Open Sand Casting A Comprehensive Overview
Open sand casting, a traditional method of metal casting, has been an integral part of manufacturing for centuries. This process involves pouring molten metal into a sand mold to create various metal products, ranging from intricate components to large structural parts. With its unique advantages and specific applications, open sand casting remains a vital technique in many industries today.
The Process of Open Sand Casting
The open sand casting process begins with the creation of a mold, which is typically made from a mixture of sand, clay, and water. The quality of the mold directly impacts the final product, making it essential for manufacturers to maintain a consistent sand mixture. The first step involves creating a pattern, which is a replica of the final object. Patterns can be crafted from various materials, including wood, metal, or plastic, and they can be either solid or hollow, depending on the requirements of the finished piece.
Once the pattern is ready, it is placed into a sand mixture, which is then compacted around it to form the mold. After the mold has set, the pattern is removed, leaving a cavity that reflects the shape of the desired item. The two halves of the mold are then reassembled, and molten metal is poured into the cavity. This metal can be aluminum, cast iron, or other alloys, chosen based on the specific properties required for the final product.
The casting process requires careful precision. As the molten metal flows into the mold, it must be poured at the correct temperature and speed to ensure that it fills every crevice without creating air pockets or imperfections. After the metal has cooled and solidified, the mold is broken apart to reveal the cast product. Finally, any excess material or imperfections are removed through machining, and the item is polished to achieve a smooth surface finish.
Advantages of Open Sand Casting
One of the most significant advantages of open sand casting is its versatility. It can produce a wide range of sizes and shapes, making it suitable for various industries, including automotive, aerospace, and construction. The flexibility in design also enables engineers and designers to create complex geometries that may be difficult to achieve with other casting methods.
open sand casting
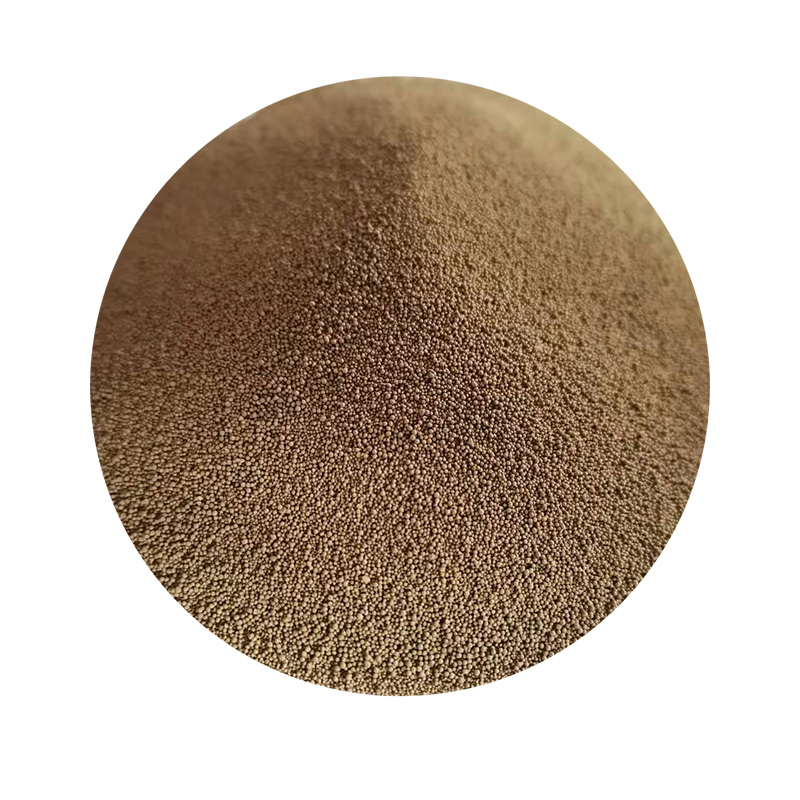
Cost-effectiveness is another notable benefit. The materials required for open sand casting, primarily sand, are relatively inexpensive and widely available. Moreover, because the process allows for large production runs, manufacturers can benefit from economies of scale, reducing the cost per unit significantly.
Additionally, open sand casting is a low-tech process that does not necessarily require advanced machinery. This accessibility makes it an attractive option for small and medium-sized enterprises (SMEs) that may not have the budget for more automated casting methods.
Challenges and Considerations
While open sand casting has numerous advantages, it also comes with its own set of challenges. One primary concern is the potential for defects in the casting, such as porosity, shrinkage cavities, and surface imperfections. These issues can arise from factors such as improper mold preparation, incorrect pouring techniques, or inadequate cooling times.
Another challenge is the requirement for skilled labor. Although the process is less reliant on high-tech machinery, it does demand a certain level of expertise to ensure that the mold is prepared correctly and that the casting process is executed flawlessly. Proper training and experience are vital for minimizing defects and maximizing production efficiency.
Environmental considerations are also increasingly relevant in today’s manufacturing landscape. The disposal of used sand and other materials presents sustainability challenges, and manufacturers need to adopt practices that minimize waste and reduce environmental impact.
Conclusion
Open sand casting is a time-honored manufacturing technique that continues to play a crucial role in producing metal components across a range of industries. Its versatility, cost-effectiveness, and simplicity make it an attractive option for many manufacturers, providing a foundation for innovation in product design and engineering. However, it is essential for businesses to remain vigilant about potential pitfalls and embrace sustainable practices to ensure the continued success and viability of this traditional casting method in the modern world. As industries evolve and adapt to new technologies, open sand casting is likely to remain a fundamental process, blending tradition with innovation in the quest for superior metal products.
Post time:Dic . 30, 2024 09:17
Next:sand casting conclusion