Sand Casting Techniques An Overview
Sand casting, one of the oldest and most versatile metal casting techniques, has stood the test of time due to its efficiency and adaptability. This method involves creating a mold from a sand mixture, which is then used to form metal objects. With applications ranging from automotive components to intricate artistic sculptures, sand casting remains a pivotal manufacturing process.
At the heart of sand casting lies the mold-making process. The primary materials employed are fine sand, binder, and water. The most common type of sand used is silica sand, which possesses excellent thermal stability and is readily available. The sand is mixed with a binder, typically clay, and water to create a mixture that can retain shape when compacted. The mold is created by packing this mixture around a pattern, which is the negative impression of the desired object.
Sand Casting Techniques An Overview
Once the mold is prepared, the next step is to pour the molten metal into the cavity. The metal is typically heated to a liquid state in a furnace before being carefully poured. The pouring process requires skill and precision, as any misalignment can lead to defects, such as misruns or cold shuts. After the metal has cooled and solidified, the mold is removed, revealing the cast object.
sand casting techniques
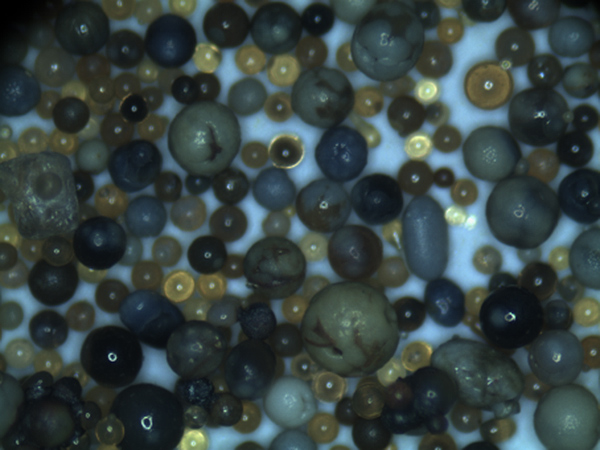
Post-casting operations are essential to ensure the quality and integrity of the final product. This includes cleaning, removing excess material, and performing any necessary machining. Furthermore, inspections are often conducted to detect any defects, such as shrinkage or porosity.
The advantages of sand casting are manifold. It is a cost-effective process, particularly for small production runs, and it allows for the casting of large, complex shapes. Additionally, sand casting is suitable for a wide range of metals, including aluminum, iron, and bronze, making it highly versatile.
However, the technique is not without its challenges. The quality of the cast can be influenced by factors like the sand's moisture content and the quality of the binder. Moreover, while sand casting can achieve detailed designs, the surface finish may not be as smooth as those obtained through other casting methods like investment casting.
In recent years, advancements in technology have further enhanced sand casting techniques. The introduction of computer-aided design (CAD) and simulation software enables manufacturers to optimize mold designs and predict potential defects before casting. Moreover, innovations in materials and processes continue to improve the efficiency and sustainability of sand casting operations.
In conclusion, sand casting is a fundamental technique in the metalworking industry that combines tradition with modern advancements. Its adaptability, cost-effectiveness, and ability to produce intricate designs ensure that it remains a critical method for manufacturers around the world.
Post time:nóv . 15, 2024 11:10
Next:ceramsite foundry sand