Understanding Metal Casting Sand Essential Material in Foundry Processes
Metal casting is a fundamental process in manufacturing that involves pouring molten metal into a mold to create various components and structures. Among the essential materials used in this process, casting sand plays a crucial role. This article delves into the significance, types, properties, and applications of casting sand in the metal casting industry.
Casting sand is primarily a mixture of fine aggregates, predominantly silica, and other additives designed to meet specific casting requirements. The properties of casting sand directly affect the quality of the final castings, making its selection and preparation paramount in the foundry.
Understanding Metal Casting Sand Essential Material in Foundry Processes
Another important type of casting sand is resin-coated sand, which is pre-coated with a phenolic resin. This type of sand is used in shell molding, where a thin shell of resin-coated sand is formed on a heated pattern. The resultant mold has a highly smooth finish, leading to reduced machining requirements on the finished product. This method is gaining popularity due to its ability to produce high-dimensional accuracy and excellent surface finish.
metal casting sand
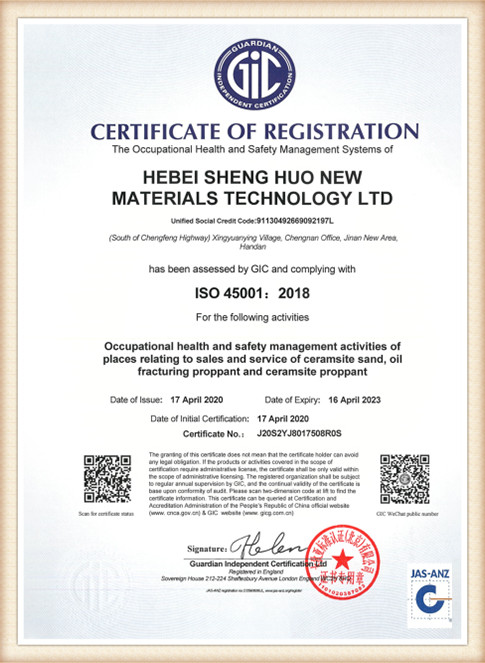
The properties of casting sand can greatly impact the overall casting process. Factors such as grain size, shape, and distribution play a vital role in determining the sand's permeability, strength, and thermal conductivity. For example, coarser sand allows for better gas escape during solidification, reducing the likelihood of casting defects such as porosity. Conversely, finer sand can create a smoother surface finish, which is advantageous for aesthetic components.
Moisture content is another critical aspect of casting sand. Adequate moisture levels are necessary to achieve optimal bonding between sand grains. If the sand is too dry, it can lead to a brittle mold that fails to maintain its shape. On the other hand, overly moist sand can result in mold collapse or the formation of defects in the final casting. Therefore, maintaining the right balance is essential for successful casting.
In addition to traditional green sand and resin-coated sand, other specialized types of casting sand are being developed to enhance specific casting characteristics. For instance, some foundries utilize zircon sand for its high thermal stability and resistance to chemical reactions with molten metal. This type of sand is particularly beneficial in applications involving reactive metals such as titanium and magnesium.
The applications of casting sand extend beyond simple metal components. Industries such as automotive, aerospace, and heavy machinery rely heavily on foundries to produce complex parts with precise specifications. High-quality casting sand contributes to the overall efficiency of these processes, reducing waste and improving the durability of the end products.
In conclusion, casting sand is an indispensable material in metal casting processes. Understanding its various types, properties, and applications enables foundry engineers to optimize their production methods and achieve superior casting quality. As technology evolves, innovations in casting sand formulations are likely to emerge, offering even greater possibilities in the realm of metal casting. The importance of casting sand will undoubtedly continue to be a cornerstone in the ongoing development of manufacturing processes across various industries.
Post time:sep . 29, 2024 02:33
Next:Sanding Techniques for Cast Iron Surfaces to Enhance Finish and Durability