Casting Sand The Backbone of Metal Foundries
Casting sand, often referred to as molding sand, plays a pivotal role in the metal casting industry. It is a crucial material used to create molds in which molten metal is poured to form various metal components ranging from everyday items to complex industrial parts. Understanding the composition, types, properties, and applications of casting sand sheds light on its significance and utility in manufacturing processes.
At its core, casting sand is primarily composed of silica (SiO2), which provides the necessary thermal stability and strength to withstand the high temperatures of molten metal. In addition to silica, other materials like clay, water, and various additives are combined to enhance the sand's properties. Clay acts as a binding agent that holds the grains of sand together, while water helps to improve the mold's plasticity and flexibility. This combination is essential for ensuring that the mold can withstand the casting process without breaking apart or collapsing.
Casting sand can be categorized into different types based on its characteristics and the specific requirements of the casting process. One commonly used type is green sand, which is a mixture of silica sand, clay, and water. Green sand is notable for its excellent moldability and ability to produce smooth surface finishes on castings. Due to its affordability and ease of use, green sand is the most widely employed molding material in iron and steel foundries.
Another popular type is resin-bonded sand, which uses resin as a binding agent instead of clay. This type of sand offers higher strength and better dimensional accuracy, making it ideal for intricate designs and thinner wall sections. However, the use of resin-bonded sand often involves additional processing steps and can result in higher production costs. Therefore, foundries must weigh the benefits against the expense depending on the specific application.
casting sand
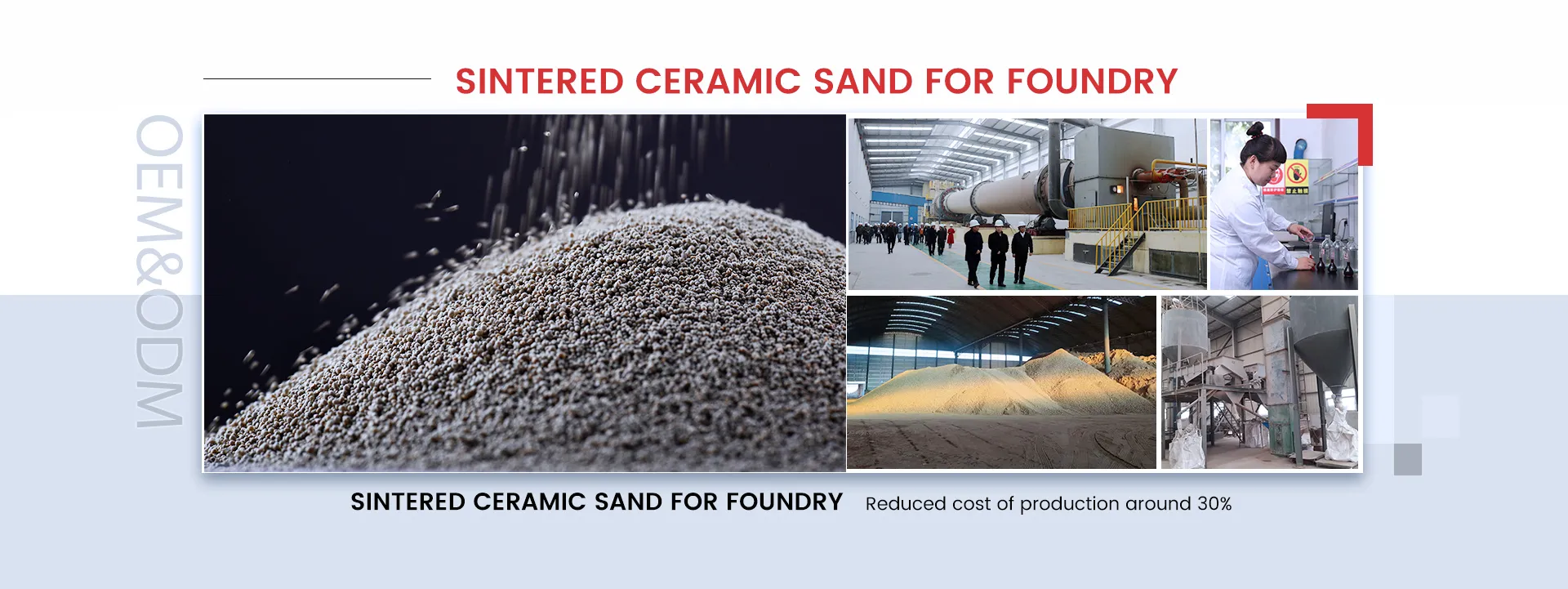
The properties of casting sand are crucial for determining the quality of the final casting
. Factors such as grain size, shape, and distribution influence the sand's ability to form precise molds and the overall surface finish of the cast product. Fine-grained sands produce smooth surfaces but may require more care to ensure they maintain structural integrity. Conversely, coarse-grained sands can create rougher surfaces but offer superior mold strength, making them advantageous for specific applications.Beyond the selection of sand types, the preparation and maintenance of casting sand are vital for successful operations in any foundry. Regular testing for moisture content, grain composition, and strength is necessary to ensure the sand meets the required specifications for each casting project. Moreover, spent sand can be recycled and processed to extend its lifespan, making the use of casting sand both economically and environmentally sustainable.
In recent years, there has been a growing interest in developing eco-friendly alternatives to traditional casting sands. Researchers are exploring organic binders and additives that can reduce the environmental impact of sand casting operations. Innovations in technology and material science are paving the way for enhanced foundry practices that are not only efficient but also sustainable.
In conclusion, casting sand is not just a humble raw material; it is a fundamental component of the metal casting process that influences the productivity and quality of manufactured goods. With its varied types and essential properties, the right selection and handling of casting sand can significantly affect the final outcome of metal castings. As the foundry industry continues to evolve, the focus on sustainability and efficiency will shape the future of casting sands, ensuring that this vital material remains at the forefront of manufacturing innovation.
Post time:Ott . 22, 2024 11:39
Next:metal casting sand for sale