Precision Sand Casting A Key Technique in Modern Manufacturing
Precision sand casting is a vital manufacturing process that has gained prominence in various industries, including automotive, aerospace, and machinery. This method offers a unique blend of versatility, cost-effectiveness, and high precision, which makes it an attractive option for producing complex components. In this article, we will explore the underlying principles of precision sand casting, its advantages, and its applications.
At its core, precision sand casting involves creating a mold from a pattern, typically made of metal or resin. The pattern is first encased in a specially formulated sand mixture, often combined with a binding agent. Once the sand has set, the mold is opened, and the pattern is removed, leaving a hollow cavity that replicates the desired component. Metal, usually in molten form, is then poured into this cavity, filling it to create the final casting.
One of the standout features of precision sand casting is its ability to produce parts with intricate geometries and tight tolerances. This is primarily achieved through advancements in computer-aided design (CAD) and computer-aided manufacturing (CAM) technologies. These tools enable manufacturers to design and fabricate patterns that precisely match the specifications of the intended casting, ensuring a high level of accuracy in the final product.
precision sand casting
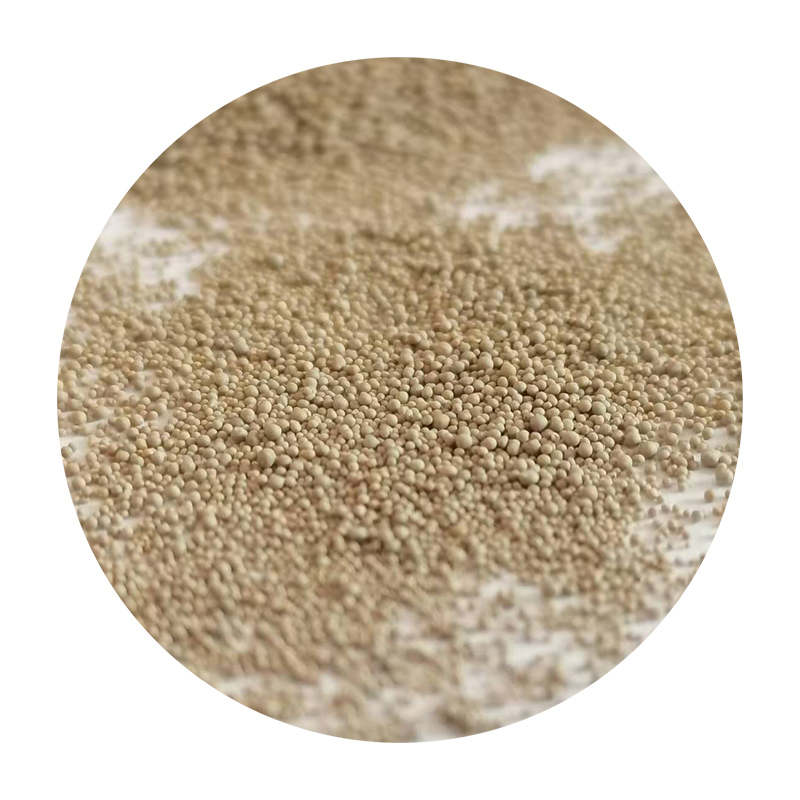
The use of high-quality, fine-grained sands allows for a smooth surface finish, which is essential for components that require minimal post-processing. Additionally, the sand casting process can accommodate a wide range of materials, including aluminum, iron, and steel, making it suitable for various applications. This adaptability has led to a resurgence of interest in sand casting, particularly in sectors where custom parts are frequently demanded.
Another significant advantage of precision sand casting is its cost-effectiveness, especially for small to medium production runs. The molds can be reused many times, reducing material waste and lowering overall manufacturing costs. Moreover, the scalability of the process allows manufacturers to produce both single prototypes and large batches efficiently. This flexibility is especially valuable in industries that are evolving rapidly, as it enables manufacturers to respond to changing market demands without incurring exorbitant costs.
Despite its many benefits, precision sand casting is not without its challenges. Achieving the perfect balance between mold strength and permeability is crucial, as a weak mold can lead to defects like cracks and miscasts. Advances in materials and techniques have been developed to mitigate these issues, but operators must still pay close attention to the molding process to ensure quality.
In conclusion, precision sand casting represents a sophisticated blend of traditional casting techniques and modern technological advancements. Its capacity for producing high-precision components at a relatively low cost makes it an indispensable part of contemporary manufacturing. As industries continue to innovate, the importance of precision sand casting will likely grow, solidifying its role as a cornerstone in producing complex, high-quality parts. Whether it’s in automotive engines, aerospace components, or intricate machinery parts, precision sand casting is sure to remain a preferred method for manufacturers looking to meet the demands of a rapidly evolving marketplace.
Post time:Ott . 07, 2024 03:14
Next:lost foam casting method