Iron Sand Casting A Time-Honored Method for Metal Fabrication
Iron sand casting is a traditional manufacturing process that has stood the test of time, providing a reliable means of producing complex metal parts with varied applications. This age-old technique, rooted in ancient practices, has evolved over the years, integrating modern technologies while still retaining its fundamental principles. The use of iron sand for casting reflects both a resourceful approach to material selection and an efficient method for fabricating durable metal components.
What is Iron Sand Casting?
Iron sand casting involves creating metal parts by pouring molten iron into a mold made from sand mixed with a binding agent. The primary ingredient in the sand is usually a type of iron oxide, which gives it a unique color and characteristic that makes it ideal for casting operations. The sand forms a mold when compacted around a pattern of the desired part, allowing intricate designs and features to be captured in the final product.
The process begins with the preparation of the mold, which is typically made from a mixture of silica sand and other additives to improve binding and durability. A pattern, usually made from a more rigid material like wood or metal, is placed into the sand mixture to create an impression. Once the mold is formed and set, molten iron is poured into the cavity, filling it completely. After the iron cools and solidifies, the mold is broken away, revealing the finished casting.
Benefits of Using Iron Sand for Casting
The use of iron sand in casting offers several advantages. Firstly, iron sand is abundant in nature, making it a cost-effective material choice. Unlike other materials that may require extensive processing or sourcing, iron sand can often be found in large quantities, particularly in coastal areas or riverbeds.
iron sand casting
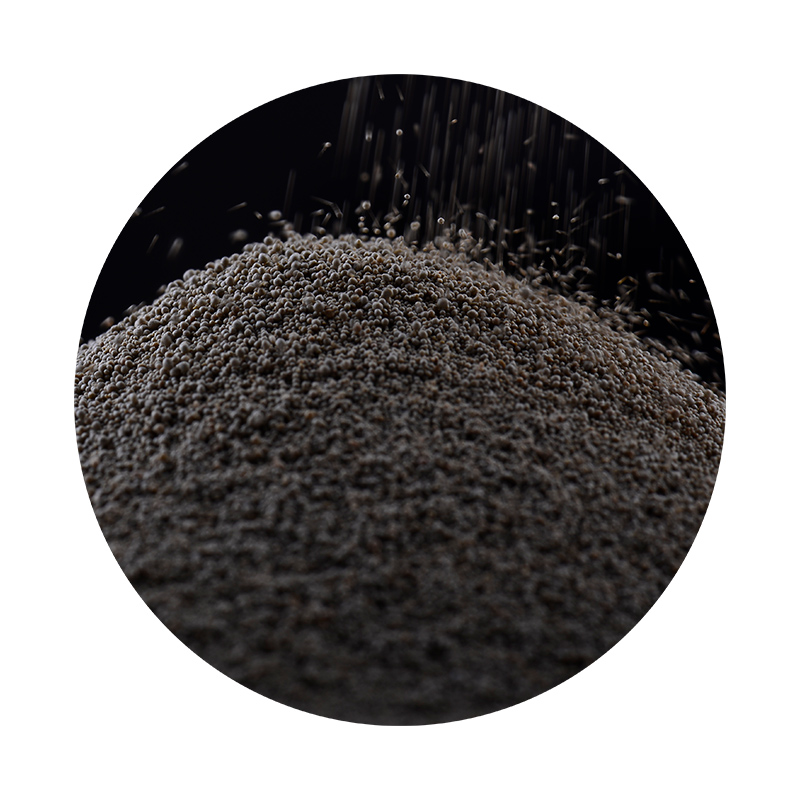
Secondly, the casting process itself provides remarkable design flexibility. Complex geometries, intricate details, and varying wall thicknesses can be achieved, which is particularly important in industries such as automotive, aerospace, and art. This versatility allows manufacturers to meet specific design requirements without needing extensive machining or additional operations.
Moreover, iron sand casting is recognized for its mechanical properties
. Cast iron, for example, demonstrates superior wear resistance, excellent strength, and ease of machining, making it a favored choice for a range of applications, from engine blocks to decorative art pieces. The inherent properties of iron enhance the durability and longevity of the finished products, which is crucial for components subjected to wear and stress.Environmental Considerations
In recent years, there has been a growing awareness of environmental sustainability in manufacturing. Iron sand casting is increasingly being viewed through this lens. The process generates relatively low emissions compared to other metal fabrication techniques, particularly when utilizing modern technologies that emphasize efficiency and waste reduction. Additionally, as industries move toward more sustainable practices, the reuse of sand and recycling of castings has become more common, further diminishing the environmental footprint of the casting process.
Conclusion
Iron sand casting is a remarkable blend of ancient craftsmanship and modern manufacturing. It underscores a deep-seated tradition while adapting to contemporary demands for efficiency and sustainability. As industries continue to seek innovative ways to produce high-quality, durable components, iron sand casting remains a key method, one that honors its past while looking forward to future advancements. With its unique advantages, this technique will likely persist as a cornerstone of metal fabrication, bridging the gap between historical practices and modern engineering challenges. In a world driven by innovation, iron sand casting stands as a testament to the enduring nature of tried-and-true manufacturing methods, showcasing the beauty and utility of metalwork at its finest.
Post time:okt . 13, 2024 13:50
Next:Specifications for Foundry Sand Quality and Performance Standards