Types of Foundry Sand An Overview
Foundry sand is a crucial component in the metal casting process, functioning as a mold material due to its ability to withstand high temperatures and provide excellent surface finish to cast components. Different types of foundry sand are used based on distinct properties required for various casting processes. Understanding these types is essential for optimizing the foundry operations and achieving the desired quality in cast products.
1. Silica Sand
Silica sand is the most commonly used type of foundry sand. Its high melting point and thermal stability make it ideal for various casting applications. Composed primarily of silicon dioxide (SiO2), silica sand is excellent for producing molds and cores. It is characterized by its grain shape, which can range from round to angular, depending on the source. Round grains are preferred for their flowability and packing properties, while angular grains are acknowledged for their strength and ability to retain shape during the casting process. Additionally, silica sand offers good permeability, allowing gases to escape during metal pouring, thus reducing defects.
2. Zircon Sand
Zircon sand is composed mostly of zirconium silicate (ZrSiO4) and is known for its high melting point and excellent thermal properties. It is often utilized in the production of high-performance molds and cores, especially for aluminum and high-temperature alloys. Zircon sand is less reactive with metal than silica sand, which makes it favorable for obtaining finer details and smoother surface finishes. Its unique properties also contribute to a lower likelihood of casting defects and improve the overall mechanical performance of the cast products.
3. Olivine Sand
types of foundry sand
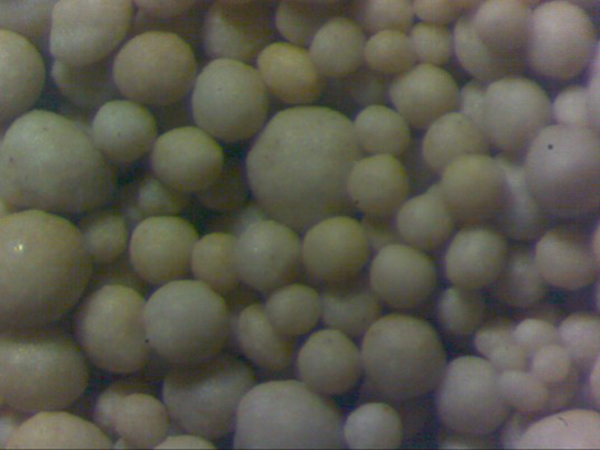
Olivine sand is derived from naturally occurring olivine minerals. It is recognized for its high heat resistance and good thermal conductivity. This type of sand is particularly advantageous in ferrous metal casting, as it can withstand high temperatures without degrading or reacting with the molten metal. Olivine sand also has a relatively low expansion rate, minimizing risks associated with mold distortion during the casting process. However, its availability is somewhat limited compared to silica sand, and thus it may not be as widely used.
4. Chromite Sand
Chromite sand, composed primarily of chromium oxide (Cr2O3), is another unique foundry sand type. It is characterized by its durability and resistance to thermal shock, making it suitable for high-temperature casting applications such as steel production. Chromite sand provides excellent mold strength and minimizes distortion during casting. However, its cost can be significantly higher than that of silica sand, which limits its use in some foundries.
5. Resin-Coated Sand
Resin-coated sand is formed by coating sand grains with a thermosetting resin, creating improved strength and durability. This type of sand offers excellent toughness and is particularly useful for creating intricate patterns. It can be used in both small and large scale production due to its versatility. The primary drawback, however, is the environmental concern surrounding the usage of resins, as they can emit volatile organic compounds (VOCs) during the curing process.
In conclusion, the type of foundry sand selected plays a critical role in the casting process, affecting the quality, efficiency, and cost of production. Foundries must consider various factors, including the type of metal being cast, the required surface finish, and environmental implications, when choosing the appropriate type of sand. By understanding the characteristics of different foundry sands, manufacturers can enhance the performance and reliability of their casting operations.
Post time:Set . 15, 2024 13:01
Next:Bauxite Sand