Metal Sand Casting An Overview of the Process, Benefits, and Applications
Metal sand casting is a time-honored manufacturing process that involves pouring molten metal into a sand mold to produce intricate metal parts. This versatile technique is widely used across various industries due to its ability to create complex shapes and the cost-effectiveness of the materials used. In this article, we will explore the process of metal sand casting, its advantages, and its diverse applications.
The Sand Casting Process
The metal sand casting process begins with the creation of a mold. This is typically achieved by compacting sand around a pattern of the desired object. The pattern is usually made of metal or plastic and is designed to be slightly larger than the final product to account for the shrinkage of the metal as it cools. The sand used in the process is often mixed with a binding agent, such as clay, which helps hold the sand grains together.
Once the sand mold is prepared, it is parted to remove the pattern, leaving a cavity in the shape of the object to be created. The next step involves pouring molten metal into the cavity. The metal may be in a liquid state form, achieved by melting through various means such as induction, resistance, or electric arc furnaces. It’s important for the molten metal to be poured at the right temperature and consistency to ensure a quality cast.
After allowing sufficient time for the metal to cool and solidify, the mold is broken apart, and the cast part is removed. This process may involve further machinery to trim excess material, smooth surfaces, or drill holes, thereby refining the finished product.
Benefits of Sand Casting
One of the primary advantages of metal sand casting is its flexibility in production. It can accommodate a variety of metals, including aluminum, copper, iron, and steel, making it suitable for an extensive range of applications. Additionally, the sand molds can be reused many times, although the exact number of uses may vary based on the design and quality of the sand.
Cost-effectiveness is another significant benefit. The materials used in sand casting, primarily sand and metal, are relatively inexpensive compared to other casting methods such as die casting. This makes it an attractive option for low to medium production runs where the volume does not justify the high costs of other casting techniques.
metal sand casting
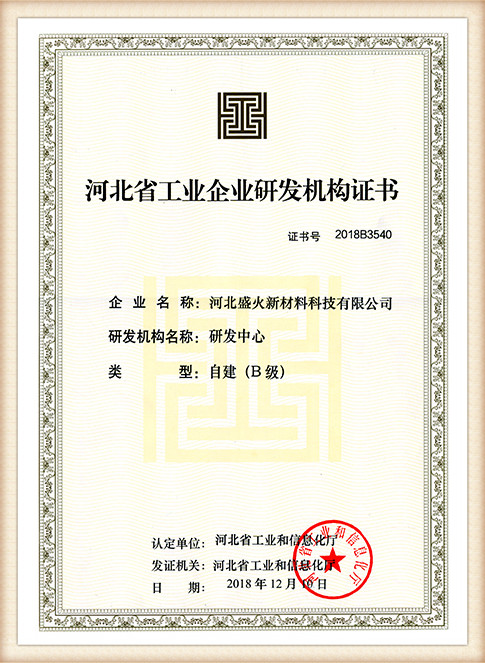
Moreover, sand casting allows for complex shapes that are often challenging to achieve using other methods. The ability to produce large components with intricate details makes it a preferred choice for many industries, especially where precision is crucial.
Applications of Metal Sand Casting
Metal sand casting has found its niche across various sectors. The automotive industry, for instance, leverages this method to create engine blocks, cylinder heads, and transmission cases. The ability to produce large, heavy parts economically is vital in a sector that prioritizes efficiency and ruggedness.
In the aerospace industry, sand casting is employed to manufacture components such as structural frames and housing parts. The lightweight yet robust nature of cast aluminum parts produced through sand casting lends well to the performance requirements of aircraft.
The construction industry also benefits from sand casting, especially in the production of decorative elements, fittings, and hardware. The versatility of the casting process allows architects to bring their designs to life with an artistic touch.
Finally, the machinery and equipment sector relies heavily on metal sand casting for producing parts like gears, pumps, and housings. The durability and reliability of cast components ensure that machinery operates efficiently under varying conditions.
Conclusion
Metal sand casting is a foundational manufacturing process that has stood the test of time. Its combination of flexibility, cost-effectiveness, and ability to produce complex shapes makes it a preferred method for many industries. Whether in automotive, aerospace, construction, or machinery, the applications of sand casting are extensive and continue to evolve with advancements in materials and technologies. As industries seek innovative ways to enhance production efficiency and reduce costs, the relevance of metal sand casting remains strong, proving its importance in modern manufacturing.
Post time:nóv . 24, 2024 15:52
Next:sand casting metal process