The Importance of Sand Casting in Modern Manufacturing
Sand casting, a metal casting process, has been a cornerstone of manufacturing for centuries. It involves creating a mold from sand, into which molten metal is poured to create a desired object. This method is not only celebrated for its versatility but also for its efficiency in producing intricate designs and large-scale industrial components. As industries evolve and demand for precision and complexity increases, sand casting factories have adapted their techniques to meet these new challenges.
What is Sand Casting?
At its core, sand casting involves a few fundamental steps. First, a pattern of the desired item is created, which can be made of metal, plastic, or wood. This pattern is used to form a mold in a mixture of sand and binder. Once the mold is prepared, it is compacted to ensure stability during the pouring of molten metal. After the mold is set, molten metal - typically aluminum, iron, or bronze - is poured into it. Once cooled, the mold is broken apart, and the final cast is removed, often requiring additional finishing work.
Advantages of Sand Casting
One of the primary advantages of sand casting is its flexibility in design. The process can accommodate a wide variety of sizes, shapes, and materials, making it suitable for producing everything from small intricate parts to large industrial components. Manufacturers appreciate that sand casting can handle complex geometries that other methods may struggle with.
Another significant benefit is cost-effectiveness. The materials used are relatively inexpensive, and the process itself can be scaled easily, allowing for both small and large production runs. This scalability makes sand casting an appealing option for prototyping and mass production alike.
Moreover, sand casting is an environmentally friendly option compared to some other casting methods. The sand used in the process can often be reused multiple times, reducing waste and minimizing the environmental impact associated with raw material procurement.
sand casting factory
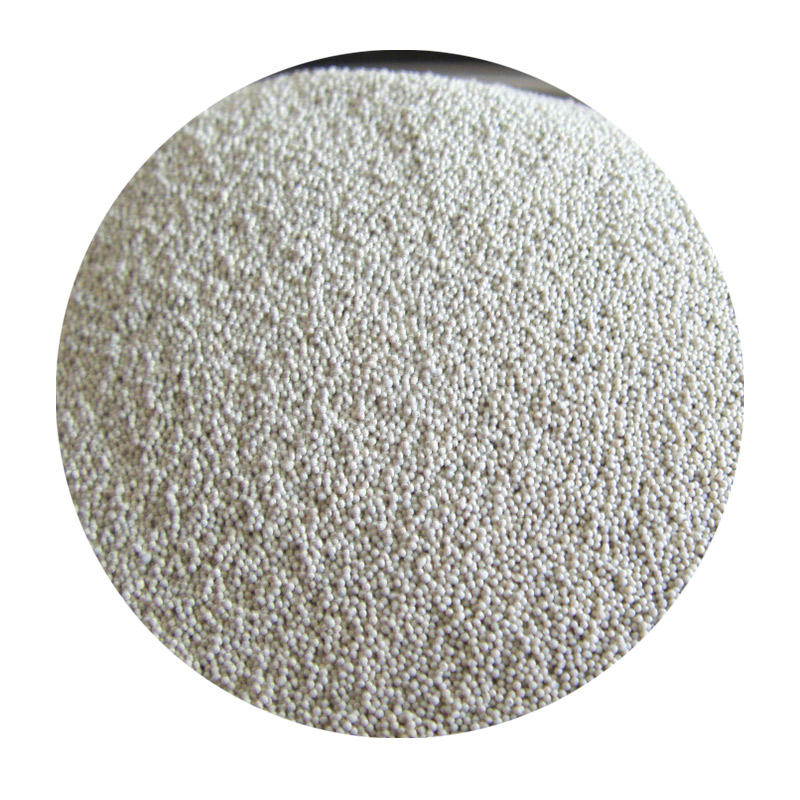
Advances in Technology
Modern sand casting factories have embraced technological advancements that improve quality and efficiency. Innovations such as computer-aided design (CAD) and computer-aided manufacturing (CAM) allow for more precise patterns and molds. Additionally, processes such as 3D printing are now being integrated into sand casting production, enabling rapid prototyping and the creation of complex mold shapes that were previously impossible to manufacture.
Automation in sand casting is also on the rise. Robotic arms and automated pouring systems reduce the risk of human error and increase production speed. These advancements create a more efficient workflow and help to meet the growing demands of industries such as aerospace, automotive, and heavy machinery.
The Role of Sand Casting in Industry
Sand casting remains a crucial method for producing components across various industries. In the automotive sector, for example, it is used to manufacture engine blocks, transmission cases, and other critical parts. The aerospace industry relies on sand casting for lightweight yet strong components that can withstand rigorous conditions.
Furthermore, as industries face increasing pressure to innovate and reduce costs, the role of sand casting is likely to grow. Its adaptability to new materials and designs positions it well in a rapidly evolving marketplace.
Conclusion
In conclusion, sand casting factories play a vital role in modern manufacturing. With its blend of cost-effectiveness, versatility, and the ability to produce complex geometries, sand casting continues to thrive despite the rise of advanced methods. The ongoing integration of technology into the sand casting process is a testament to its enduring relevance and adaptability in a continuously changing industrial landscape. As we look to the future, the sand casting process will undoubtedly continue to evolve, cementing its place as an essential manufacturing technique.
Post time:Dic . 19, 2024 12:57
Next:resin coated frac sand