Sand Casting 101 An Introductory Guide
Sand casting is one of the oldest and most versatile methods for manufacturing metal parts. It plays a crucial role in various industries, including automotive, aerospace, and machinery. This article explores the fundamental aspects of sand casting, highlighting its processes, advantages, and applications.
What is Sand Casting?
Sand casting is a process that involves creating a mold from sand and then pouring molten metal into this mold to produce a desired shape. The mold is usually made from a mixture of sand, clay, and water, which forms a cohesive structure capable of holding the shape of the desired part. Once the molten metal cools and solidifies, the mold is broken away to reveal the cast part.
The Sand Casting Process
The sand casting process generally involves several key steps
1. Pattern Making The first step is to create a pattern, usually made from wood, metal, or plastic, which replicates the shape of the desired final product. This pattern is used to create the mold cavity.
2. Mold Creation The pattern is then placed in a box, and sand mixed with a binding agent is packed around it. Once the sand is compacted, the pattern is removed, leaving a cavity in the shape of the intended part.
sand casting 101
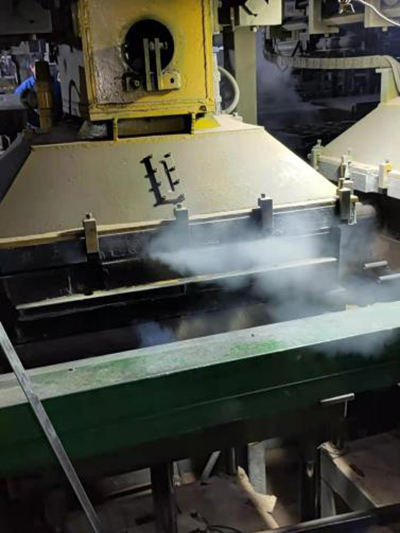
3. Pouring Molten metal is heated to its melting point and poured into the mold cavity. The pouring must be done carefully to avoid defects such as air pockets or uneven surfaces.
4. Cooling and Solidification After the metal has filled the mold, it is allowed to cool and solidify. This process can take anywhere from a few minutes to several hours, depending on the size and thickness of the component.
5. Finishing Once the metal has cooled, the mold is broken apart to retrieve the cast part. Additional finishing processes, such as grinding and polishing, may be required to achieve the desired surface finish and dimensions.
Advantages of Sand Casting
Sand casting offers several advantages. It is relatively inexpensive compared to other casting methods, as it requires minimal tooling. The process is also highly adaptable, making it suitable for a wide range of materials, including aluminum, brass, iron, and steel. Moreover, sand casting can produce both large and small parts, making it ideal for both prototyping and mass production.
Applications
Due to its versatility, sand casting is widely used in several applications, from producing intricate engine components to large machinery parts. Its capacity to create complex shapes makes it invaluable in various engineering fields.
In conclusion, sand casting remains a cornerstone of metal manufacturing, combining simplicity with versatility. Understanding its process, benefits, and applications can help manufacturers leverage this age-old technique effectively.
Post time:nóv . 18, 2024 22:54
Next:can you sand resin