The Sand Casting Foundry Process A Comprehensive Overview
Sand casting, one of the oldest and most versatile metal casting processes, has been utilized for centuries to create complex designs and shapes in various industries. This manufacturing process involves creating a mold from sand and pouring molten metal into that mold to produce a final product. Due to its ease of use, low cost, and adaptability, sand casting remains a favored technique in foundries today.
1. The Basics of Sand Casting
The sand casting process begins with the production of a mold, which serves as the negative cavity for the final product. The primary materials used for the mold are sand, a bonding agent (usually clay), and water, creating a mixture that can retain its shape when compacted. The first step involves creating a pattern, which is a replica of the object to be cast. Patterns are typically made from materials such as wood, metal, or plastic, depending on the complexity and size of the desired component.
2. Preparing the Mold
Once the pattern is created, it is placed in a flask, a rigid frame that holds the sand mixture. The mold is formed by packing sand around the pattern, ensuring that it conforms to the shape accurately. The compacted sand is then carefully removed, leaving a cavity that mirrors the pattern. Various methods can be employed to enhance the mold's properties, such as using resin-coated sand or adding additives to improve strength and thermal resistance.
After the mold is formed, it consists of two parts— the cope (top half) and the drag (bottom half). The two halves are then joined together, creating a complete mold with a hollow cavity for pouring molten metal.
3. Pouring the Metal
Once the mold is ready, the next crucial step is to prepare the molten metal. The selected metal—often aluminum, iron, or bronze—is heated in a furnace until it reaches a liquid state. Proper temperature control is essential to ensure the metal flows well into the mold and minimizes defects.
sand casting foundry process
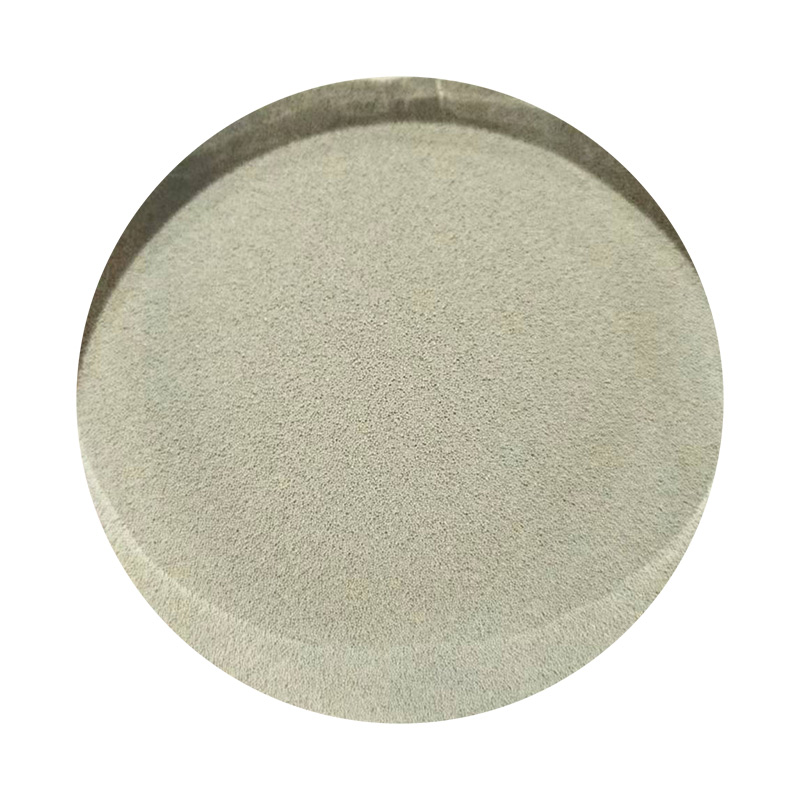
With the molten metal heated to the appropriate temperature, it is poured into the mold cavity through channels called sprues. As the metal fills the mold, it displaces any air, preventing air pockets that can lead to casting defects. The pouring process must be executed carefully to prevent turbulence, which could introduce impurities or cause the metal to oxidize.
4. Cooling and Solidification
Once the metal has been poured into the mold, it begins to cool and solidify. The cooling rate is critical as it affects the final properties of the cast metal. Too rapid cooling may lead to cracking, while insufficient cooling can result in poor mechanical properties. Typically, the metal is allowed to cool slowly in the mold for several hours, depending on the thickness and complexity of the casting.
5. Finishing the Cast
After the metal has solidified and cooled, the mold is broken away to reveal the casting. The next phase involves removing any excess material, known as flash, and performing finishing operations such as grinding, machining, or sandblasting to achieve the desired surface finish and dimensions. Depending on the intended application, additional processes like heat treatment or coating may be applied to enhance the material properties and durability of the final product.
6. Applications and Benefits
Sand casting finds extensive use across various industries, including automotive, aerospace, and manufacturing. Its ability to produce complex shapes and large components makes it an invaluable process. Moreover, the relative low cost associated with the materials and setup fosters its wide application, particularly for low to medium production runs.
Conclusion
The sand casting process is a time-tested method that combines artistry with engineering to produce precision metal components. With its simplicity, flexibility, and cost-effectiveness, sand casting continues to play an essential role in modern manufacturing, providing durable and intricately designed products to meet industry demands. Whether creating custom machinery parts or artistic sculptures, sand casting remains a cornerstone of metalworking technology.
Post time:Ott . 06, 2024 11:10
Next:steps in sand casting