Materials Used for Sand Casting
Sand casting, one of the oldest and most versatile metal casting processes, has been widely adopted in various industries due to its ability to produce intricate shapes and large parts with ease. The fundamental principle behind this method is the use of a sand mixture, which serves as the mold for molten metal. The materials used in sand casting are critical to the quality and efficiency of the final product. This article explores the key components and materials involved in the sand casting process.
1. Sand
Silica sand is the primary material used in sand casting. It is a fine, granular material that possesses excellent thermal stability and is readily available, making it the top choice for many foundries. The grain size of the sand plays a crucial role in determining the surface finish of the final casting. Smaller grains can produce a smoother finish, while larger grains result in a rougher surface. In addition to silica, some foundries also use other types of sand, such as zircon sand or olivine sand, which offer specific advantages, such as improved thermal properties or lower moisture absorption.
2. Binders
To create a stable mold, sand grains must be bound together. This is achieved by using binders, which are materials that, when mixed with sand, create a coherent structure capable of holding its shape during the metal pouring process. The most common binders used in sand casting include clay, oil, and synthetic resins. Bentonite clay is often utilized due to its excellent bonding properties and its ability to retain moisture, which helps to prevent cracking of the mold. Oil-based binders, such as those made from linseed oil, offer greater flexibility and durability. Moreover, newer synthetic resin binders, like phenolic resins, provide enhanced strength and minimize gas porosity in castings.
3. Additives
materials used for sand casting
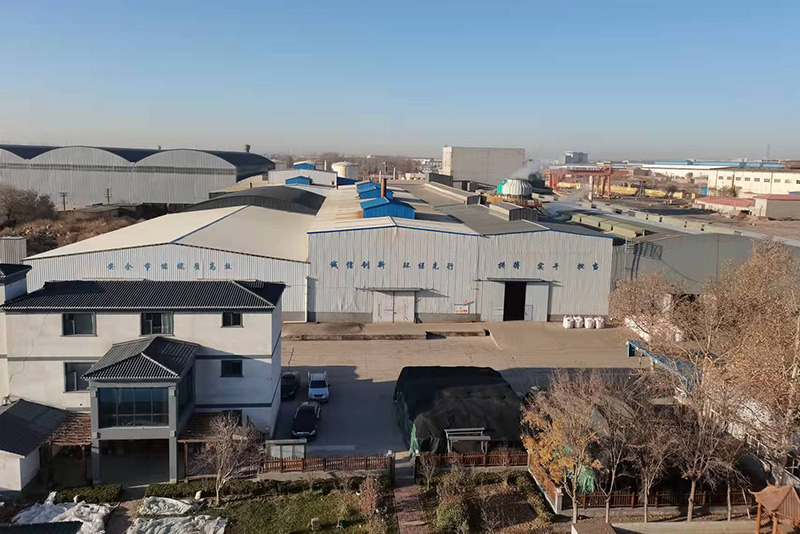
Additives are materials that can be mixed with sand to enhance certain properties of the mold. Common additives include coal dust, which helps to improve the thermal conductivity of the mold and reduces the likelihood of defects such as burn-on. Other additives might include wetting agents that improve the binding capacity of sands, or anti-foaming agents that help to manage gas release during the casting process. These additives are critical for fine-tuning the mold characteristics, ensuring that it meets the specific requirements of the casting project.
4. Metal Alloys
The choice of metal alloy significantly affects the characteristics of the final casting. While a wide range of metal alloys can be used in sand casting, some of the most popular include aluminum alloys, iron alloys, and copper alloys. Aluminum alloys are favored for their lightweight and corrosion-resistant properties, making them ideal for applications in the automotive and aerospace industries. Iron alloys, particularly gray iron, are known for their excellent castability and machinability, commonly used in various mechanical components. Copper alloys, primarily bronze, offer superior wear resistance and are often used for artistic and decorative castings.
5. Water
Water is a crucial component in the sand casting process, primarily for its role in keeping the mold material pliable and aiding in the curing of binders. The moisture content in the sand mixture must be carefully controlled. Too little moisture can cause the mold to crack, while too much moisture can lead to casting defects like blowholes. The expertise in maintaining the right moisture level is essential for achieving a successful casting.
Conclusion
In conclusion, the materials used in sand casting are diverse and play a pivotal role in the overall quality and reliability of cast parts. From the silica sand that forms the base of the mold to the binders and additives that enhance its structural integrity, each component contributes uniquely to the process. Furthermore, the selection of appropriate metal alloys and the careful management of water content are paramount in achieving the desired properties in the final casting. As industries continue to evolve, the materials used in sand casting will also adapt, presenting new opportunities and challenges for manufacturers in their quest for innovation and efficiency.
Post time:nóv . 08, 2024 22:20
Next:sand 3d print