Lost Foam Metal Casting An Overview of an Innovative Technique
Lost foam metal casting is a modern manufacturing technique that combines the benefits of traditional sand casting with the advantages of advanced modeling processes. This method has revolutionized the way metal parts are produced, offering increased efficiency, precision, and flexibility. The lost foam casting process involves using a foam pattern as a mold, which is then replaced by molten metal to create intricate and complex shapes. This article explores the principles, benefits, applications, and future of lost foam metal casting.
Principles of Lost Foam Casting
The lost foam casting process begins with the creation of a foam pattern that is an exact replica of the desired metal part. The pattern is typically made from polystyrene foam, which is lightweight and easily shaped. Once the pattern is produced, it is coated with a thin layer of a refractory material, such as sand or ceramic. This coating serves to protect the foam during the pouring of molten metal and forms the final mold.
Here’s how the process works
1. Foam Pattern Creation The foam pattern can be created using various methods, including CNC machining or 3D printing, allowing for highly complex designs. 2. Coating The pattern is coated with a fine layer of sand mixed with a binding agent. This layer hardens, forming a shell around the foam.
3. Mold Assembly The coated foam patterns are then assembled into a mold box, where they are tightly packed to minimize any gaps.
4. Pouring Molten Metal When molten metal is poured into the mold, it comes into contact with the foam, causing it to vaporize. This creates an accurate impression of the foam pattern in the sand, resulting in the final metal part.
5. Cooling and Finishing Once the metal has cooled and solidified, the mold is broken apart, revealing the finished part that requires minimal further processing.
Benefits of Lost Foam Casting
lost foam metal casting
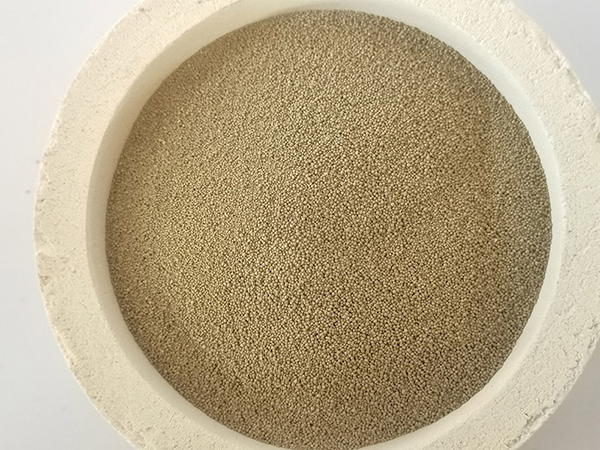
One of the paramount benefits of lost foam metal casting is its ability to produce complex geometries with high precision. Traditional casting methods often struggle with intricate designs, leading to the need for additional machining. However, lost foam casting allows manufacturers to create parts that closely match their specifications right from the mold.
Another advantage is the reduction of waste material, as the foam pattern fully integrates into the final product. This leads to lower material costs and environmental impact, making the process more sustainable. Additionally, the technique permits the production of lighter and stronger components, which is particularly beneficial in industries such as aerospace and automotive.
Lost foam casting also accelerates production times. The ability to create molds with complex shapes means that assembly processes can be simplified, reducing the number of parts required and simplifying the manufacturing workflow. This contributes to an overall decrease in production lead times.
Applications of Lost Foam Casting
The applications of lost foam metal casting are vast and span various industries. Its ability to produce intricate and high-quality components makes it an ideal choice for sectors like aerospace, automotive, and marine manufacturing. For example, lost foam casting is often used to produce engine blocks, transmission cases, and other complex parts that require precise specifications and high strength-to-weight ratios.
Other applications include agricultural machinery, industrial equipment, and even artistic sculptures, proving that this technique can cater to both functional and aesthetic needs. The flexibility of design afforded by lost foam casting also opens up opportunities for rapid prototyping, enabling manufacturers to quickly iterate on designs before final production.
The Future of Lost Foam Casting
As technology advances, the future of lost foam metal casting looks promising. Ongoing developments in materials science, especially in the realm of foam types and refractory coatings, are likely to enhance the performance and efficacy of the process. Moreover, with the rapid adoption of 3D printing technology, the ability to create intricate foam patterns is becoming faster and more accessible.
Furthermore, as industries continue to prioritize sustainability, lost foam casting’s reduced waste and energy requirements position it as an attractive option moving forward. The method’s capacity for lower emissions and resource conservation aligns well with global movements toward greener manufacturing practices.
In conclusion, lost foam metal casting represents a significant advancement in manufacturing technology. Its unique approach allows for the production of complex metal parts with high precision and minimal waste, making it an efficient, flexible, and environmentally friendly choice for various applications. As the industry continues to evolve, lost foam casting is poised to play a pivotal role in the future of metal manufacturing.
Post time:Set . 25, 2024 16:45
Next:g2 super sand