The Importance of Quality Metal Casting Sand in Foundry Operations
When it comes to metal casting, one of the most critical materials used is foundry sand. This essential component plays a pivotal role in the quality and success of metal casting processes. With the growing demand for high-performing products in various industries, the search for quality metal casting sand for sale has intensified. In this article, we will discuss the different types of casting sand, their properties, and the importance of sourcing high-quality material for foundry operations.
Types of Metal Casting Sand
Foundry sand is generally categorized into several types, each designed for specific casting applications. The three primary types of sand used in metal casting are
1. Silica Sand Silica sand is the most commonly used casting sand. Its high melting point, excellent thermal conductivity, and good flowability make it suitable for producing intricate designs and shapes. However, silica sand poses risks related to respirable crystalline silica dust, necessitating safety measures for workers.
2. Clay-Based Sand This type of sand is primarily composed of clay minerals, which provide excellent bonding properties. Clay-based sand is often used for making molds and cores. When combined with water, clay-based sands become plastic enough to be shaped into complex designs. The most common type of clay used in these applications is bentonite clay, known for its ability to retain moisture and improve mold strength.
3. Synthetic Sand Synthetic or man-made sands are designed to meet specific casting requirements. Produced from by-products or recycled materials, synthetic sands offer various benefits, including enhanced flowability and lower environmental impact. Additionally, they are engineered to minimize defects and improve the efficiency of the casting process.
Key Properties of Quality Foundry Sand
The properties of casting sand greatly influence the performance of the metal casting process. When sourcing sand, several key characteristics should be considered
metal casting sand for sale
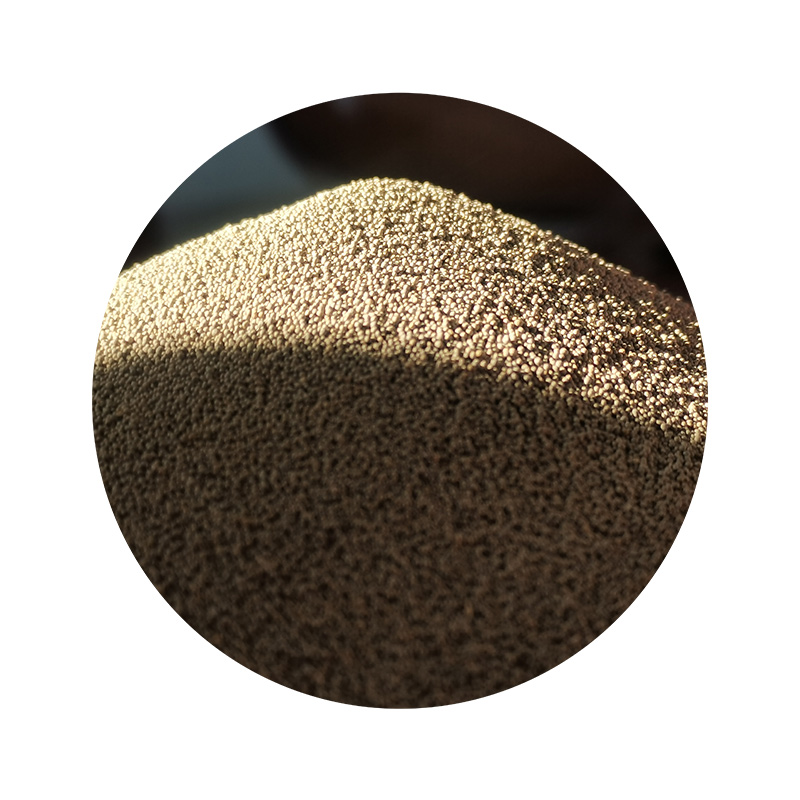
1. Grain Shape and Size The shape and size of the sand grains are crucial for mold integrity and the final quality of the cast product. Ideal sand grains should be round or sub-angular and contain a uniform size distribution to ensure proper packing and minimize voids.
2. Chemical Composition High-quality casting sand should have a low impurity level, particularly concerning iron and other contaminants. The chemical composition affects the melting point and the interaction with molten metal, directly influencing the outcome of the casting.
3. Moisture Content Proper moisture levels in sand are important to achieve the right balance between mold strength and flexibility. Sand that is too dry may lead to cracking during the casting process, while overly wet sand can lose shape and structural integrity.
4. Flowability and Compactability Good foundry sand should easily flow into molds and compact tightly to form a solid structure. This ensures that fine details in the mold are captured accurately, resulting in high-quality casts.
The Importance of Sourcing Quality Sand
Sourcing quality metal casting sand for sale is vital for any foundry operation. Using inferior materials can lead to defects in the final product, increased production costs, and even safety risks. Quality sand ensures that the molds can withstand high temperatures without deformation, promotes better surface finishes, and minimizes the risk of inclusions and other casting defects.
Moreover, investing in quality sand can lead to long-term savings. By reducing scrap rates and increasing the efficiency of the casting process, foundries can significantly lower production costs over time. This not only improves profit margins but also enhances competitiveness in the market.
In conclusion, the pursuit of quality metal casting sand is a critical consideration for any foundry operation. Understanding the types of casting sands available, their properties, and the benefits of sourcing high-quality materials is essential for achieving successful casting outcomes. As the demand for precision-engineered products continues to rise, foundries must prioritize quality in every aspect of the production process, starting with the materials they choose to use.
Post time:nóv . 12, 2024 07:49
Next:sand casting processes