications.
Conclusion
In summary, the type of sand used in foundry operations plays a critical role in the quality and efficiency of the casting process. Green sand remains the most popular choice due to its versatility and cost-effectiveness, while resin sand, silica sand, chromite sand, and zircon sand offer unique benefits for specialized applications. Understanding the characteristics of each type of sand will enable foundries to optimize their processes and achieve superior casting results.
Post time:Ott . 08, 2024 22:00
Next:Sanding Techniques for Achieving Smooth Finishes on Glazed Ceramics