Resin Coated Sand Process An Overview
The resin coated sand process has revolutionized the field of foundry applications, significantly improving the casting quality and mechanical properties of the final products. This innovative casting technique primarily utilizes sand grains coated with a specially formulated resin, which enhances the bonding characteristics and thermal stability during the metal pouring process.
At the core of the resin coated sand process is the preparation of the sand itself. Standard foundry sand is typically mixed with a thermosetting resin and a catalyst to facilitate the hardening process. This combination results in a sand that possesses excellent strength and thermal resistance. The resin coating not only helps the sand grains adhere together more effectively but also minimizes fines, which can adversely affect the casting surface quality.
One key advantage of the resin coated sand process is its ability to produce highly detailed and intricate patterns. The fine, uniform particle size of the resin coated sand allows for the creation of intricate mold designs, which are essential for modern manufacturing requirements. Moreover, the smooth surface finish achieved with this method reduces the need for extensive post-casting treatment, thereby streamlining the overall production process.
resin coated sand process
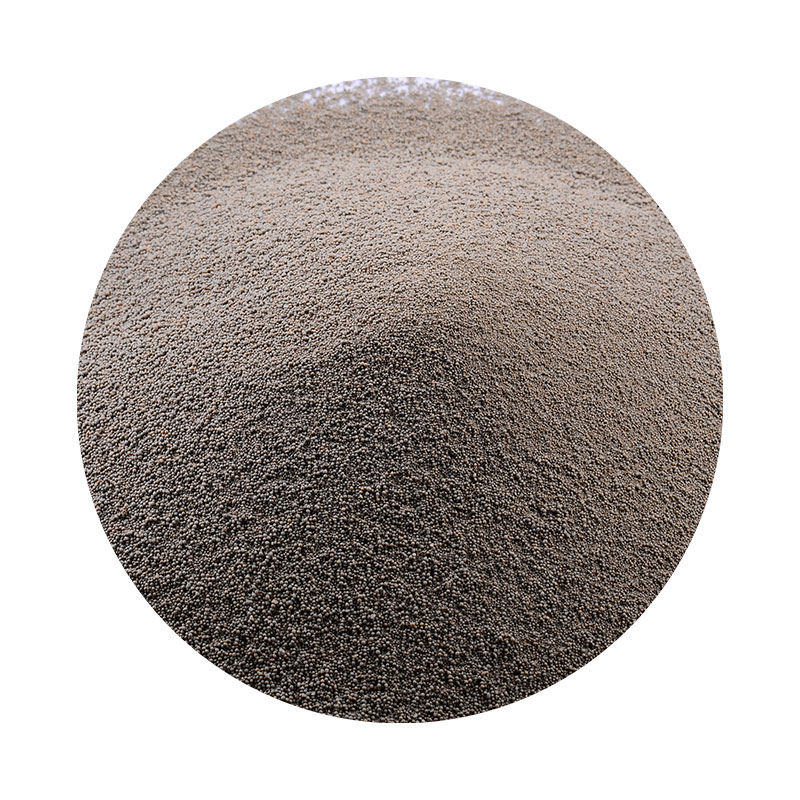
The resin used in this process can vary, but phenolic resins are among the most commonly utilized due to their superior properties. They offer excellent heat resistance and maintain their integrity even at high temperatures. The use of these resins allows for a reduction in gas generation, a common problem in traditional sand casting methods. This is crucial for preventing defects in the final cast products.
Once the resin coated sand is prepared, it is then molded into the desired shape using various techniques such as the jolt squeeze process or the shell mold process. In these methods, the sand molds are formed around patterns that define the final shape of the cast. After the molds are created, they are placed together and molten metal is poured in. The heat from the metal causes the resin to harden, forming a strong and durable mold.
Post-casting, the resin coated sand can be reclaimed for reuse. This reusability makes the process environmentally friendly and cost-effective. The reclaimed sand can be re-coated with resin for subsequent casting applications, minimizing waste and promoting sustainability within the foundry industry.
In conclusion, the resin coated sand process stands out as a preferred method for producing high-quality castings. Its ability to create intricate designs, combined with enhanced mold strength and reduced defects, makes it ideal for various applications including automotive, aerospace, and machinery components. As technology advances, the resin coated sand process is expected to evolve further, offering even greater efficiencies and improvements in the casting process. Embracing this innovative technique not only enhances the quality of the products but also supports industry efforts towards sustainability and waste reduction.
Post time:Set . 19, 2024 06:05
Next:the golden sands