Application of Sand Casting Process
Sand casting is one of the oldest and most widely used metal casting processes. It involves creating a mold from sand to produce metal parts. This method is celebrated for its versatility, cost-effectiveness, and capability to create complex shapes. In this article, we will explore the applications, advantages, and challenges associated with sand casting.
One of the primary applications of sand casting is in the automotive industry. Car manufacturers use sand casting to produce engine blocks, transmission cases, and other critical components. The process allows for the creation of large, intricate parts that are lightweight yet strong, meeting the rigorous demands of vehicle performance and safety. Additionally, sand casting is scalable, making it suitable for both prototype development and large-scale production runs.
Another significant application of sand casting is in the aerospace sector. Components such as turbine blades, frames, and brackets require precision and reliability. Sand casting provides the required flexibility to create aerospace parts that can withstand high temperatures and extreme conditions. The ability to produce complex geometries without extensive tooling makes this method particularly advantageous for small production runs or the development of new designs.
The heavy equipment and machinery industry also benefits from sand casting. Large machine components, such as housings for pumps and gearboxes, are often produced using this method. The durability and strength of sand-cast parts make them ideal for applications in which the equipment must endure heavy loads and harsh operating environments. Furthermore, sand casting is suitable for producing components in various sizes, from small parts to large, heavy-duty components.
application of sand casting process
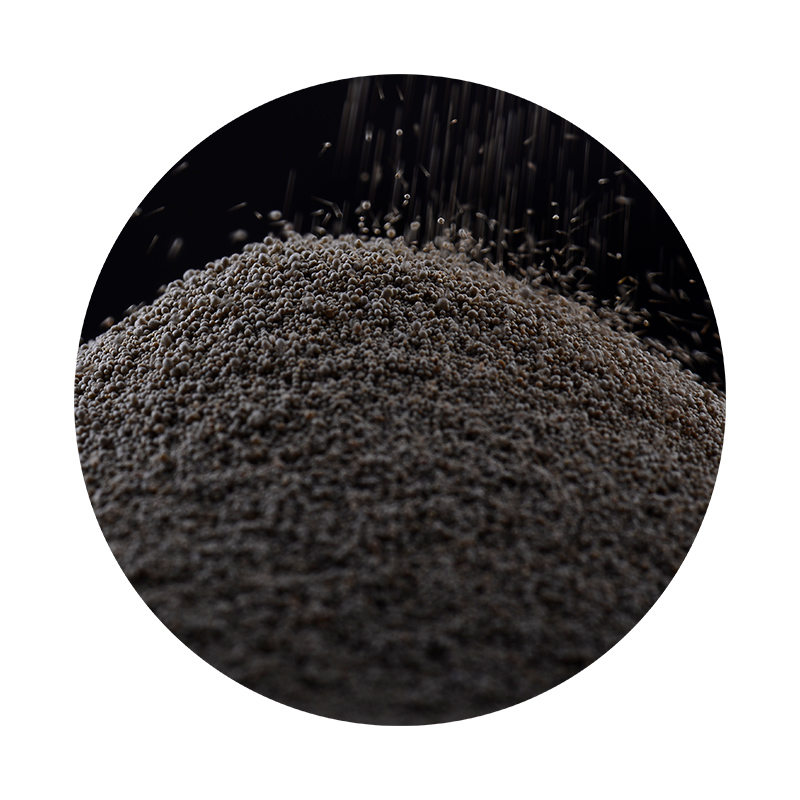
In addition to these industries, sand casting is commonly employed in the production of artistic sculptures and decorative items. Many artisans and manufacturers utilize sand casting to create intricate designs that would be challenging to achieve with other methods. The malleability of sand allows for detailed patterns and textures, which can enhance the aesthetic appeal of the final product.
Despite its numerous advantages, sand casting does face challenges. One of the main issues is the potential for defects, such as sand inclusions, gas porosity, or misalignment of the mold. These defects can affect the mechanical properties of the finished product. Moreover, sand casting usually requires further processing, such as machining, to achieve the desired surface finish and dimensional accuracy.
Technological advancements have addressed some of these challenges, incorporating sophisticated simulation and monitoring systems to optimize the casting process. Developments in binder materials and sand mixtures also improve the quality and efficiency of sand casting operations.
In conclusion, sand casting is a vital manufacturing process with a broad range of applications across numerous industries, particularly automotive, aerospace, and heavy machinery. Its ability to produce intricate and large components makes it an indispensable technique, despite certain inherent challenges. As advancements continue to evolve, the future of sand casting looks promising, assuring its relevance in modern manufacturing. The process not only contributes to effective production but also plays a significant role in innovation and design.
Post time:Set . 18, 2024 23:16
Next:Förlorad skumgjutning