Benefits of Sand Casting in Manufacturing
Sand casting, one of the oldest and most versatile manufacturing methods, has maintained its relevance in today’s industrial landscape due to its numerous advantages. This technique involves creating a mold from sand and using it to form metal components. The following discussion highlights the key benefits that make sand casting a preferred choice for many manufacturers.
1. Cost-Effective Production
One of the most significant advantages of sand casting is its cost-effectiveness. The materials required for sand casting, primarily sand and a binding agent, are relatively inexpensive. The process does not necessitate high-tech equipment, which further reduces production costs. This affordability makes sand casting an ideal choice for small and medium-sized enterprises (SMEs) looking to minimize expenses while producing quality components.
2. Design Flexibility
Sand casting offers unparalleled design flexibility. It can produce complex shapes and large components that may be challenging or impossible to fabricate using other methods. The technique allows for extensive modifications to patterns, enabling manufacturers to experiment with design and shape without significant financial consequences. This adaptability is particularly beneficial in industries such as aerospace and automotive, where intricate designs are often required.
Another benefit of sand casting is its compatibility with a wide range of materials. The process can accommodate various metals, including aluminum, bronze, iron, and magnesium, allowing manufacturers to select the most suitable alloy for their specific application. This versatility in material choice can lead to enhanced performance characteristics in the finished product, such as improved strength or lower weight.
4. Large-Scale Production Capabilities
sand casting benefits
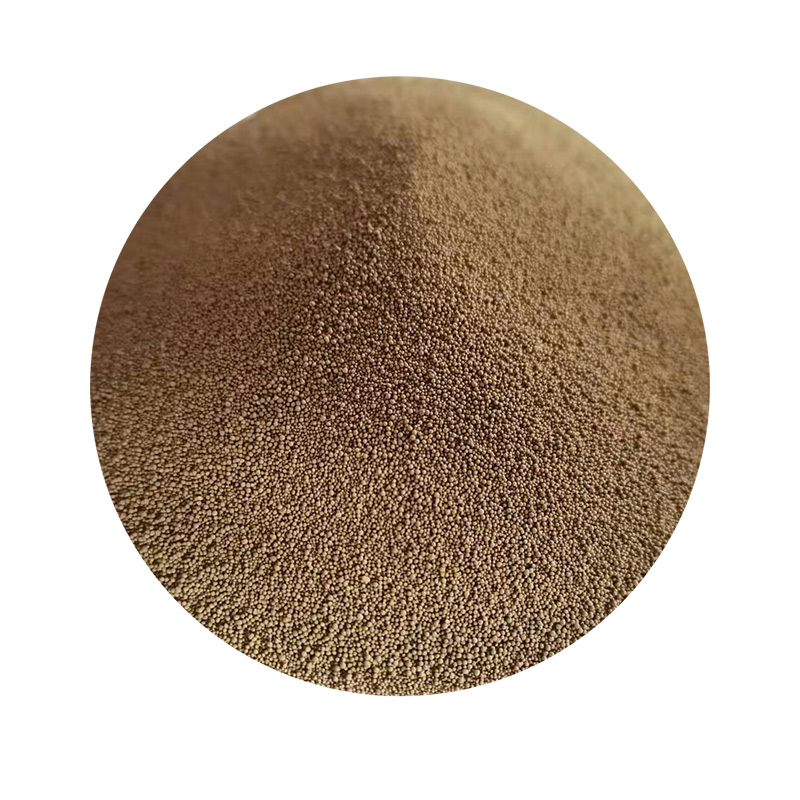
While sand casting is often employed for small production runs, it is equally capable of handling large-scale production. With the use of automated systems and advanced technologies, manufacturers can significantly increase their output without sacrificing quality. This scalability means that businesses can efficiently meet fluctuating demand while maintaining cost controls.
5. Reduced Waste
The sand casting process generates minimal waste material compared to other manufacturing methods. The sand used in the molds can often be reused multiple times, which not only lowers material costs but also contributes to sustainable manufacturing practices. This reduction in waste is increasingly important as industries strive to become more eco-friendly and comply with stringent environmental regulations.
6. Rapid Prototyping
Due to its simple setup and short lead times, sand casting is an excellent choice for rapid prototyping. Manufacturers can quickly create prototypes to test designs and functionalities before committing to mass production. This rapid iteration process can result in faster time-to-market for new products, giving companies a competitive edge in their respective industries.
7. Durability and Strength
Products manufactured through sand casting often exhibit excellent durability and strength. This is particularly true for iron and steel castings, which are known for their toughness. The ability to achieve intricate shapes while maintaining structural integrity makes sand casting a reliable choice for high-stress applications.
Conclusion
In summary, sand casting presents numerous benefits that make it a vital technique in modern manufacturing. Its cost-effectiveness, design flexibility, material versatility, ability to handle large-scale production, reduced waste generation, rapid prototyping capabilities, and the resultant durability of finished products position it as a preferred methodology for various industries. As manufacturing continues to evolve, sand casting will remain a critical component, enabling businesses to meet market demands efficiently while maintaining high-quality standards.
Post time:Ott . 13, 2024 01:25
Next:Tillämpningar av sandgjutning inom industri och hantverk