Advantages of Sand Casting
Sand casting, one of the oldest and most widely used metal casting processes, offers a multitude of advantages that make it an attractive option for manufacturers and engineers alike. This traditional technique, still relevant in contemporary manufacturing, capitalizes on the unique properties of sand to create intricate metal parts with a variety of applications. In this article, we will explore the key advantages of sand casting, which include versatility, cost-effectiveness, design flexibility, and reproducibility.
1. Versatility
One of the most significant advantages of sand casting is its versatility in producing a wide range of metal components. Sand casting can be used to create parts from various metals and alloys, including aluminum, iron, magnesium, and bronze. This versatility allows manufacturers to tailor the casting process to meet specific requirements of different industries, such as automotive, aerospace, and marine. Moreover, the process can accommodate both small-scale and large-scale production, making it ideal for a broad spectrum of applications.
2. Cost-Effectiveness
Another notable benefit of sand casting is its cost-effectiveness, particularly for small to medium-sized production runs. The materials used in sand casting, especially silica sand, are relatively inexpensive and readily available. Furthermore, the molds are often reusable, which can significantly reduce material costs. Unlike other casting processes that require intricate tooling and machining, sand casting setups can be less expensive to produce, making it a practical choice for startups and companies with budget constraints. Additionally, the simplicity of the sand casting process means that it often requires less investment in specialized equipment.
3. Design Flexibility
sand casting advantages
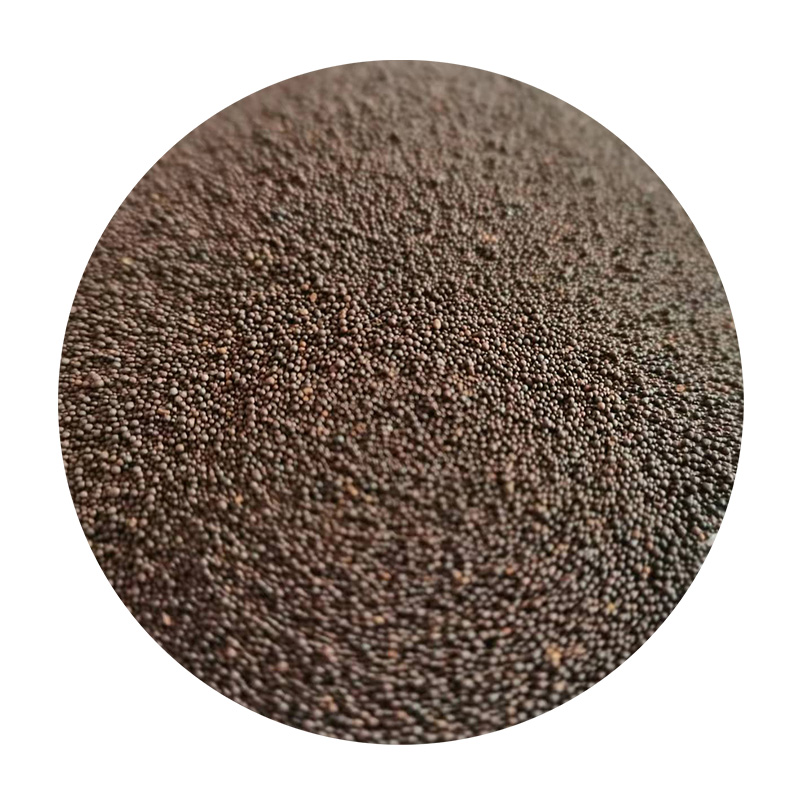
Design flexibility is perhaps one of the standout features of sand casting. The process allows for the creation of complex geometries and intricate details that may be challenging or expensive to achieve with other methods. Sand casting molds are made from a mixture of sand and a bonding agent, which gives the mold the ability to capture fine details and contours of the pattern being cast. This flexibility enables engineers to innovate and design parts that optimize performance while reducing the need for post-production machining. Whether it’s creating subtle fillets, thin walls, or oversized components, sand casting provides manufacturers with the creative freedom to expand their design horizons.
4. Reproducibility
Reproducibility is crucial in manufacturing, and sand casting excels in this area. Once a pattern is created, it can be used repeatedly to produce identical castings, ensuring consistency across large production runs. This capability is particularly important in industries where precise specifications and tolerances are vital. By using the same mold multiple times, manufacturers can achieve high levels of accuracy, which can be essential for components that need to fit together perfectly in assemblies. This reproducibility not only enhances quality control but also streamlines the production process, leading to increased efficiency.
5. Environmental Considerations
As the manufacturing sector increasingly focuses on sustainability, sand casting presents an environmentally friendly alternative. The primary raw material, sand, is abundant and can be reused multiple times before it requires replacement. Many foundries have adopted environmentally responsible practices, such as reclaiming sand and minimizing waste. Additionally, advancements in technology have made it possible to reduce emissions and energy consumption during casting, aligning sand casting with green manufacturing goals.
Conclusion
In summary, sand casting remains a highly advantageous manufacturing process that offers versatility, cost-effectiveness, design flexibility, and reproducibility. Its ability to produce complex components at a relatively low cost has made it a preferred choice for various industries. As manufacturers continue to seek efficient and sustainable methods of production, the time-honored technique of sand casting is likely to retain its prominence in the manufacturing landscape for years to come. With ongoing innovations and advancements in materials and processes, the future of sand casting looks bright, ensuring its relevance in an ever-evolving industry.
Post time:Ott . 01, 2024 11:21
Next:Фундамент бизнеси барои рехтани часпак бо масолеҳи масолеҳи хум.