Sand Casting An Essential Manufacturing Process
Sand casting, a traditional metal casting technique, plays a vital role in the manufacturing industry. With origins traced back thousands of years, this method continues to thrive due to its versatility, cost-effectiveness, and ability to produce intricate shapes. The process involves creating a mold from a mixture of sand, clay, and water, into which molten metal is poured to form a desired object.
The Composition of Sand
The primary ingredient in sand casting is silica sand, known for its high melting point and durability. This type of sand can withstand the extreme temperatures of molten metal, making it ideal for casting. To enhance its binding properties, clay, specifically bentonite, is often added to the sand. This mixture, when combined with water, creates a strong mold that can capture fine details of the pattern being cast.
The Sand Casting Process
The sand casting process begins with the creation of a pattern, usually made of metal or plastic. This pattern is an exact replica of the final product and is used to form the mold. The pattern is placed in the sand mixture, which is then compacted around it to form a mold. Once the mold is completed, the pattern is removed, leaving a cavity that resembles the desired object.
sand casting sand
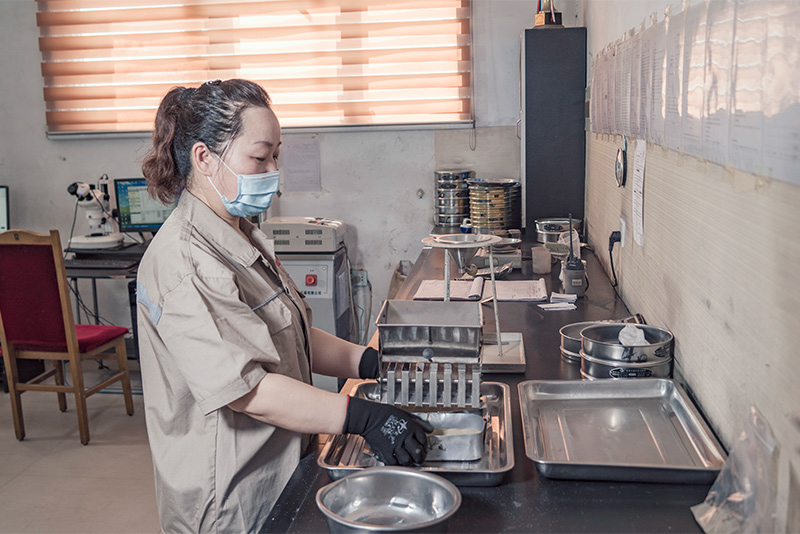
Next, the molten metal is poured into the mold cavity through a gating system, which helps control the flow and reduces turbulence. After the metal has cooled and solidified, the mold is broken apart to reveal the cast part. This process allows for the production of complex geometries, making sand casting suitable for various applications, from automotive components to artistic sculptures.
Benefits and Applications
One of the significant advantages of sand casting is its cost-effectiveness. The materials used are relatively inexpensive compared to other casting methods. Furthermore, sand molds can be reused several times, which adds to the economic efficiency of the process. The ability to work with different metals, including iron, aluminum, and bronze, also makes it a preferred choice for many manufacturers.
Sand casting has a wide range of applications across industries. In the automotive sector, it is commonly used to produce engine blocks, transmission cases, and various smaller components. In the aerospace industry, sand casting helps create lightweight parts that can withstand high-stress conditions. Additionally, artists often utilize this technique for creating sculptures and custom works, emphasizing its adaptability and importance.
Conclusion
In conclusion, sand casting remains a cornerstone of modern manufacturing due to its simplicity, affordability, and versatility. The process allows for the creation of diverse shapes and components that are integral to numerous industries. As technology advances, the sand casting process continues to evolve, ensuring its relevance in the ever-changing landscape of manufacturing.
Post time:Set . 24, 2024 18:26
Next:Optimizing Sand Mixtures for Enhanced Metal Casting Performance and Quality