Types of Sand Casting Process
Sand casting is a widely utilized manufacturing process in which molten metal is poured into a mold made from sand to create complex metal parts. This method is particularly favored for its versatility, cost-effectiveness, and ability to produce large-scale and intricate designs. While there are various types of sand casting processes, the most common include the green sand casting process, no-bake sand casting, and lost foam sand casting. Each of these methods has its own unique characteristics and applications.
Green Sand Casting
Green sand casting is the most traditional and widely used sand casting method. The term green refers to the moisture content in the sand, which is mixed with clay and water to form a pliable material. The mixture retains its shape during the casting process and provides excellent moldability.
In this process, the green sand is compacted around a pattern of the desired part. Once the mold is formed, the pattern is removed, leaving a cavity that will be filled with molten metal. One of the key advantages of green sand casting is its ability to produce intricate shapes and details. Additionally, it is cost-effective and suitable for both small and large production runs.
Green sand casting is often employed in the production of engine blocks, pipe fittings, and various automotive parts
. However, it can require additional finishing processes to remove imperfections, as the surface finish may not be as smooth as other casting methods.No-Bake Sand Casting
No-bake sand casting, also known as air-set casting, utilizes a different approach compared to green sand casting. In this process, a resin binder is mixed with the sand, and the mold is formed without the need for moisture. The resin hardens at room temperature, creating a strong and durable mold.
types of sand casting process
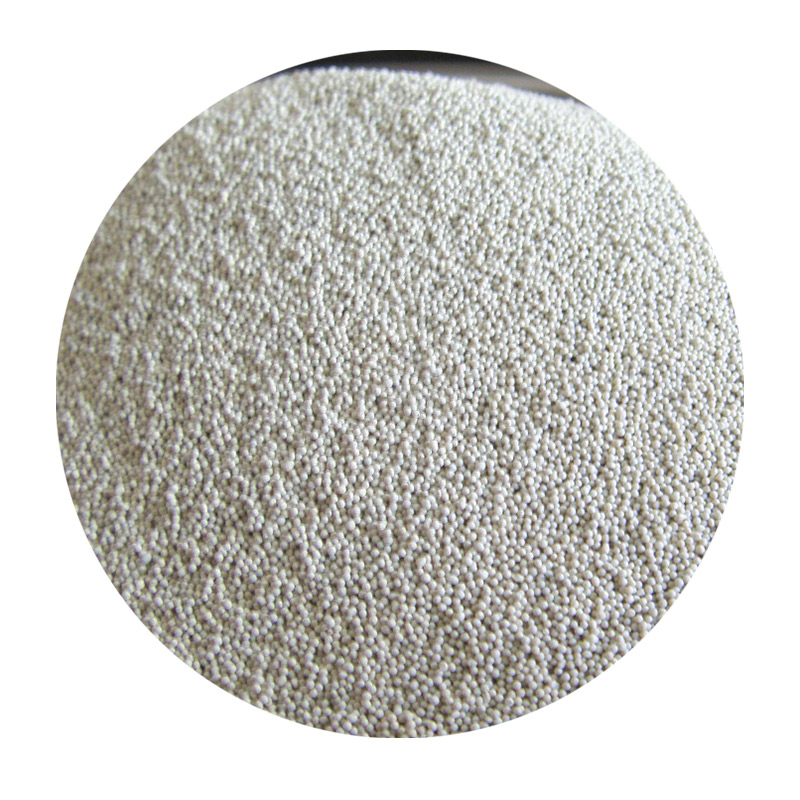
One of the significant benefits of no-bake sand casting is the ability to produce molds with a superior surface finish and greater dimensional accuracy. This makes it ideal for high-precision components. The no-bake process also enables manufacturers to create larger and more complex molds than typically possible with green sand casting.
No-bake sand casting is widely used across diverse industries, including aerospace, defense, and the production of intricate machinery components. However, it requires careful handling and quality control of the resin binder to ensure optimal performance during the casting process.
Lost Foam Sand Casting
Lost foam sand casting is an innovative process that combines the benefits of sand casting with the precision of investment casting. This method uses a foam pattern, typically made from polystyrene, which is coated in a sand mixture. The foam pattern is then placed into a mold, and when molten metal is poured into the cavity, it vaporizes the foam, allowing the metal to take its shape.
The lost foam process offers several advantages, including a high level of accuracy, excellent surface finish, and reduced need for machining. It is particularly effective for producing complex shapes and parts with undercuts that may be challenging to achieve with traditional molding techniques.
Lost foam casting is commonly used in applications such as automotive components, industrial machinery, and even artistic sculptures. However, it can involve relatively higher costs associated with the foam patterns and the special handling required during casting.
Conclusion
In summary, sand casting is a fundamental manufacturing process that serves as the backbone of metal part production across various industries. The primary types of sand casting—green sand casting, no-bake sand casting, and lost foam sand casting—each offer unique advantages tailored for specific applications. By understanding these different methods, manufacturers can select the most suitable process to meet their production needs, offering flexibility and scalability for a wide range of metal components. Whatever the choice, sand casting remains an indispensable technique for modern manufacturing, enabling the creation of complex and high-quality metal parts.
Post time:okt . 13, 2024 19:07
Next:Types of Sand Suitable for Effective Sand Casting Processes