Sand Casting Steel An Overview
Sand casting, one of the oldest forms of metal casting, continues to play a pivotal role in manufacturing processes, particularly in the steel industry. This method utilizes sand as the primary mold material and is favored for its flexibility, cost-effectiveness, and ability to produce complex shapes and intricate designs. Unlike other casting techniques, sand casting does not require expensive tooling, making it an attractive option for both small-scale and large-scale production.
The Sand Casting Process
The sand casting process begins with the creation of a pattern, which is typically made from metal, plastic, or wood. This pattern represents the final object to be produced and is used to form the mold in which molten steel will be poured. The pattern is placed in a mold box, and sand is then compacted around it, forming a negative impression. The type of sand used is usually silica sand, mixed with a binding agent such as clay to enhance its strength and stability.
Once the sand has set, the mold is prepared for pouring. The pattern is removed, leaving a cavity that mirrors the shape of the intended steel component. This cavity is then treated with a release agent to ensure the finished product can be easily removed after casting. The next step involves heating the steel until it reaches a molten state, after which it is poured into the mold cavity.
Advantages of Sand Casting
One of the primary advantages of sand casting steel is its versatility. The method is capable of producing a variety of shapes and sizes, ranging from small parts weighing just a few grams to massive components in the ton range. This adaptability makes sand casting suitable for many industries, including automotive, aerospace, and construction. Furthermore, it is effective for both low-volume and high-volume production runs.
sand casting steel
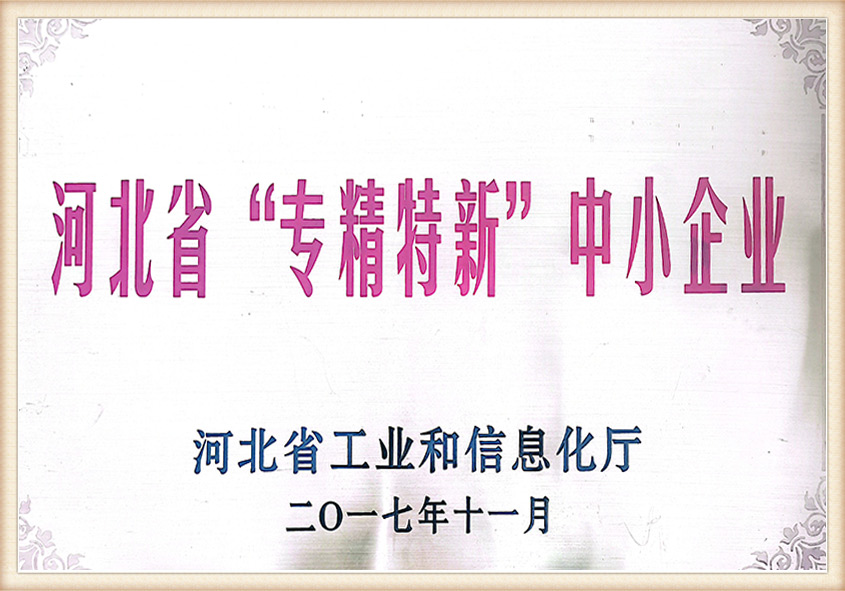
Cost is another significant factor in favor of sand casting. The materials needed for sand molds are relatively inexpensive compared to other casting techniques, such as die casting or investment casting. Additionally, the process does not require the same level of precision as other methods, allowing manufacturers to save on both time and labor.
Challenges in Sand Casting
Despite its advantages, sand casting does come with some challenges. The quality of the final product can be influenced by various factors, including the mixture of the sand, the temperature of the molten steel, and the accuracy of the pattern. Potential issues such as inclusions, porosity, and dimensional inaccuracies can arise during the casting process, necessitating careful monitoring and control.
To mitigate these challenges, manufacturers often invest in advanced technologies and methodologies. For example, computer-aided design (CAD) software assists in optimizing patterns and molds for better accuracy and efficiency. Additionally, the integration of automated systems can enhance the consistency of the sand mixture and improve the overall quality of the castings.
Conclusion
In summary, sand casting steel remains a prominent technique in the manufacturing landscape due to its versatility, cost-effectiveness, and ability to produce complex components. While challenges exist, advancements in technology continue to improve the process, making it more efficient and reliable. As industries evolve and demand for intricate steel parts grows, sand casting is expected to remain an integral part of metal production, heralding a promising future for this age-old method.
Post time:nóv . 12, 2024 11:31
Next:components of sand casting