Sand Casting Techniques An Overview
Sand casting, one of the oldest and most versatile manufacturing processes, has been used for thousands of years to create metal parts and structures. This technique involves pouring molten metal into a mold made of sand, allowing the metal to cool and solidify into the desired shape. Given its robustness and adaptability, sand casting remains a popular choice in industries ranging from automotive to aerospace.
The Basic Process
The sand casting process can be broken down into several key steps
1. Pattern Making A pattern of the desired part is created, usually from materials such as wood, metal, or plastic. This pattern serves as a blueprint for the mold and is designed to be slightly larger than the final product to account for metal shrinkage during cooling.
2. Mold Preparation The pattern is then placed in a mixture of sand and a binding agent, typically clay. The sand is compacted around the pattern to create a mold. Once the mold is formed, the pattern is removed, leaving a cavity in the shape of the desired part.
3. Core Making (if necessary) If the part has internal cavities or complex geometries, cores are created using similar sand mixtures. These cores are placed in the mold before pouring the molten metal.
4. Metal Pouring The mold is heated, and the metal is melted using furnaces that reach extremely high temperatures. Once liquefied, the molten metal is poured into the mold, filling the cavity and surrounding any cores.
5. Cooling and Solidification As the metal cools, it solidifies into the shape of the mold. Cooling times vary based on the metal used and the size of the part.
6. Mold Removal and Finishing Once the metal has cooled, the sand mold is broken away to reveal the cast part. Additional finishing processes, such as grinding or machining, may be employed to achieve the desired surface finish and dimensional accuracy.
Advantages of Sand Casting
Sand casting offers numerous benefits, making it a favorable option for many applications
sand casting techniques
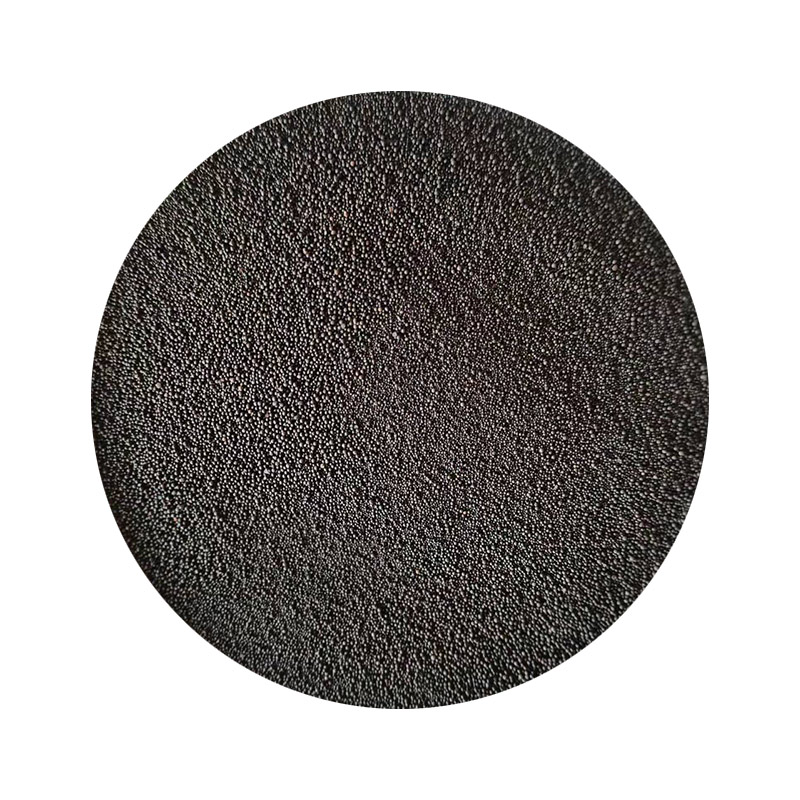
- Cost-Effective The materials required for sand molds are inexpensive and readily available, leading to low production costs, especially for large components.
- Versatility Sand casting can accommodate a wide range of metals and alloys, including aluminum, iron, and magnesium, making it suitable for various applications
.- Large Part Production This technique can efficiently produce large parts, which can be challenging with other manufacturing processes.
- Complex Geometries Sand casting allows for intricate designs and complex shapes, making it ideal for custom parts and prototypes.
Challenges and Limitations
Despite its many advantages, sand casting does have some limitations
- Surface Finish The surface finish of sand-cast parts tends to be rough compared to other processes, such as die casting. This may require additional machining or finishing.
- Dimensional Tolerances Sand casting generally cannot achieve the precise tolerances that precision machining processes offer, making it less suitable for applications requiring high precision.
- Environmental Considerations The use of silica sand poses health risks, and the process can generate dust and other pollutants, necessitating proper handling and environmental controls.
Innovations in Sand Casting
Recent advancements in technology have improved the sand casting process. Computer numerical control (CNC) machines are increasingly used for pattern making and mold creation, enhancing accuracy and efficiency. Additionally, the use of 3D printing technology for sand molds and cores has revolutionized the industry, enabling rapid prototyping and reduced lead times.
In conclusion, sand casting remains a cornerstone of manufacturing due to its unique blend of cost-effectiveness, versatility, and capability to create complex geometries. While it faces challenges such as surface finish and dimensional accuracy, ongoing technological advancements are continually enhancing its effectiveness. As industries evolve and demand for customized and high-quality parts increases, sand casting will undoubtedly continue to play a significant role in the manufacturing landscape.
Post time:Dic . 15, 2024 14:48
Next:make sand casting