Understanding Sand Casting Definition and Process
Sand casting, also known as sand mold casting, is one of the oldest and most widely used metal casting processes in the manufacturing industry. This method involves shaping molten metal into a desired form by pouring it into a mold that is made of sand. The versatility and cost-effectiveness of sand casting have made it an essential technique for producing a wide range of metal components, from small intricate items to large heavy-duty parts.
Definition of Sand Casting
At its core, sand casting is the process of creating a mold from sand and then pouring molten metal into that mold to create a part or component. The sand used in this method can vary but typically consists of silica sand that is mixed with other materials like clay and water to help bind it together. Once the sand mold is created, it can withstand the high temperatures of molten metal, allowing for the casting process to occur.
The Sand Casting Process
The sand casting process can be broken down into several key steps
1. Pattern Making The first step involves creating a pattern, which is a replica of the final product. Patterns are usually made from materials such as wood, metal, or plastic. The pattern needs to account for the shrinkage that occurs when the metal cools and solidifies.
2. Mold Creation Once the pattern is ready, it is used to create a mold. This is done by placing the pattern in a box known as a flask, which is then filled with a mixture of sand and a binding agent. The mixture is compacted around the pattern to form the mold. After the sand hardens, the pattern is removed, leaving a hollow cavity that reflects the shape of the desired part.
3. Core Making In some cases, additional cores made of sand are inserted into the mold to create internal features or complex geometries. Cores are also made from sand and are designed to be easily removable after the metal has cooled and solidified.
sand casting definition
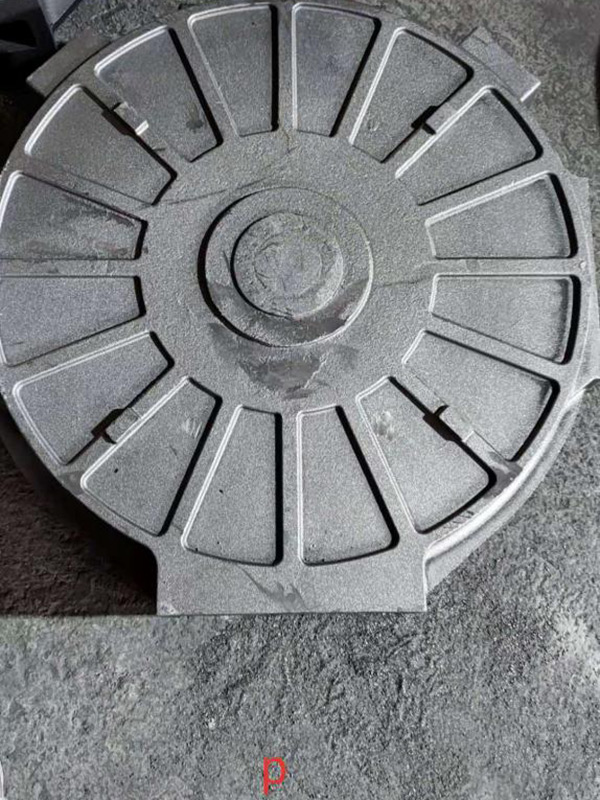
4. Melting and Pouring The next step is to melt the metal, which can be done using various methods such as induction melting or cupola furnaces. Once in a liquid state, the molten metal is carefully poured into the mold cavity through a system of channels known as gates.
5. Cooling After the molten metal is poured, it is allowed to cool and solidify. The cooling time can vary depending on the size and thickness of the casting, as well as the type of metal being used.
6. Mold Removal Once the metal has cooled sufficiently, the sand mold is broken away to reveal the cast part. This usually involves shaking or vibrating the mold to dislodge the sand, which can then be reused.
7. Finishing The last step involves cleaning and finishing the cast part. This can include processes such as grinding, sanding, and machining to ensure that the part meets the required specifications and surface finish.
Advantages of Sand Casting
One of the primary advantages of sand casting is its ability to produce large and complex parts at a lower cost compared to other casting methods. The materials used for molds are inexpensive and readily available, making it accessible for various production scales. Additionally, sand casting can accommodate a wide range of metals, including aluminum, bronze, iron, and steel.
Moreover, sand casting is highly adaptable; changes to the design can be relatively easy to implement. The process also allows for the production of multiple castings from a single mold, optimizing efficiency and reducing waste.
Conclusion
In summary, sand casting is a fundamental manufacturing process that has stood the test of time. Its definition as a shaping method for molten metal using sand molds highlights its importance in producing both simple and complex parts across various industries. As technology evolves, innovations in sand casting are likely to enhance its efficiency, precision, and environmental sustainability, further solidifying its role in modern manufacturing. Whether for small-scale applications or large industrial components, sand casting remains a critical process worth understanding in the vast landscape of metallurgy and production.
Post time:des . 04, 2024 18:13
Next:3d printing for sand casting